An Order Is Subdivided Into Several
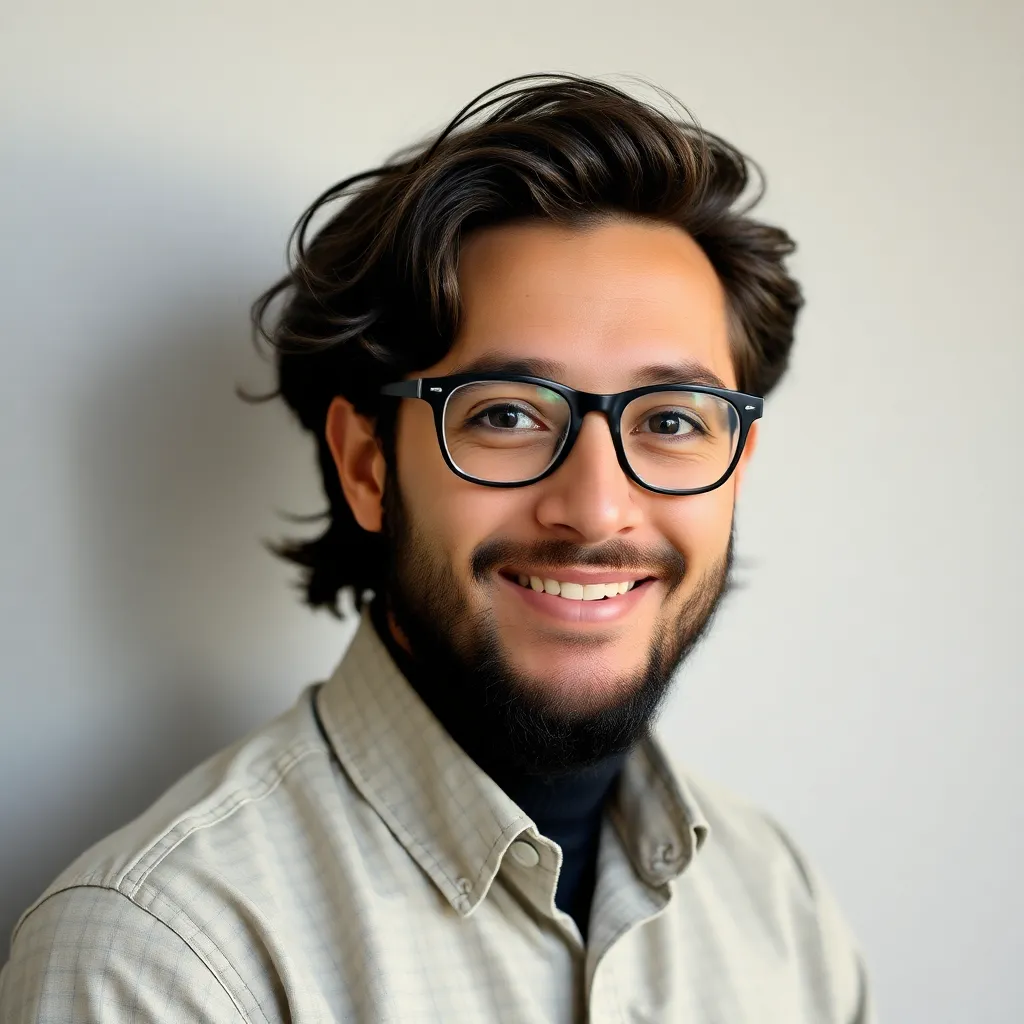
Muz Play
May 11, 2025 · 6 min read

Table of Contents
An Order is Subdivided: Exploring the Complexities of Order Fulfillment
In the dynamic world of e-commerce and supply chain management, understanding the intricacies of order fulfillment is paramount to success. While the concept of an order might seem simple – a customer requests a product, and a business provides it – the reality is far more nuanced. Frequently, a single order is subdivided into several smaller units for efficient processing, shipping, and delivery. This subdivision, while often invisible to the customer, is a critical component ensuring timely and cost-effective order fulfillment. This article delves deep into the reasons behind order subdivision, the various methods employed, and the implications for businesses of all sizes.
Why Subdivide an Order?
The decision to subdivide an order isn't arbitrary; it's a strategic choice driven by several key factors aiming to optimize the entire fulfillment process. Let's examine the primary reasons:
1. Inventory Management and Stock Optimization:
Efficient Warehouse Operations: Large orders containing multiple items often necessitate splitting them based on warehouse location. If items reside in different warehouses, subdividing the order allows for parallel processing, reducing overall fulfillment time. Instead of waiting for all items to converge at a single location, each sub-order is processed from its respective warehouse, significantly speeding up the process.
Minimizing Stockouts: Subdivision enables better inventory control. By tracking each item within a subdivided order, businesses can identify potential stockouts more effectively. If one item within an order is out of stock, only that specific sub-order is delayed, minimizing disruption to the rest of the order's fulfillment.
2. Optimized Shipping and Transportation Costs:
Consolidated Shipping: Shipping multiple small packages can be significantly more expensive than shipping a single larger one. Subdivision allows for consolidating smaller items into larger shipments, reducing overall shipping costs. This is especially crucial for businesses dealing with large volumes of orders.
Utilizing Different Shipping Carriers: Subdividing an order allows businesses to leverage different shipping carriers based on cost-effectiveness and delivery speed. For example, heavier items might be shipped via ground transportation, while smaller, less bulky items might be shipped via express mail.
Improved Delivery Time: By optimizing shipping routes and utilizing different carriers, businesses can reduce overall delivery time. Subdividing the order allows for greater flexibility in routing, potentially leading to faster and more efficient deliveries.
3. Improved Customer Satisfaction:
Faster Partial Shipments: Subdividing an order allows for the possibility of partial shipments. If certain items within an order are ready to ship earlier, they can be sent immediately, improving customer satisfaction. This "partial shipment" strategy keeps the customer informed and engaged throughout the fulfillment process.
Reduced Risk of Damage: Shipping individual smaller packages minimizes the risk of damage during transit. If one package gets damaged, only that specific part of the order is affected, limiting the overall impact on the customer.
4. Enhanced Order Tracking and Visibility:
Improved Transparency: Subdivision provides greater transparency into the order fulfillment process. Each sub-order can be tracked individually, providing a clearer picture of its status. This enhanced visibility improves communication with the customer and keeps them updated on the order's progress.
Streamlined Returns and Exchanges: If a customer needs to return or exchange an item, the subdivision allows for easier identification and processing of the affected sub-order, minimizing disruption to the remaining items within the original order.
Methods of Order Subdivision
The specific approach to order subdivision varies significantly depending on factors like order size, product type, warehouse configuration, and business processes. Here are some common methods:
1. By Product Type:
This approach groups items of the same type together into sub-orders. This is particularly useful if products require different handling, packaging, or shipping methods. For example, fragile items might be grouped into one sub-order while non-fragile items are grouped into another.
2. By Warehouse Location:
When items are stored in different warehouses, subdividing the order by warehouse location is crucial. This allows parallel processing and avoids delays associated with consolidating items from multiple locations.
3. By Shipping Carrier:
Grouping items based on the most efficient shipping carrier for that specific item size and weight can optimize shipping costs. This method is especially useful for businesses dealing with a diverse range of products with varying shipping requirements.
4. By Customer Request:
In some cases, customers may request specific delivery dates or methods for certain items within their order. Subdivision allows for tailoring the fulfillment process to meet these individual customer requirements.
5. Automated Order Subdivision Systems:
Sophisticated businesses often employ automated systems that intelligently subdivide orders based on a combination of factors, such as inventory levels, shipping costs, and delivery times. These systems analyze various data points to optimize the fulfillment process, minimizing manual intervention and maximizing efficiency.
The Impact of Order Subdivision on Business Operations
Implementing an effective order subdivision strategy significantly impacts multiple aspects of business operations.
1. Increased Efficiency and Productivity:
Subdivision streamlines the fulfillment process, leading to increased efficiency and productivity throughout the entire supply chain. Parallel processing of sub-orders reduces overall processing time and frees up resources for other tasks.
2. Reduced Operational Costs:
By optimizing shipping costs and improving inventory management, order subdivision contributes to a significant reduction in overall operational costs. Efficient resource allocation and minimized waste further contribute to cost savings.
3. Enhanced Customer Satisfaction:
Faster delivery times, improved communication, and reduced risk of damage contribute to a significant increase in customer satisfaction. The transparency provided by individual sub-order tracking keeps customers informed and engaged.
4. Improved Scalability and Growth:
A robust order subdivision strategy is crucial for scaling business operations. As order volume increases, the ability to efficiently process and manage subdivided orders becomes increasingly important for maintaining service levels and supporting business growth.
Challenges and Considerations
While order subdivision offers numerous benefits, businesses must also be aware of potential challenges:
1. Increased Complexity:
Managing multiple sub-orders increases operational complexity, requiring robust inventory management systems and efficient tracking mechanisms. Careful planning and integration of systems are essential to avoid confusion and errors.
2. Potential for Errors:
The increased complexity of managing multiple sub-orders increases the potential for errors in order processing, packing, and shipping. Robust quality control processes and error-checking mechanisms are essential to mitigate this risk.
3. Communication Challenges:
Keeping track of multiple sub-orders and communicating their status to the customer can be challenging. Clear and consistent communication is essential to maintain customer satisfaction and avoid confusion.
4. System Integration:
Integrating various systems, such as warehouse management systems (WMS), transportation management systems (TMS), and order management systems (OMS), is crucial for effective order subdivision. Seamless data flow between these systems is essential to optimize the entire process.
Conclusion: Embracing the Subdivided Order
In conclusion, subdividing an order is not merely a technical detail; it's a strategic approach to optimizing the entire order fulfillment process. By carefully considering the reasons for subdivision, selecting appropriate methods, and addressing potential challenges, businesses can unlock significant improvements in efficiency, cost-effectiveness, and customer satisfaction. The adoption of sophisticated order management systems and streamlined processes is key to maximizing the benefits of order subdivision and thriving in today's competitive landscape. The move towards automation and intelligent order management systems will further revolutionize how businesses approach order subdivision, leading to a future where complex fulfillment is seamless and invisible to the end customer, resulting in a superior buying experience and enhanced business profitability.
Latest Posts
Latest Posts
-
Is Burning Chemical Or Physical Change
May 12, 2025
-
Choose The Logical Binomial Random Variable
May 12, 2025
-
List Two Major Characteristics Of Elements
May 12, 2025
-
Relationship Between Vapor Pressure And Temperature
May 12, 2025
-
How To Find Molar Mass Of Unknown Acid
May 12, 2025
Related Post
Thank you for visiting our website which covers about An Order Is Subdivided Into Several . We hope the information provided has been useful to you. Feel free to contact us if you have any questions or need further assistance. See you next time and don't miss to bookmark.