Cost Of Goods Manufactured Journal Entry
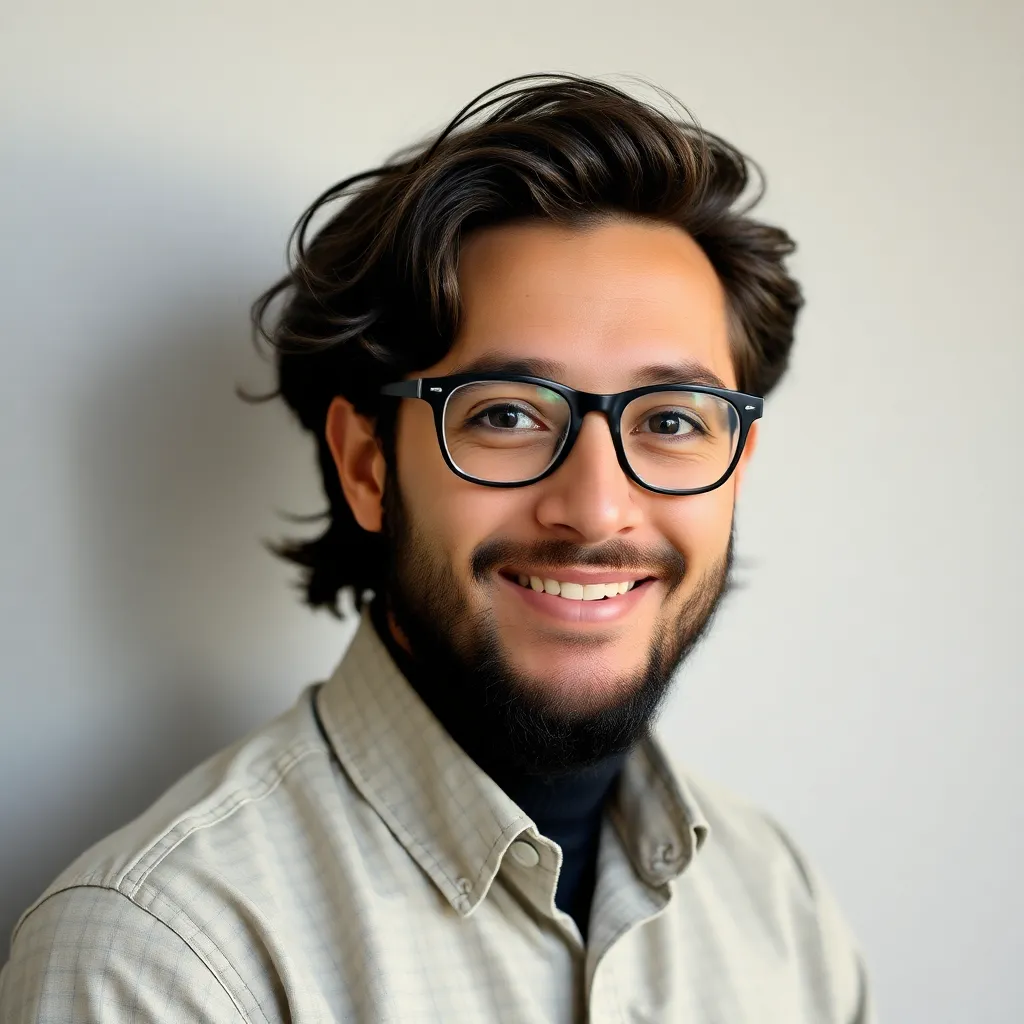
Muz Play
Apr 23, 2025 · 7 min read

Table of Contents
Cost of Goods Manufactured (COGM): A Comprehensive Guide to Journal Entries
Understanding the Cost of Goods Manufactured (COGM) is crucial for businesses that produce their own goods. It represents the total cost of producing finished goods during a specific period. Accurately recording COGM involves several journal entries that track the flow of costs from raw materials to finished products. This comprehensive guide will walk you through the process, explaining the different stages and the corresponding journal entries. We'll also explore the importance of accurate COGM calculation for profitability analysis and decision-making.
Understanding the Components of COGM
Before diving into the journal entries, let's break down the key components that make up the Cost of Goods Manufactured:
1. Direct Materials
These are the raw materials that are directly traceable to the finished product. Examples include wood for furniture, fabric for clothing, or steel for automobiles. The cost of direct materials used in production includes the purchase price, freight-in costs, and any applicable import duties.
2. Direct Labor
This represents the wages and salaries paid to employees directly involved in the production process. This includes assembly line workers, machine operators, and other personnel directly contributing to the creation of the finished good. It excludes indirect labor costs such as supervisors' salaries or maintenance personnel.
3. Manufacturing Overhead
This encompasses all indirect costs associated with the manufacturing process. These costs are not directly traceable to a specific product but are necessary for production. Examples include:
- Indirect Labor: Salaries of supervisors, maintenance personnel, and quality control inspectors.
- Factory Rent: Cost of renting or owning the factory space.
- Utilities: Electricity, gas, and water used in the factory.
- Depreciation: Depreciation of factory equipment and machinery.
- Factory Supplies: Consumables used in the manufacturing process.
- Insurance: Insurance premiums for the factory and equipment.
The Journal Entries Involved in COGM Calculation
The calculation of COGM involves several stages, each requiring specific journal entries. These entries track the flow of costs throughout the manufacturing process. Let's examine these entries in detail:
1. Recording Purchase of Raw Materials
When raw materials are purchased, the journal entry debits the Raw Materials Inventory account and credits the Accounts Payable or Cash account, depending on whether the purchase was made on credit or cash.
Example:
Account Name | Debit | Credit |
---|---|---|
Raw Materials Inventory | $10,000 | |
Accounts Payable | $10,000 | |
To record purchase of raw materials |
2. Recording Direct Materials Used in Production
Once raw materials are used in production, they are transferred from the Raw Materials Inventory account to the Work in Process (WIP) inventory account.
Example:
Account Name | Debit | Credit |
---|---|---|
Work in Process | $8,000 | |
Raw Materials Inventory | $8,000 | |
To record direct materials used in production |
3. Recording Direct Labor Costs
Direct labor costs are debited to the Work in Process inventory account and credited to the Wages Payable or Cash account, depending on the payment method.
Example:
Account Name | Debit | Credit |
---|---|---|
Work in Process | $5,000 | |
Wages Payable | $5,000 | |
To record direct labor costs |
4. Recording Manufacturing Overhead Costs
Manufacturing overhead costs are debited to the Manufacturing Overhead account. The credits vary depending on the nature of the expense, such as Accounts Payable for utilities, Accumulated Depreciation for depreciation, or Cash for factory supplies.
Example (Multiple Overhead Entries):
Entry 1: Factory Rent
Account Name | Debit | Credit |
---|---|---|
Manufacturing Overhead | $1,000 | |
Cash | $1,000 | |
To record factory rent |
Entry 2: Factory Utilities
Account Name | Debit | Credit |
---|---|---|
Manufacturing Overhead | $500 | |
Accounts Payable | $500 | |
To record factory utilities |
Entry 3: Depreciation of Factory Equipment
Account Name | Debit | Credit |
---|---|---|
Manufacturing Overhead | $200 | |
Accumulated Depreciation | $200 | |
To record depreciation of factory equipment |
5. Applying Manufacturing Overhead to Production
Manufacturing overhead is applied to production using a predetermined overhead rate. This rate is calculated at the beginning of the accounting period and is based on an estimated level of overhead costs and an estimated level of activity (e.g., machine hours or direct labor costs). The journal entry debits the Work in Process inventory account and credits the Manufacturing Overhead account.
Example:
Let's assume a predetermined overhead rate of 150% of direct labor costs. Since direct labor costs were $5,000, the applied overhead is $5,000 * 1.50 = $7,500.
Account Name | Debit | Credit |
---|---|---|
Work in Process | $7,500 | |
Manufacturing Overhead | $7,500 | |
To apply manufacturing overhead to production |
6. Completing Production and Transferring to Finished Goods
Once production is complete, the cost of the finished goods is transferred from the Work in Process inventory account to the Finished Goods Inventory account.
Example: Let's summarize the costs accumulated in WIP:
- Direct Materials: $8,000
- Direct Labor: $5,000
- Applied Manufacturing Overhead: $7,500
- Total Cost of Goods Manufactured: $20,500
Account Name | Debit | Credit |
---|---|---|
Finished Goods Inventory | $20,500 | |
Work in Process | $20,500 | |
To transfer completed goods to finished goods inventory |
7. Cost of Goods Sold (COGS)
When finished goods are sold, the cost of those goods is transferred from the Finished Goods Inventory account to the Cost of Goods Sold account.
Example: Assume $18,000 worth of goods were sold.
Account Name | Debit | Credit |
---|---|---|
Cost of Goods Sold | $18,000 | |
Finished Goods Inventory | $18,000 | |
To record cost of goods sold |
Importance of Accurate COGM Calculation
Accurate calculation and recording of COGM is vital for several reasons:
- Inventory Valuation: COGM is a key component in determining the value of the ending finished goods inventory. This affects the company's balance sheet and profitability.
- Cost Control: Tracking COGM helps businesses identify areas where costs can be reduced and efficiency improved. Analyzing direct materials, direct labor, and overhead costs helps pinpoint inefficiencies.
- Pricing Decisions: Accurate COGM data is crucial for setting profitable selling prices. Understanding the true cost of production helps ensure that prices cover all expenses and generate a reasonable profit margin.
- Profitability Analysis: COGM is a crucial element in calculating the gross profit margin, which is a key indicator of a company's profitability. A higher gross profit margin indicates greater efficiency and higher profitability.
- Financial Reporting: COGM is a crucial element in the preparation of the income statement and balance sheet, both of which are essential components of accurate financial reporting and transparency.
Addressing Potential Complications
While the basic process outlined above is straightforward, several factors can complicate COGM calculation:
- Multiple Production Departments: Businesses with multiple production departments need to allocate overhead costs to each department before assigning them to specific products.
- Joint Products and By-products: Companies producing multiple products from a single process need to allocate costs to each product appropriately.
- Process Costing vs. Job Order Costing: Different costing methods (process costing and job order costing) require slightly different approaches to tracking and allocating costs.
Accurate COGM calculation requires careful attention to detail and a thorough understanding of the manufacturing process. Regular review and reconciliation of inventory accounts are crucial for maintaining accuracy and ensuring the reliability of financial statements. This detailed breakdown offers a strong foundation for effectively managing and analyzing the cost of goods manufactured in your business. By diligently tracking these costs, you can make informed decisions to improve profitability and drive sustainable growth.
Latest Posts
Latest Posts
-
Write The Electronic Configuration Of Sodium
Apr 23, 2025
-
Determine What Type Of Reaction Each Unbalanced Chemical Equation Represents
Apr 23, 2025
-
Synapsis Of Homologous Chromosomes And Crossing Over Take Place During
Apr 23, 2025
-
Parts Of Compound Light Microscope And Its Function
Apr 23, 2025
-
Plants That Produce Seeds Within A Cone Are Called
Apr 23, 2025
Related Post
Thank you for visiting our website which covers about Cost Of Goods Manufactured Journal Entry . We hope the information provided has been useful to you. Feel free to contact us if you have any questions or need further assistance. See you next time and don't miss to bookmark.