Difference Between Job Order And Process Costing
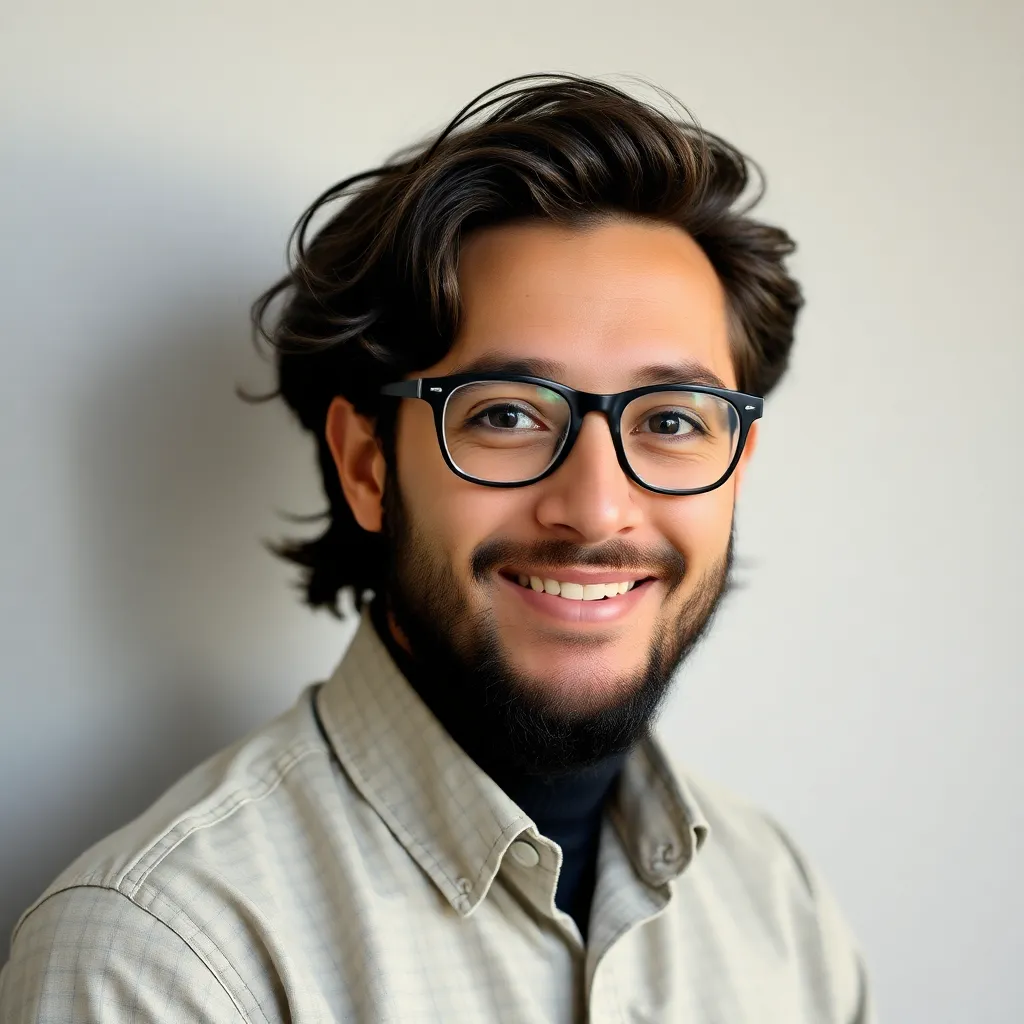
Muz Play
May 09, 2025 · 7 min read
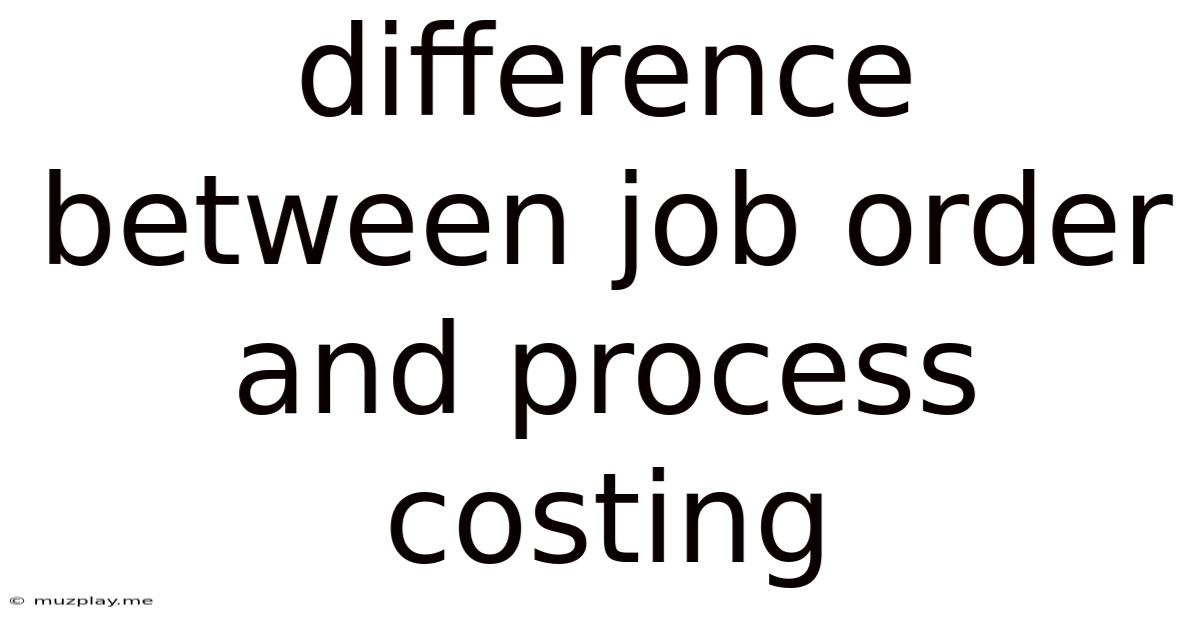
Table of Contents
Job Order Costing vs. Process Costing: A Comprehensive Guide
Choosing the right costing method is crucial for accurate financial reporting and effective managerial decision-making. Two prominent methods, job order costing and process costing, stand out, each suited to different production environments. Understanding their core differences is paramount for businesses to optimize their accounting practices and gain valuable insights into their profitability. This comprehensive guide delves deep into the distinctions between job order and process costing, outlining their applications, advantages, and limitations.
What is Job Order Costing?
Job order costing is a costing method used in situations where unique products or services are produced. Each job or project is treated as a separate cost unit, allowing for detailed tracking of costs associated with each specific order. This meticulous approach is particularly valuable when dealing with customized products, projects with varying complexities, and situations demanding high levels of individual cost control.
Think of a custom home builder. Each house built is a unique job, with its own specific materials, labor hours, and overhead costs. A printing company producing personalized stationery or a bespoke tailor creating custom-made suits would also utilize job order costing. The key characteristic is the individuality of each output.
Key Features of Job Order Costing:
- Individual Job Tracking: Each job is assigned a unique identification number, enabling meticulous tracking of direct materials, direct labor, and manufacturing overhead costs.
- Detailed Cost Records: Comprehensive records are maintained for each job, allowing for precise cost analysis and accurate pricing decisions.
- Cost Accumulation by Job: Costs are accumulated separately for each job, providing detailed cost information for each individual project.
- Suitable for Customized Products: Ideal for businesses producing unique, customized products or services where each job differs significantly from others.
- Direct Cost Tracing: Direct costs are easily traced to specific jobs, simplifying cost allocation.
How Job Order Costing Works:
- Job Cost Sheet: A job cost sheet is created for each job, serving as a central repository for all costs associated with that specific order.
- Cost Accumulation: Direct materials, direct labor, and manufacturing overhead costs are accumulated on the job cost sheet.
- Overhead Allocation: Manufacturing overhead costs are allocated to each job based on a predetermined overhead rate, which may be based on direct labor hours, machine hours, or other appropriate allocation bases.
- Cost Reconciliation: At the completion of the job, the total costs are summarized on the job cost sheet, providing a comprehensive picture of the cost of the completed job.
- Costing of Goods Sold (COGS): When a job is completed and sold, its cost is transferred from work-in-progress (WIP) inventory to the cost of goods sold (COGS) account.
What is Process Costing?
Process costing is employed in manufacturing environments where homogeneous products are produced in large quantities. Unlike job order costing, where individual jobs are tracked, process costing focuses on calculating the average cost of producing a unit of product over a specific period. This method is particularly efficient for mass production scenarios where individual product tracking is impractical or excessively costly.
Imagine a beverage manufacturer producing thousands of identical bottles of soda daily. Or a cement factory churning out tons of cement. The products are virtually identical, making individual cost tracking unnecessary. Process costing simplifies the accounting process in these high-volume, standardized production settings.
Key Features of Process Costing:
- Averaging Costs: Costs are averaged across a large volume of identical products, simplifying the cost accounting process.
- Mass Production Focus: Primarily suited for industries with high-volume, standardized production.
- Production Departments: Costs are accumulated by production department, providing insights into departmental efficiency and cost drivers.
- Cost per Unit Calculation: The primary output is the cost per unit of product, offering valuable data for pricing and profitability analysis.
- Equivalent Units: A crucial concept in process costing, equivalent units represent the number of fully completed units that could have been produced given the current stage of completion of partially finished units.
How Process Costing Works:
- Cost Accumulation: Costs are accumulated by production department, including direct materials, direct labor, and manufacturing overhead.
- Equivalent Units Calculation: Equivalent units are calculated for both direct materials and conversion costs (direct labor and manufacturing overhead) considering the degree of completion of work-in-progress inventory.
- Cost per Equivalent Unit: The total cost for each element (materials and conversion costs) is divided by the equivalent units to determine the cost per equivalent unit.
- Cost Allocation: The cost per equivalent unit is then used to allocate costs to completed units and ending work-in-progress inventory.
- Cost of Goods Sold (COGS): The cost of goods sold is calculated by multiplying the number of units sold by the cost per equivalent unit.
Head-to-Head Comparison: Job Order vs. Process Costing
Feature | Job Order Costing | Process Costing |
---|---|---|
Product Type | Unique, customized products or services | Homogeneous, mass-produced products |
Cost Tracking | Individual jobs | Production departments |
Cost Unit | Individual job | Unit of product |
Cost Calculation | Direct costs directly traced to each job | Average cost per unit over a period |
Overhead Allocation | Specific allocation to each job | Allocation based on production departments |
Inventory Valuation | Specific identification | Weighted-average or FIFO method |
Complexity | More complex, detailed | Simpler, less detailed |
Suitability | Low-volume, high-variety production | High-volume, low-variety production |
Advantages and Disadvantages: Job Order Costing
Advantages:
- Accurate Costing: Provides highly accurate cost information for each individual job, facilitating better pricing decisions and profitability analysis.
- Effective Cost Control: Allows for detailed monitoring of costs, enabling managers to identify and address areas of inefficiency.
- Better Pricing Strategies: Accurate cost data empowers businesses to develop competitive and profitable pricing strategies for customized products.
- Improved Project Management: Offers valuable insights into the performance of individual projects, facilitating better project planning and management.
Disadvantages:
- Time-Consuming: Requires meticulous record-keeping, making it more time-consuming and labor-intensive compared to process costing.
- Costly: Can be expensive to implement and maintain due to the high level of detail required.
- Not Suitable for Mass Production: Not ideal for businesses producing large volumes of identical products.
- Complexity: Can be complex to implement and manage, particularly for businesses with a large number of jobs running concurrently.
Advantages and Disadvantages: Process Costing
Advantages:
- Efficient and Cost-Effective: Requires less record-keeping and less labor than job order costing, making it more efficient and cost-effective for mass production.
- Simple and Easy to Understand: Simpler to implement and manage compared to job order costing, making it easier for businesses to understand and utilize.
- Suitable for Mass Production: Ideal for businesses producing large volumes of identical products.
- Consistent Unit Cost: Provides consistent unit cost information, simplifying pricing decisions and inventory valuation.
Disadvantages:
- Less Accurate Costing: Averages costs across large production runs, potentially leading to less accurate cost information for individual units.
- Limited Cost Control: Lacks the detail needed to pinpoint inefficiencies at the individual product level.
- Not Suitable for Customized Products: Not suitable for businesses producing unique, customized products or services.
- Oversimplification: Can oversimplify cost analysis, potentially masking individual product or department cost variances.
Choosing the Right Costing Method: Key Considerations
The selection between job order and process costing hinges on several key factors:
- Nature of Products: The most critical factor is whether products are unique and customized or homogeneous and mass-produced. Job order costing is for unique items; process costing is for standardized products.
- Production Volume: High-volume production generally favors process costing due to its efficiency. Low-volume, high-variety production better suits job order costing.
- Degree of Customization: Highly customized products necessitate job order costing to accurately track individual costs.
- Cost Tracking Requirements: The level of detail needed for cost tracking influences the choice. Process costing sacrifices detail for efficiency.
- Management Information Needs: The type and depth of information needed for managerial decision-making will guide the appropriate method.
Conclusion
Understanding the fundamental differences between job order and process costing is essential for effective cost accounting and management. The appropriate choice depends entirely on the specific characteristics of the business and its production processes. While job order costing offers detailed cost tracking for unique products, process costing provides an efficient approach for mass production. By carefully considering the factors outlined above, businesses can select the costing method best suited to their needs, ensuring accurate cost data, efficient operations, and informed decision-making. Selecting the correct costing system is not just about accounting accuracy; it's about gaining valuable insights into operational efficiency and overall profitability.
Latest Posts
Latest Posts
-
How To Find A Vector Orthogonal To A Plane
May 09, 2025
-
Acids Increase The Concentration Of What In Water
May 09, 2025
-
Both Protozoans And Algae Are Found In The Kingdom
May 09, 2025
-
What Is Body Mechanics In Nursing
May 09, 2025
-
Describe The Relationship Between Population Density And Population Distribution
May 09, 2025
Related Post
Thank you for visiting our website which covers about Difference Between Job Order And Process Costing . We hope the information provided has been useful to you. Feel free to contact us if you have any questions or need further assistance. See you next time and don't miss to bookmark.