Difference Between Job Order Costing And Process Costing
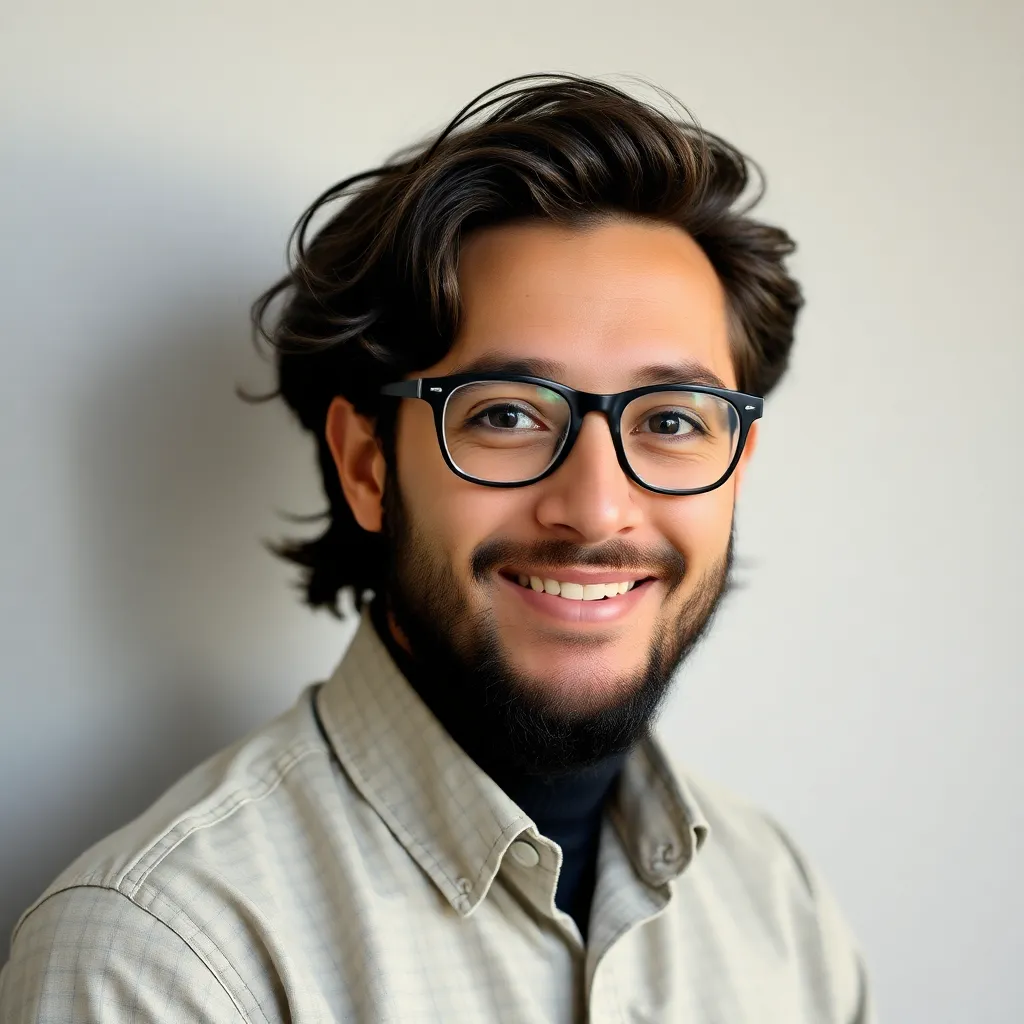
Muz Play
May 09, 2025 · 7 min read
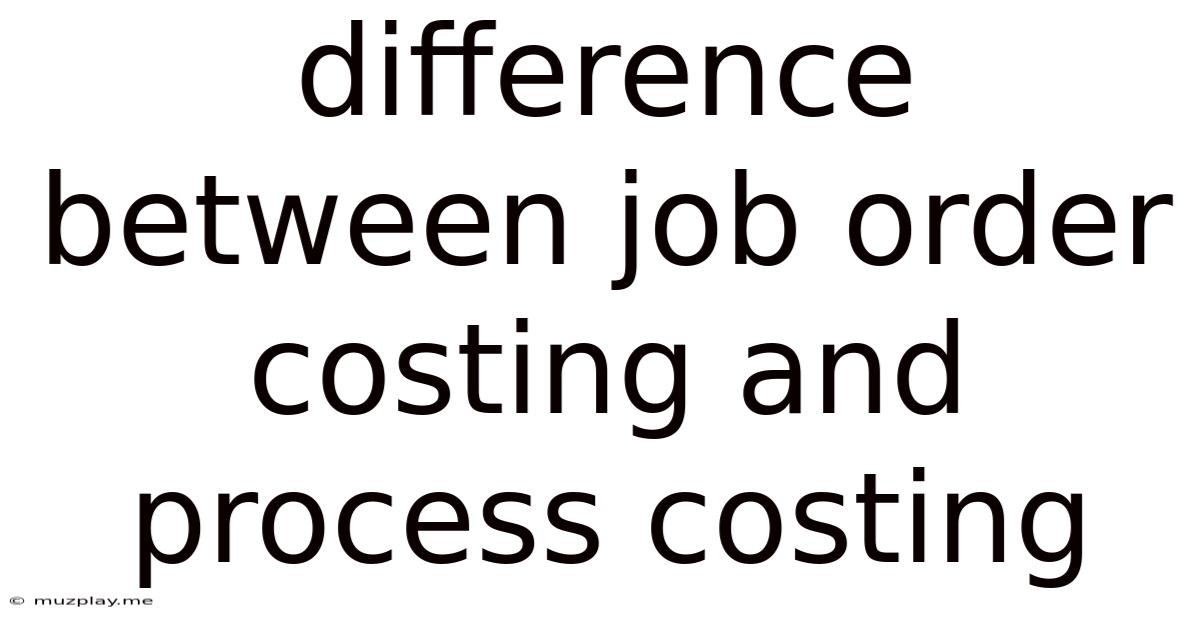
Table of Contents
Job Order Costing vs. Process Costing: A Comprehensive Guide
Choosing the right costing method is crucial for accurate financial reporting and effective decision-making. Two prominent methods are job order costing and process costing. While both aim to determine the cost of goods manufactured, they differ significantly in their application and the types of businesses they suit. This comprehensive guide will delve into the intricacies of each method, highlighting their key differences and helping you determine which one is best for your organization.
Understanding Job Order Costing
Job order costing is a cost accounting system used to assign costs to individual projects or jobs. It's ideal for businesses that produce unique or customized products or services, where each job has distinct characteristics and requires a separate cost calculation. Think of custom-built homes, tailored suits, or specialized software development projects. The key is that each job is treated as a separate entity, and costs are tracked individually for each one.
Key Characteristics of Job Order Costing:
- Individual Job Tracking: Costs are meticulously tracked for each individual job or project throughout its lifecycle. This includes direct materials, direct labor, and manufacturing overhead.
- Unique Products or Services: Best suited for businesses producing non-homogeneous products or services where each job differs significantly from others.
- Detailed Cost Information: Provides a detailed breakdown of costs for each job, enabling accurate pricing, profitability analysis, and performance evaluation.
- Direct Cost Tracing: Direct materials and direct labor are easily traceable to specific jobs.
- Overhead Allocation: Manufacturing overhead is allocated to jobs using a predetermined overhead rate, typically based on a chosen allocation base like direct labor hours or machine hours. This involves calculating a predetermined overhead rate at the beginning of the accounting period (e.g., by dividing estimated overhead costs by estimated allocation base). Then, the overhead cost is applied to individual jobs based on the actual allocation base used by that job.
The Job Cost Sheet: The Heart of Job Order Costing
The job cost sheet is a critical document in job order costing. It serves as a central repository for all costs associated with a particular job. This sheet meticulously records:
- Job Number: A unique identifier for each job.
- Customer Name: Identifies the client for whom the job is being performed.
- Date Started and Completed: Tracks the job's duration.
- Direct Materials: A detailed list of materials used, their quantities, and their costs.
- Direct Labor: Hours worked by each employee on the job and their respective wage rates.
- Manufacturing Overhead: Overhead costs allocated to the job based on the predetermined overhead rate and the actual allocation base consumed.
- Total Job Cost: The sum of direct materials, direct labor, and allocated manufacturing overhead.
Example of Job Order Costing:
Imagine a custom cabinet maker receiving an order for a unique kitchen cabinet. The job cost sheet would track the cost of the wood, hinges, and other materials (direct materials), the labor hours of the carpenter and finisher (direct labor), and a portion of the shop's rent, utilities, and depreciation (manufacturing overhead). By summing these costs, the cabinet maker determines the total cost of producing that specific cabinet.
Understanding Process Costing
Process costing is a cost accounting system used to assign costs to large volumes of homogenous products or services produced through a continuous or repetitive process. This method is best suited for mass production environments where identical or nearly identical units are manufactured in a continuous flow. Think of oil refineries, cement factories, or food processing plants. Costs are averaged across the entire production process, rather than tracked individually for each unit.
Key Characteristics of Process Costing:
- Mass Production: Ideal for businesses producing large quantities of identical or similar products.
- Continuous Production: Suited to continuous or repetitive production processes where units move through various stages.
- Averaged Costs: Costs are averaged across all units produced in a specific period. This leads to a cost per unit calculation.
- Cost Accumulation by Department or Process: Costs are accumulated for each stage or department in the production process.
- Equivalent Units: A crucial concept in process costing. Equivalent units represent the number of finished units that could have been produced given the amount of work performed on partially completed units. This is necessary because some units may be only partially complete at the end of the accounting period.
Calculating Costs in Process Costing:
Process costing involves several steps to determine the cost per unit:
- Calculate Equivalent Units: Determine the equivalent number of completed units based on the degree of completion of work-in-progress.
- Calculate Cost per Equivalent Unit: Divide the total costs (direct materials, direct labor, and manufacturing overhead) incurred in the process by the total equivalent units produced.
- Allocate Costs to Finished Goods and Work-in-Process: Apply the cost per equivalent unit to the number of completed units and the equivalent units in work-in-process to determine the cost of goods manufactured and the cost of ending work-in-process inventory.
Example of Process Costing:
A bakery producing thousands of identical loaves of bread daily would use process costing. The total costs of flour, yeast, sugar, labor, and oven operation are accumulated for a specific period (e.g., a month). These costs are then divided by the total number of loaves produced to determine the cost per loaf. Any partially baked loaves at the end of the month are accounted for using the concept of equivalent units.
Job Order Costing vs. Process Costing: A Detailed Comparison
Feature | Job Order Costing | Process Costing |
---|---|---|
Type of Product | Unique, customized products or services | Homogeneous, mass-produced products or services |
Cost Tracking | Individual job tracking | Cost accumulation by department or process |
Cost Assignment | Direct costs easily traceable to specific jobs | Costs averaged across all units produced |
Cost Calculation | Total cost per job | Cost per unit |
Inventory Valuation | Cost per job | Cost per unit |
Suitability | Custom-made products, consulting services | Mass production, oil refining, food processing |
Complexity | More complex, requires detailed record-keeping | Relatively simpler, less detailed record-keeping |
Overhead Allocation | Based on predetermined overhead rate | Based on production volume or other allocation base |
Choosing the Right Costing Method
The choice between job order costing and process costing depends heavily on the nature of your business and its production process. Consider these factors:
- Product Homogeneity: If you produce unique products, job order costing is appropriate. For mass-produced, identical products, process costing is better.
- Production Process: Continuous and repetitive production processes are well-suited to process costing, while custom projects benefit from job order costing.
- Cost Tracking Needs: If you need detailed cost information for individual projects, job order costing provides that level of granularity. Process costing provides a cost per unit, which is sufficient for many mass production environments.
- Business Size and Complexity: Smaller businesses with fewer projects may find job order costing manageable. Larger businesses with complex production processes may require the efficiency of process costing.
Hybrid Costing Systems: A Practical Approach
In reality, many businesses employ hybrid costing systems, combining elements of both job order and process costing. This approach is particularly useful for businesses with a mix of custom and mass-produced products or those with complex production processes involving multiple stages. For instance, a company might use job order costing for its custom design projects and process costing for its standard product lines.
Conclusion
Understanding the nuances of job order costing and process costing is essential for any business seeking to accurately track its production costs. By carefully considering the characteristics of each method and the nature of your own business, you can select the most appropriate costing system to enhance your financial reporting, improve decision-making, and optimize your overall profitability. Remember to consider the factors outlined above and potentially explore hybrid costing options to find the perfect fit for your unique circumstances. The correct choice will contribute significantly to the accuracy and effectiveness of your cost accounting practices.
Latest Posts
Latest Posts
-
Diagramming A Cross Using A Punnett Square
May 09, 2025
-
Some Advantages Of The Intensification Of Globalization Include
May 09, 2025
-
Why Are Conifers And Cycads Considered Gymnosperms
May 09, 2025
-
How To Factor Trinomials Where A Is Greater Than 1
May 09, 2025
-
Having Two Different Genes For A Trait Sometimes Called Hybrid
May 09, 2025
Related Post
Thank you for visiting our website which covers about Difference Between Job Order Costing And Process Costing . We hope the information provided has been useful to you. Feel free to contact us if you have any questions or need further assistance. See you next time and don't miss to bookmark.