Distillation Is The Separation Of Multiple
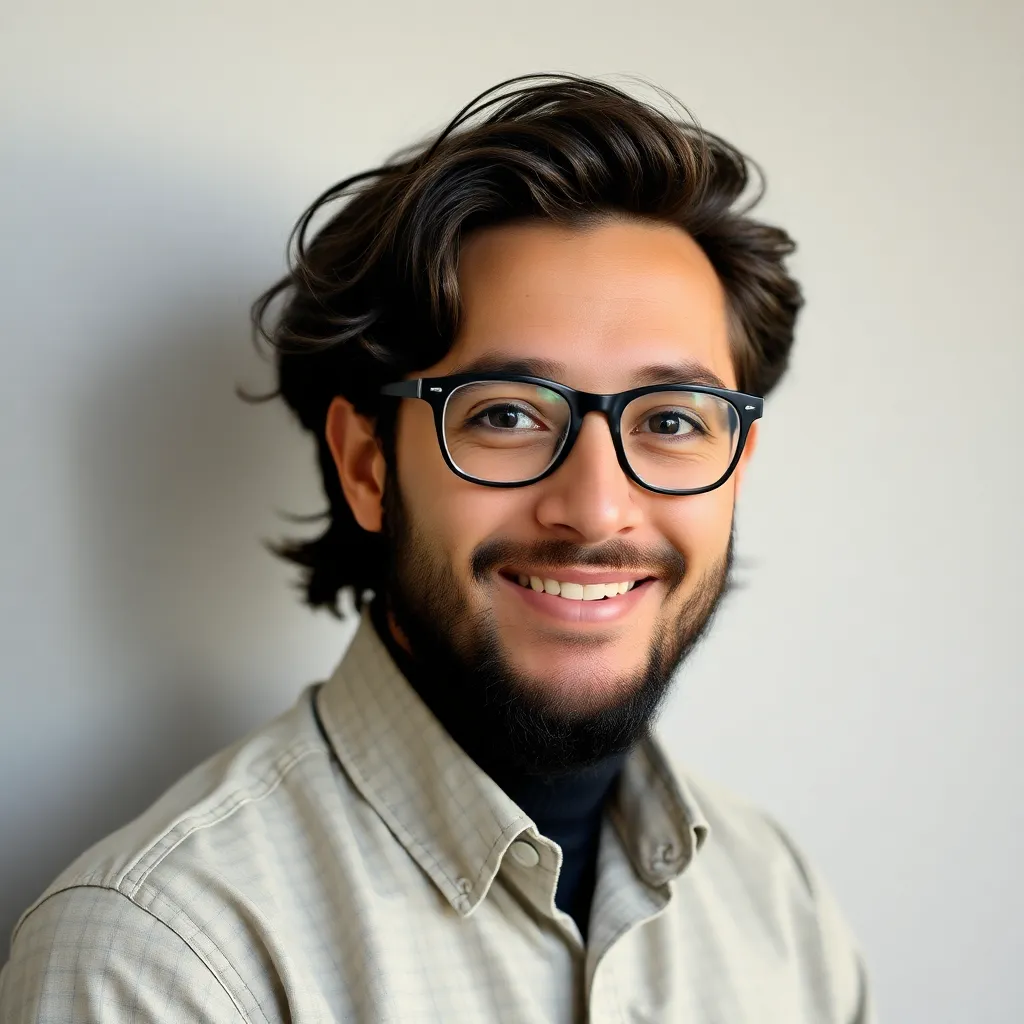
Muz Play
May 12, 2025 · 6 min read
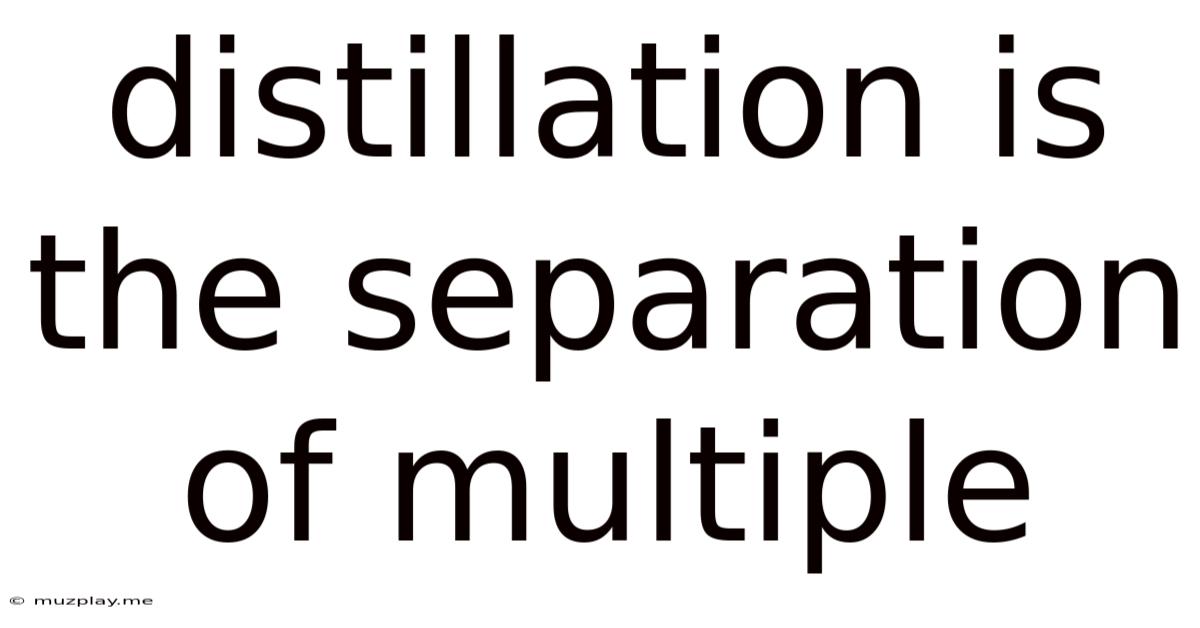
Table of Contents
Distillation: The Separation of Multiple Components in a Mixture
Distillation, a cornerstone technique in chemistry and chemical engineering, is a powerful method for separating multiple components within a liquid mixture based on their differing boiling points. This process leverages the principle of vapor-liquid equilibrium, where the more volatile components (those with lower boiling points) vaporize more readily than less volatile ones. The resulting vapor is then condensed, collected, and purified, yielding a fraction enriched in the lower-boiling component. This seemingly simple process has far-reaching applications across numerous industries, from the production of alcoholic beverages to the refinement of petroleum products.
Understanding the Fundamentals of Distillation
At the heart of distillation lies the concept of vapor pressure. Each component in a liquid mixture exerts a partial pressure, contributing to the total vapor pressure above the liquid. The component with the highest vapor pressure at a given temperature will vaporize more readily. When the total vapor pressure equals the atmospheric pressure, the liquid boils.
Key Terms and Concepts:
- Boiling Point: The temperature at which the vapor pressure of a liquid equals the external pressure. Different substances have different boiling points.
- Volatility: A measure of how readily a substance vaporizes. Highly volatile substances have low boiling points.
- Vapor-Liquid Equilibrium (VLE): The state where the rate of evaporation equals the rate of condensation at a given temperature and pressure. This is crucial for understanding the separation process.
- Raoult's Law: This law describes the partial pressure of each component in an ideal mixture. It states that the partial pressure of a component is equal to the product of its mole fraction in the liquid and its vapor pressure in the pure state. While ideal behavior is rare, Raoult's Law provides a useful starting point for understanding distillation.
- Relative Volatility: This parameter quantifies the ease of separating two components in a mixture. It is the ratio of the vapor pressures of the two components. A higher relative volatility indicates easier separation.
Types of Distillation: Tailoring the Process to the Mixture
Distillation isn't a one-size-fits-all solution. The optimal method depends on the complexity of the mixture, the desired purity of the separated components, and the scale of the operation. Here are some prominent types:
1. Simple Distillation:
This is the most basic form of distillation, suitable for separating mixtures with components having significantly different boiling points (at least 70-80°C difference). The mixture is heated, and the vapor is directly condensed and collected. Simple distillation is relatively inexpensive and easy to set up, but it's inefficient for separating closely boiling components. It's often used for purifying a liquid containing non-volatile impurities.
2. Fractional Distillation:
Fractional distillation is a more sophisticated technique used when the boiling points of the components are closer together. It employs a fractionating column, which provides multiple vapor-liquid equilibrium stages. As the vapor rises through the column, it repeatedly condenses and re-vaporizes, leading to a gradual enrichment of the more volatile component in the vapor phase. The efficiency of the fractional distillation process hinges on the design and length of the fractionating column; more theoretical plates (stages of vapor-liquid equilibrium) generally lead to better separation. This method is widely used in petroleum refining to separate different hydrocarbon fractions.
3. Steam Distillation:
This method is particularly useful for separating thermally sensitive components or those that are immiscible with water. Steam is passed through the mixture, lowering the boiling point of the components. The mixture boils at a temperature below the boiling point of any individual component. The vapor, a mixture of steam and the volatile components, is then condensed. The components separate because of their immiscibility, enabling the isolation of desired substances. Steam distillation finds application in the extraction of essential oils from plants.
4. Vacuum Distillation:
For substances with high boiling points, vacuum distillation is used. Reducing the pressure above the liquid lowers its boiling point, preventing decomposition or degradation that could occur at higher temperatures. This technique is employed in the purification of heat-sensitive compounds or high-boiling liquids.
5. Azeotropic Distillation:
Azeotropes are mixtures of liquids that boil at a constant composition. They cannot be separated by conventional distillation methods. Azeotropic distillation utilizes various techniques to overcome this challenge, such as adding an entrainer (a third component that modifies the vapor-liquid equilibrium) or employing pressure swing distillation. This method is vital in separating azeotropic mixtures frequently encountered in industrial processes.
Applications of Distillation: A Wide Spectrum of Industries
Distillation's versatility makes it indispensable across diverse sectors:
1. Petroleum Refining:
The refining of crude oil relies heavily on distillation to separate it into various fractions like gasoline, kerosene, diesel, and lubricating oils. Fractional distillation is crucial here, considering the complexity of crude oil's composition.
2. Alcoholic Beverage Production:
Distillation is fundamental to producing spirits like whiskey, vodka, and gin. The process purifies the fermented mash, concentrating the ethanol content. Different distillation techniques and column designs contribute to the unique characteristics of different alcoholic beverages.
3. Pharmaceutical Industry:
Distillation plays a vital role in purifying solvents, separating reaction products, and isolating active pharmaceutical ingredients. The precise control and high purity achieved through distillation are essential for pharmaceutical quality standards.
4. Chemical Industry:
Numerous chemical processes employ distillation to separate reactants, products, and byproducts. The purification of chemicals is essential for maintaining product quality and preventing unwanted side reactions.
5. Water Purification:
While not as commonly associated with distillation, it's increasingly used for desalination and water purification. The process removes impurities, including salts and other dissolved solids, producing potable water.
Optimization and Efficiency in Distillation
Optimizing the distillation process is crucial for maximizing efficiency and minimizing energy consumption. Several factors influence the effectiveness of separation:
- Column Design: The design of the distillation column, including the number of theoretical plates and the type of packing material, significantly affects separation efficiency.
- Reflux Ratio: The reflux ratio, which is the ratio of liquid returned to the column to the liquid withdrawn as distillate, impacts the purity of the separated components. Higher reflux ratios generally lead to better separations but require more energy.
- Operating Pressure: Adjusting the operating pressure can significantly affect the boiling points of the components, influencing the ease of separation.
- Feed Composition: The composition of the feed mixture significantly impacts the efficiency of separation.
- Heat Integration: Employing heat integration techniques can minimize energy consumption by recovering heat from the process streams.
Advanced Distillation Techniques: Pushing the Boundaries
Recent advancements in distillation have pushed the boundaries of efficiency and applicability:
- Membrane Distillation: This technique uses a hydrophobic membrane to separate volatile components from a liquid mixture. It offers advantages in terms of energy efficiency and potential for handling complex mixtures.
- Reactive Distillation: Combining chemical reactions with distillation allows for simultaneous reaction and separation, improving yields and reducing energy consumption.
- Extractive Distillation: Adding a suitable solvent to the mixture modifies the relative volatilities of the components, making separation easier. This is particularly useful for separating azeotropic mixtures.
- Pressure Swing Distillation: This technique involves alternating between high and low pressure during the distillation process to enhance separation.
Conclusion: The Enduring Importance of Distillation
Distillation, despite its seemingly simple principles, remains a powerful and versatile separation technique with widespread industrial applications. Continuous advancements in technology, coupled with a deeper understanding of the underlying thermodynamics and mass transfer processes, are continually improving its efficiency and expanding its capabilities. From the production of everyday consumer goods to the refinement of crucial industrial chemicals, distillation plays a crucial role in our modern world. The optimization and ongoing development of novel distillation techniques ensure its continued importance in meeting the ever-evolving demands of various industries.
Latest Posts
Latest Posts
-
What Is The Iupac Name For The Following Compound
May 12, 2025
-
Molecular Weight Of One Amino Acid
May 12, 2025
-
Is Sugar A Mixture Or A Pure Substance
May 12, 2025
-
How To Read The Solubility Table
May 12, 2025
-
Is Evaporation An Exothermic Or Endothermic Process
May 12, 2025
Related Post
Thank you for visiting our website which covers about Distillation Is The Separation Of Multiple . We hope the information provided has been useful to you. Feel free to contact us if you have any questions or need further assistance. See you next time and don't miss to bookmark.