Fracture Stress On Stress Strain Curve
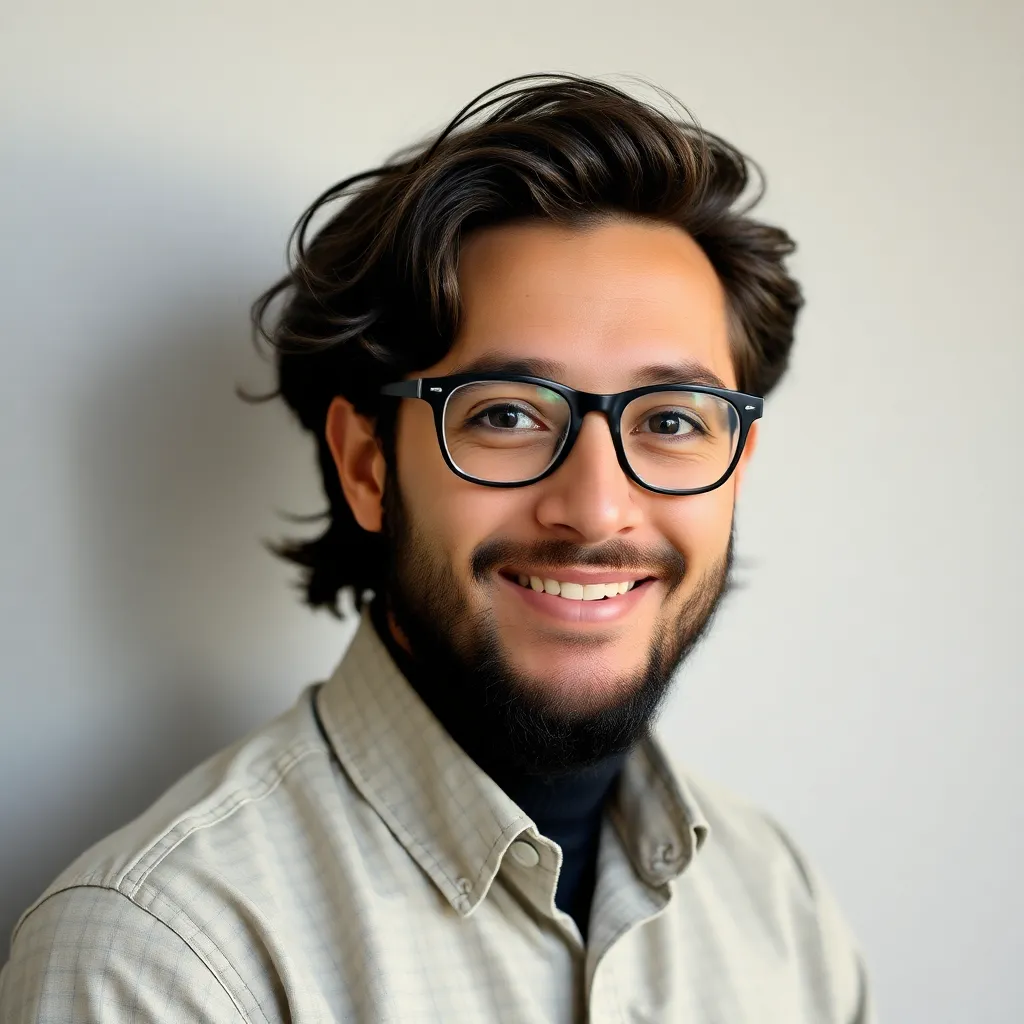
Muz Play
Apr 22, 2025 · 6 min read

Table of Contents
Fracture Stress on the Stress-Strain Curve: A Comprehensive Guide
Understanding the fracture stress, as depicted on the stress-strain curve, is crucial in materials science and engineering. This point marks the ultimate limit of a material's ability to withstand stress before catastrophic failure occurs. This comprehensive guide will delve into the intricacies of fracture stress, exploring its significance, influencing factors, and practical applications.
What is Fracture Stress?
Fracture stress, also known as ultimate tensile strength (UTS) or tensile strength, represents the maximum stress a material can endure before it fractures or breaks. This value is determined experimentally through tensile testing, where a standardized specimen is subjected to a uniaxial tensile load until failure. The stress-strain curve generated from this test vividly illustrates the material's behavior, with the fracture stress marking the peak point on the curve. It's important to differentiate fracture stress from the yield strength, which indicates the onset of plastic deformation. While yield strength signifies the material's beginning of permanent deformation, fracture stress represents its complete structural failure.
Identifying Fracture Stress on the Stress-Strain Curve
The stress-strain curve, a graphical representation of a material's response to an applied load, is indispensable in identifying fracture stress. The curve typically shows an initial elastic region, followed by a plastic region, and culminates at the fracture point. The highest point on the curve represents the ultimate tensile strength or fracture stress. Beyond this point, the material loses its ability to resist further stress, leading to catastrophic failure. The curve's shape varies depending on the material's properties; ductile materials exhibit a significant plastic region before fracture, while brittle materials show little to no plastic deformation prior to failure.
Factors Influencing Fracture Stress
Numerous factors can significantly influence a material's fracture stress. These factors can be broadly categorized into intrinsic and extrinsic factors.
Intrinsic Factors (Material Properties)
-
Material Composition: The chemical composition of a material significantly impacts its strength. Alloying elements, impurities, and grain size all play crucial roles. For instance, adding carbon to iron increases its strength and hardness.
-
Microstructure: The arrangement of grains and phases within a material significantly affects its mechanical properties. Fine-grained materials generally exhibit higher strength compared to coarse-grained materials due to increased grain boundary area, hindering dislocation movement. The presence of defects such as voids, inclusions, and cracks also weakens the material.
-
Crystal Structure: The crystal structure of a material influences its mechanical behavior. Materials with different crystal structures exhibit varying strengths and fracture toughness. For instance, face-centered cubic (FCC) metals are typically more ductile than body-centered cubic (BCC) metals.
-
Temperature: Temperature significantly influences a material's strength. Generally, the strength of most materials decreases with increasing temperature, as elevated temperatures promote atomic mobility and dislocation movement. However, some materials, like certain ceramics, show increased strength at higher temperatures.
-
Strain Rate: The rate at which the load is applied affects the material's response. High strain rates tend to increase the apparent fracture stress, as the material doesn't have sufficient time to deform plastically.
Extrinsic Factors (Environmental Conditions)
-
Temperature: As mentioned previously, temperature is a critical factor impacting fracture stress. Changes in ambient temperature during testing can lead to variations in the observed fracture strength.
-
Loading Conditions: The type of loading (tensile, compressive, shear, etc.) affects the material's response. Tensile loading typically leads to lower fracture stress compared to compressive loading in brittle materials. The manner in which the load is applied – whether static or dynamic – also plays a crucial role.
-
Surface Finish: The surface roughness of a material can significantly influence its fracture strength. Surface imperfections, such as scratches or notches, act as stress concentrators, significantly reducing the material's overall strength.
-
Environmental Effects: The surrounding environment can impact fracture stress. Corrosion, for example, can weaken the material's structure, leading to premature fracture. Exposure to specific chemicals or radiation can also degrade material properties.
Determining Fracture Stress: Experimental Techniques
Tensile testing is the primary method for determining fracture stress. This involves subjecting a standardized specimen to a uniaxial tensile load until failure, while continuously measuring the applied force and the resulting elongation. The stress-strain curve generated from this test allows for the precise determination of the fracture stress (UTS). Other techniques used to assess the material's fracture behaviour include:
-
Charpy Impact Test: Measures a material's ability to absorb energy upon impact, providing insights into its fracture toughness, especially at low temperatures.
-
Fracture Toughness Testing: Determines the material's resistance to crack propagation, providing additional information about its fracture behavior beyond the simple fracture stress.
-
Fatigue Testing: This assesses a material's resistance to failure under cyclic loading, which is crucial for applications subjected to repeated stresses.
Applications and Significance of Fracture Stress
Understanding fracture stress is paramount across various engineering disciplines. It is crucial for:
-
Material Selection: Engineers use fracture stress data to select appropriate materials for specific applications. Components operating under high-stress conditions require materials with high fracture stress.
-
Design and Manufacturing: Knowing the fracture stress allows engineers to design and manufacture components that can withstand anticipated loads and avoid failure. Safety factors are often incorporated to ensure that the applied stress remains well below the fracture stress.
-
Quality Control: Regular testing of materials using tensile tests ensures that materials meet specified strength requirements. This ensures consistent quality and reliability of manufactured products.
-
Predictive Modelling: Data regarding fracture stress are crucial in developing and refining predictive models for material failure. This can help in designing more robust and reliable structures and components.
-
Failure Analysis: In the case of component failure, determining the fracture stress aids in understanding the cause of failure and identifying potential improvements in material selection or design.
Beyond Fracture Stress: Considering Ductility and Toughness
While fracture stress provides crucial information about a material's strength, it's essential to consider other factors like ductility and toughness for a complete understanding of its mechanical behavior.
Ductility
Ductility refers to a material's ability to deform plastically before fracture. High ductility implies that the material undergoes significant plastic deformation prior to fracture, providing warning signs before failure. Brittle materials, on the other hand, exhibit little or no plastic deformation before fracture, resulting in sudden and catastrophic failure.
Toughness
Toughness represents the material's ability to absorb energy before fracture. High toughness indicates that the material can withstand significant amounts of energy before failure, offering increased safety and reliability. Toughness is influenced by both strength and ductility.
Conclusion
Fracture stress, as indicated on the stress-strain curve, is a critical material property that defines the maximum stress a material can withstand before failure. Understanding this property, coupled with knowledge of ductility and toughness, is indispensable for engineers and material scientists. Numerous factors, both intrinsic and extrinsic, influence fracture stress. Through careful material selection, design considerations, and quality control, engineers can leverage this knowledge to create safe, reliable, and efficient structures and components. The continued research and advancement in understanding fracture stress will continue to lead to innovation across multiple sectors, from aerospace to biomedical engineering.
Latest Posts
Latest Posts
-
What Refers To The Division Of The Nucleus
Apr 22, 2025
-
Electrons Travel In Paths Called Energy Levels
Apr 22, 2025
-
Does Sodium Lose Or Gain Electrons
Apr 22, 2025
-
What Is The Difference Between Base Units And Derived Units
Apr 22, 2025
-
Osmotic Pressure Is Measured In Units Of
Apr 22, 2025
Related Post
Thank you for visiting our website which covers about Fracture Stress On Stress Strain Curve . We hope the information provided has been useful to you. Feel free to contact us if you have any questions or need further assistance. See you next time and don't miss to bookmark.