How Does A Fractional Column Work
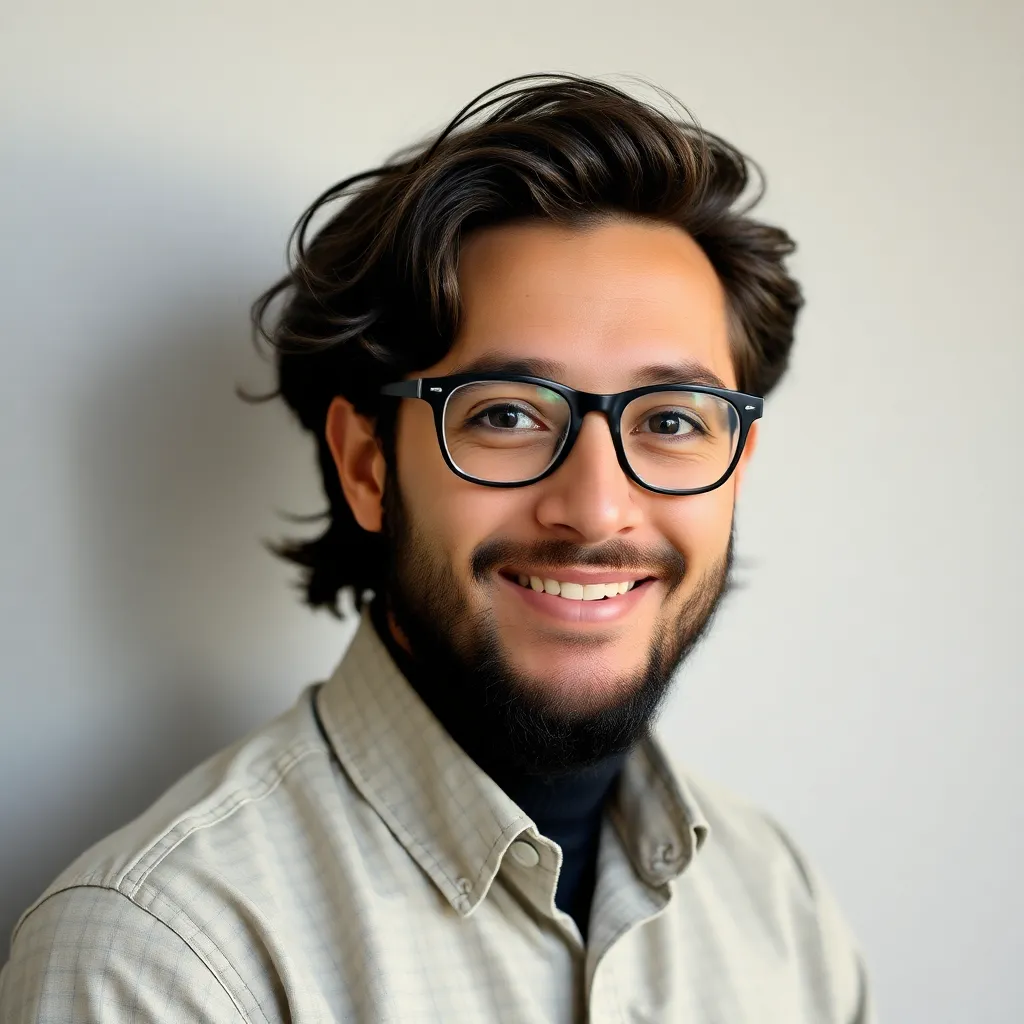
Muz Play
Apr 24, 2025 · 5 min read

Table of Contents
How Does a Fractional Column Work? A Deep Dive into Distillation's Workhorse
Distillation, a cornerstone of chemical engineering and countless industrial processes, relies heavily on fractional columns to achieve efficient separations. Understanding how these columns work is crucial for anyone involved in chemical processing, refining, or related fields. This comprehensive guide will delve into the intricacies of fractional columns, explaining the principles behind their operation and the factors influencing their effectiveness.
The Fundamentals of Fractional Distillation
Fractional distillation is a process used to separate a mixture of liquids with different boiling points. It's an extension of simple distillation, offering significantly improved separation efficiency, especially for mixtures with closely boiling components. The key difference lies in the incorporation of a fractionating column, a device designed to provide multiple stages of vaporization and condensation within a single apparatus.
Simple Distillation vs. Fractional Distillation
Before delving into the complexities of fractional columns, let's briefly compare simple and fractional distillation:
-
Simple Distillation: Suitable for separating liquids with significantly different boiling points. It involves a single vaporization and condensation cycle, resulting in relatively impure distillate.
-
Fractional Distillation: Ideal for separating liquids with similar boiling points. It employs a fractionating column to create multiple vapor-liquid equilibrium stages, leading to a much purer distillate. This enhanced separation capability is the primary reason for its widespread use in various industries.
The Anatomy of a Fractional Column
A fractional column typically consists of several key components:
- Still Pot: The bottom of the column where the liquid mixture is heated.
- Fractionating Column: The central component where the separation occurs. This contains packing materials or trays to increase surface area and efficiency.
- Condenser: Cools the vapor rising from the column, converting it back into liquid.
- Receiver: Collects the purified liquid (distillate).
- Thermometer: Monitors the temperature of the vapor, providing crucial information about the composition of the distillate.
The Role of Packing Materials and Trays
The efficiency of a fractional column heavily depends on the type and arrangement of its internal components, which increase the surface area available for vapor-liquid contact. These components fall into two primary categories:
-
Packing Materials: These are inert materials with high surface area-to-volume ratios, such as glass beads, Raschig rings, or metal helices. They provide numerous sites for vapor condensation and subsequent re-vaporization, mimicking multiple simple distillation steps. The increased surface area allows for better vapor-liquid equilibrium to be achieved at each point along the column.
-
Trays (or Plates): These are horizontal plates with various designs (e.g., bubble-cap trays, sieve trays) that provide discrete stages for vapor-liquid contact. Vapor bubbles up through the liquid on each tray, allowing for efficient mass transfer. The design of the trays influences the efficiency of vapor-liquid interaction.
The Mechanism of Separation: Vapor-Liquid Equilibrium
The heart of fractional distillation lies in the principle of vapor-liquid equilibrium (VLE). When a liquid mixture is heated, the more volatile component (lower boiling point) vaporizes more readily. This vapor rises up the column, while the less volatile component remains predominantly in the liquid phase.
As the vapor rises, it encounters cooler surfaces (packing materials or trays). This causes a portion of the vapor to condense, enriching the liquid phase with the less volatile component. Simultaneously, the heat from the rising vapor partially vaporizes the condensed liquid, enriching the vapor phase with the more volatile component.
This continuous cycle of vaporization and condensation, occurring repeatedly along the column, progressively separates the components. Each cycle effectively represents a single theoretical plate, or equilibrium stage. The more theoretical plates a column has, the better the separation.
Factors Affecting Fractional Column Efficiency
Several factors influence the efficiency of a fractional column:
- Column Length: A longer column provides more theoretical plates, leading to better separation.
- Column Diameter: A wider column can handle larger volumes but might reduce efficiency per unit length.
- Packing Material/Tray Design: The surface area and efficiency of the packing or trays significantly impact separation.
- Heating Rate: A controlled heating rate is crucial to maintain equilibrium and avoid flooding (excessive liquid flow) or weeping (liquid leaking past the packing).
- Reflux Ratio: The reflux ratio is the ratio of liquid returned to the column to the liquid removed as distillate. A higher reflux ratio generally improves separation but requires more time and energy.
Advanced Concepts and Techniques
The practical application of fractional distillation often involves more sophisticated techniques and considerations:
-
Azeotropes: Some liquid mixtures form azeotropes, where the vapor composition is identical to the liquid composition at a specific boiling point. These mixtures cannot be separated by conventional fractional distillation and require specialized techniques like azeotropic distillation or extractive distillation.
-
Vacuum Distillation: For high-boiling point liquids, vacuum distillation reduces the boiling point, minimizing thermal degradation and improving separation efficiency.
-
Steam Distillation: This technique is employed for separating heat-sensitive compounds. Steam is introduced to the mixture, lowering the boiling point of the components and reducing the risk of decomposition.
-
Optimization Techniques: Sophisticated modeling and simulation techniques are used to optimize column design and operating parameters to achieve desired separation with maximum efficiency and minimum energy consumption.
Applications of Fractional Distillation
Fractional distillation is ubiquitous in various industrial processes and applications, including:
- Petroleum Refining: Separating crude oil into its various components (gasoline, kerosene, diesel, etc.).
- Chemical Manufacturing: Purifying chemical compounds and separating reaction products.
- Liquefied Air Separation: Separating air into its constituent gases (nitrogen, oxygen, argon).
- Pharmaceutical Industry: Purifying pharmaceutical compounds and solvents.
- Food and Beverage Industry: Separating and purifying alcohol in the production of spirits.
Conclusion: Mastering the Art of Separation
Fractional distillation, facilitated by the ingenious design of fractional columns, remains a critical separation technique across a vast range of industries. Understanding the underlying principles of vapor-liquid equilibrium, the role of column design, and the impact of various operating parameters is essential for efficient and effective separation processes. Continued advancements in column design, packing materials, and control strategies promise further improvements in the precision and efficiency of fractional distillation, solidifying its position as a cornerstone of modern chemical engineering. The ability to separate complex mixtures with high purity remains vital for countless applications, making the study of fractional columns a worthwhile endeavor for anyone pursuing a career in related fields.
Latest Posts
Latest Posts
-
What Is A Unique Solution In Linear Algebra
Apr 24, 2025
-
Name The 2nd Trophic Level Both Names
Apr 24, 2025
-
The Adjusting Entry For Accrued Revenues
Apr 24, 2025
-
Relationship Between Work And Power Physics
Apr 24, 2025
-
How Is Self Pollination Similar To Cross Pollination
Apr 24, 2025
Related Post
Thank you for visiting our website which covers about How Does A Fractional Column Work . We hope the information provided has been useful to you. Feel free to contact us if you have any questions or need further assistance. See you next time and don't miss to bookmark.