The Conversion Of Nitrogen Gas To Ammonia Is Called
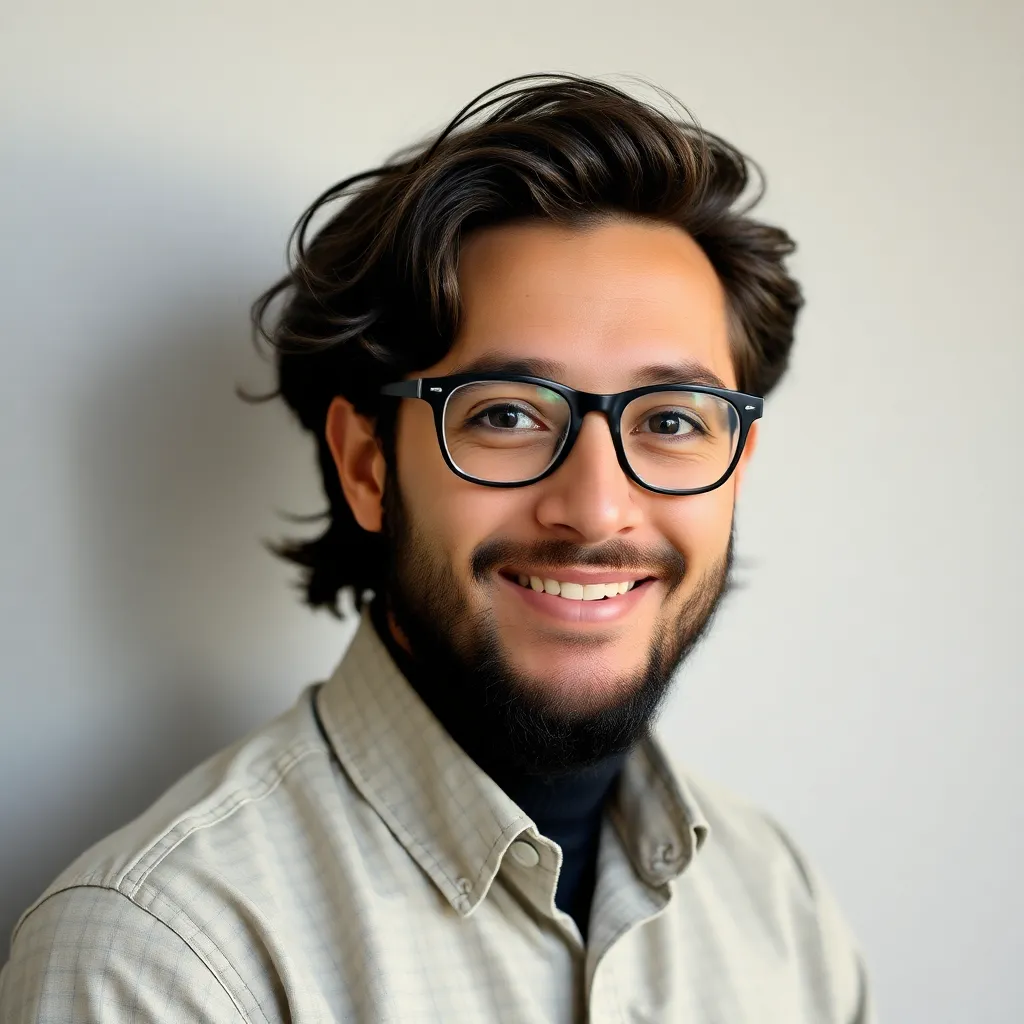
Muz Play
Apr 19, 2025 · 6 min read

Table of Contents
The Conversion of Nitrogen Gas to Ammonia: A Deep Dive into the Haber-Bosch Process
The conversion of nitrogen gas (N₂) to ammonia (NH₃) is a process of monumental importance, fundamentally shaping the world's food supply and impacting various industrial sectors. This crucial reaction, known as nitrogen fixation, is not naturally abundant enough to meet the global demand for nitrogen-based fertilizers. The primary method for achieving this conversion on an industrial scale is the Haber-Bosch process, a cornerstone of modern chemistry and agriculture. This article delves into the intricacies of this process, exploring its history, chemistry, thermodynamics, industrial implementation, and its environmental impact.
Understanding the Haber-Bosch Process: A Chemical Marvel
The Haber-Bosch process is essentially the catalytic reaction between nitrogen gas (N₂) and hydrogen gas (H₂) to produce ammonia (NH₃). The balanced chemical equation is:
N₂(g) + 3H₂(g) ⇌ 2NH₃(g)
This seemingly simple equation belies the complexity of the process. The reaction is:
- Exothermic: It releases heat, meaning the products have lower energy than the reactants. This exothermicity, however, is not sufficient to drive the reaction towards completion.
- Equilibrium-Limited: The reaction reaches an equilibrium, meaning that at any given temperature and pressure, a certain proportion of reactants and products will coexist. To favor ammonia production, careful manipulation of reaction conditions is necessary.
- Requires a Catalyst: The activation energy for the reaction is very high, requiring a catalyst to speed up the process. Without a catalyst, the reaction would be impractically slow. The most commonly used catalyst is finely divided iron, often promoted with other elements like potassium and aluminum oxides.
The Role of Thermodynamics and Kinetics
The Haber-Bosch process highlights the interplay between thermodynamics and kinetics. Thermodynamics dictates the equilibrium position and spontaneity of the reaction. For the ammonia synthesis:
- High pressure favors ammonia formation: According to Le Chatelier's principle, increasing the pressure shifts the equilibrium towards the side with fewer moles of gas (in this case, the product side). Industrially, pressures ranging from 150 to 350 atmospheres are typically employed.
- Low temperature favors ammonia formation: Because the reaction is exothermic, lowering the temperature shifts the equilibrium towards the product side. However, lower temperatures drastically decrease the reaction rate, making the process impractically slow.
Kinetics, on the other hand, deals with the rate of the reaction. To achieve a commercially viable rate:
- High temperature is essential: Despite favoring the reactants at equilibrium, a higher temperature is necessary to increase the reaction rate, even if it means compromising equilibrium yields. Temperatures around 400-500°C are typically used.
- Catalyst is crucial: The iron catalyst lowers the activation energy, significantly accelerating the reaction rate without altering the equilibrium position.
The History of the Haber-Bosch Process: A Legacy of Innovation
The development of the Haber-Bosch process was a monumental achievement in chemical engineering, significantly impacting humanity. Fritz Haber, a German chemist, played a pivotal role in the early 20th century, discovering the essential catalysts and laying the foundation for the process. Carl Bosch, a German chemical engineer, then successfully scaled up the process to industrial levels, overcoming significant engineering challenges related to high-pressure operation.
The timing of its development was crucial. The burgeoning global population at the beginning of the 20th century placed enormous strain on food production. The Haber-Bosch process enabled the large-scale production of nitrogen-based fertilizers, dramatically boosting crop yields and ensuring food security for a growing population. This had a profound impact on global demographics, enabling a population explosion that continues to this day.
Industrial Implementation: A Complex Engineering Feat
The industrial implementation of the Haber-Bosch process is a complex engineering undertaking, requiring sophisticated technology and precise control:
- Hydrogen Production: Hydrogen gas, a crucial reactant, is typically produced from natural gas (methane) through steam reforming. This involves reacting methane with steam at high temperatures to produce hydrogen and carbon dioxide. Other methods, such as electrolysis of water, are also being explored to reduce reliance on fossil fuels.
- Nitrogen Purification: Nitrogen gas is obtained from the fractional distillation of liquid air. Purification is essential to remove impurities that could poison the catalyst.
- Compression and Purification: Both hydrogen and nitrogen gases are compressed to the required high pressure before being fed into the reactor. Purification systems are crucial throughout the process to remove any impurities that could damage the catalyst or contaminate the product.
- Reactor Design: The reactor is designed to withstand the high temperatures and pressures involved. The catalyst is carefully distributed to maximize its surface area and optimize reaction efficiency.
- Ammonia Separation and Purification: After the reaction, the ammonia gas is separated from the unreacted nitrogen and hydrogen using a process called fractional condensation. The unreacted gases are recycled back into the reactor to improve efficiency.
- Product Handling and Storage: The purified ammonia is then stored and transported for use in fertilizer production or other industrial applications.
Environmental Impact: A Double-Edged Sword
While the Haber-Bosch process has been instrumental in feeding billions of people, its environmental impact is a subject of ongoing debate:
- Greenhouse Gas Emissions: The production of hydrogen from natural gas releases significant amounts of carbon dioxide, a potent greenhouse gas, contributing to climate change.
- Energy Consumption: The process is energy-intensive, requiring substantial amounts of fossil fuels, further increasing carbon emissions.
- Ammonia Release: Ammonia is a potent greenhouse gas itself, and some ammonia can be released into the atmosphere during fertilizer application or production, contributing to environmental pollution and acid rain.
- Eutrophication: Excess nitrogen from fertilizers can run off into water bodies, causing eutrophication – an excessive growth of algae that depletes oxygen and harms aquatic life.
Research is underway to improve the environmental profile of the Haber-Bosch process:
- Renewable Energy Sources: Replacing fossil fuels with renewable energy sources (such as solar, wind, or geothermal energy) for hydrogen production would significantly reduce greenhouse gas emissions.
- Electrochemical Methods: Developing more efficient electrochemical methods for ammonia synthesis, possibly using renewable electricity, is another area of active research.
- Catalyst Improvements: Developing more efficient and selective catalysts could reduce energy consumption and improve yields.
- Precision Agriculture: Implementing precision agriculture techniques could reduce fertilizer overuse and minimize environmental pollution from excess nitrogen.
The Future of Ammonia Synthesis: Sustainability and Innovation
The Haber-Bosch process, though crucial for global food security, faces significant challenges regarding its environmental footprint. Research efforts are focusing on developing more sustainable alternatives:
- Electrocatalytic Nitrogen Reduction: Using renewable electricity to directly reduce nitrogen gas to ammonia in an electrochemical cell offers a potential pathway to a more sustainable process.
- Photocatalytic Nitrogen Fixation: Utilizing sunlight to drive the conversion of nitrogen gas to ammonia using photocatalysts is another promising approach.
- Bio-inspired Nitrogen Fixation: Mimicking the nitrogen fixation mechanisms of certain bacteria could provide a more environmentally friendly and energy-efficient route.
These alternative methods are still in their early stages of development, but they hold immense potential for creating a more sustainable ammonia production industry.
Conclusion: A Balancing Act Between Necessity and Sustainability
The conversion of nitrogen gas to ammonia, primarily achieved through the Haber-Bosch process, is a cornerstone of modern civilization, enabling unprecedented increases in agricultural productivity and supporting a vastly larger global population than would otherwise be possible. However, its environmental impacts cannot be ignored. The future of ammonia synthesis lies in developing sustainable and environmentally friendly alternatives that can meet the growing global demand for nitrogen while minimizing its ecological footprint. The challenge lies in balancing the critical need for food production with the urgent need for environmental stewardship. Continuous innovation and research are essential to achieve this balance and ensure a secure and sustainable future.
Latest Posts
Latest Posts
-
All Real Numbers Less Than 3
Apr 19, 2025
-
On First Exposure To Antigen T Helper Cells
Apr 19, 2025
-
Cellulose Is A Made Of Many
Apr 19, 2025
-
Which Is The Property Of Nonmetals To Evaporate Easily
Apr 19, 2025
-
How To Find Direction Of Magnetic Force
Apr 19, 2025
Related Post
Thank you for visiting our website which covers about The Conversion Of Nitrogen Gas To Ammonia Is Called . We hope the information provided has been useful to you. Feel free to contact us if you have any questions or need further assistance. See you next time and don't miss to bookmark.