The Three Sources Of Inefficiency Are
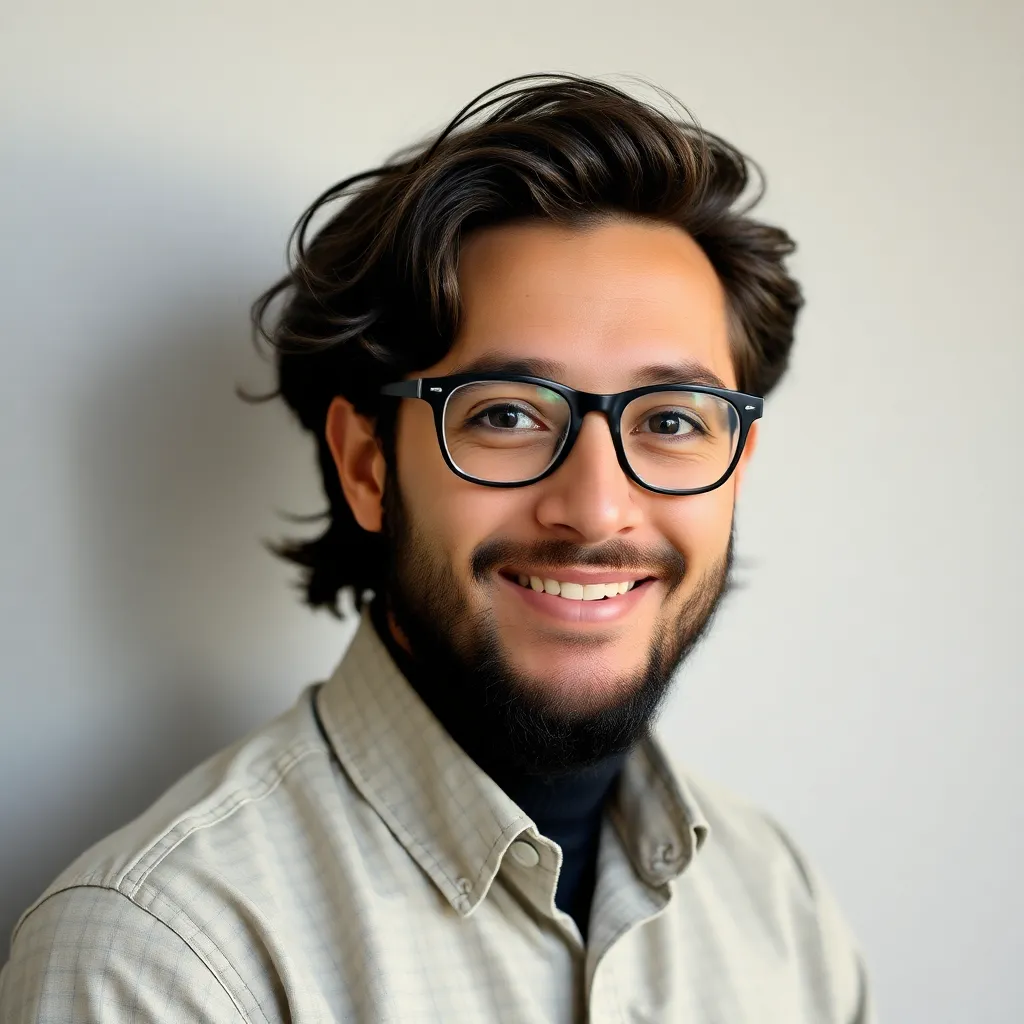
Muz Play
May 09, 2025 · 6 min read
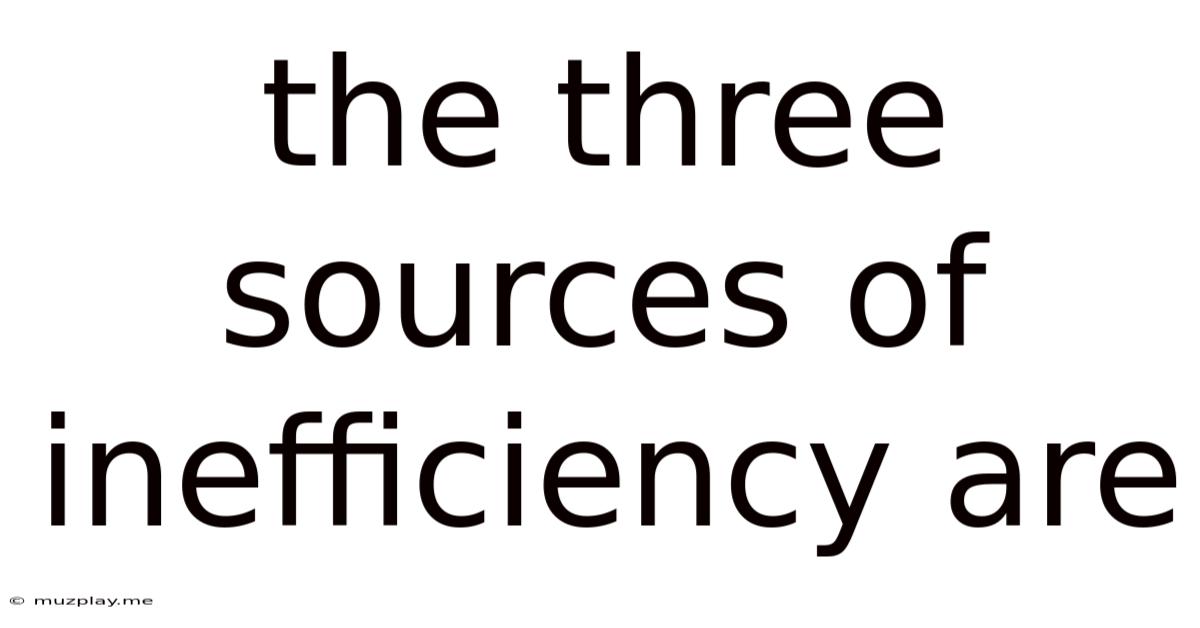
Table of Contents
The Three Sources of Inefficiency: Identifying and Eliminating Waste in Your Business
In today's competitive business landscape, efficiency is paramount. Businesses that can streamline their operations, eliminate waste, and maximize productivity are more likely to thrive. Understanding the root causes of inefficiency is crucial for identifying areas for improvement and driving significant gains in profitability and overall performance. This article delves into the three primary sources of inefficiency: process inefficiencies, resource inefficiencies, and skill inefficiencies. We'll explore each in detail, providing practical examples and strategies for overcoming these common hurdles.
1. Process Inefficiencies: Streamlining Your Workflow
Process inefficiencies stem from poorly designed, outdated, or unnecessarily complex workflows. These inefficiencies can manifest in many ways, leading to wasted time, resources, and ultimately, lost profits. Identifying and addressing process inefficiencies is a critical step towards optimizing your operations.
Identifying Process Bottlenecks: A Systematic Approach
The first step in tackling process inefficiencies is identifying the bottlenecks. This often involves:
- Mapping Your Processes: Create a visual representation of your workflows, charting each step, decision point, and handoff. Tools like flowcharts or swim lane diagrams can be invaluable here. This provides a clear picture of how work flows through your organization.
- Data Analysis: Analyze data related to process completion times, error rates, and resource consumption. Identify areas where significant delays occur or where resources are disproportionately used. Key Performance Indicators (KPIs) are crucial in this stage.
- Employee Feedback: Engage your employees directly. They are often the ones on the front lines and have valuable insights into the challenges and inefficiencies within existing processes. Conduct surveys, interviews, or focus groups to gather their perspectives.
Common Types of Process Inefficiencies:
- Redundancy: Performing the same task multiple times, often due to lack of communication or integration between departments.
- Unnecessary Steps: Processes that include steps that don't add value to the final product or service.
- Lack of Automation: Manually performing tasks that could be automated using software or technology. This often leads to increased error rates and slower processing times.
- Poor Communication: Inefficient communication channels, leading to delays, misunderstandings, and rework.
- Inadequate Training: Employees lacking the necessary skills or training to perform their tasks efficiently.
Strategies for Eliminating Process Inefficiencies:
- Process Re-engineering: Completely redesigning processes to eliminate unnecessary steps and improve efficiency. This often involves a radical shift from the current way of doing things.
- Automation: Implementing software and technology to automate repetitive tasks, reducing manual effort and increasing accuracy. Consider Robotic Process Automation (RPA) for high-volume, rule-based tasks.
- Lean Methodology: Employing lean principles to identify and eliminate waste in all aspects of the process. This focuses on continuous improvement and maximizing value for the customer.
- Improved Communication: Establishing clear communication channels and protocols to ensure seamless information flow between departments and teams.
- Standardization: Establishing standardized procedures and workflows to ensure consistency and reduce variation.
2. Resource Inefficiencies: Optimizing Your Assets
Resource inefficiencies arise from the misuse, underutilization, or mismanagement of resources – including personnel, equipment, materials, and capital. This often leads to increased costs, reduced productivity, and missed opportunities.
Identifying Resource Waste:
- Inventory Management: Holding excessive inventory ties up capital and increases storage costs. Analyze inventory turnover rates to identify slow-moving items.
- Equipment Utilization: Are your machines and equipment being used to their full capacity? Track utilization rates to identify idle time and potential optimization opportunities.
- Personnel Allocation: Are employees assigned to tasks that best utilize their skills and experience? Analyze employee workload and identify areas where resources are over- or under-allocated.
- Energy Consumption: Analyze energy usage patterns to identify opportunities for conservation and cost savings.
- Material Waste: Track material consumption and identify areas where waste can be reduced through improved processes or more efficient materials.
Common Types of Resource Inefficiencies:
- Overstocking: Holding more inventory than necessary.
- Idle Equipment: Equipment sitting idle due to lack of work or maintenance issues.
- Underutilized Personnel: Employees not fully utilizing their skills or time.
- Wasteful Energy Consumption: Excessive energy usage due to inefficient equipment or practices.
- Material Spoilage: Materials deteriorating or becoming unusable due to poor storage or handling.
Strategies for Eliminating Resource Inefficiencies:
- Just-in-Time Inventory: Implementing a just-in-time inventory system to minimize storage costs and reduce waste.
- Preventive Maintenance: Implementing a preventive maintenance program to minimize equipment downtime and extend the lifespan of assets.
- Employee Skill Development: Providing training and development opportunities to enhance employee skills and productivity.
- Energy-Efficient Technologies: Investing in energy-efficient equipment and technologies to reduce energy consumption.
- Waste Reduction Programs: Implementing programs to reduce material waste through improved processes and efficient material handling.
- Resource Allocation Optimization: Using software and data analysis to optimize the allocation of resources based on demand and capacity.
3. Skill Inefficiencies: Empowering Your Workforce
Skill inefficiencies occur when employees lack the necessary skills, knowledge, or training to perform their tasks effectively. This can lead to errors, delays, rework, and decreased overall productivity. Addressing skill gaps is crucial for improving efficiency and achieving organizational goals.
Identifying Skill Gaps:
- Performance Reviews: Regularly review employee performance to identify areas where skills or training are lacking.
- Employee Feedback: Gather feedback from employees to identify challenges they face due to skill gaps.
- Job Analysis: Conduct job analyses to identify the required skills for each position and compare them with the actual skills possessed by employees.
- Error Analysis: Analyze errors to identify root causes and determine whether skill gaps are contributing factors.
- Customer Feedback: Analyze customer feedback to identify areas where service delivery could be improved through improved employee skills.
Common Types of Skill Inefficiencies:
- Lack of Technical Skills: Employees lacking the technical skills necessary to operate equipment or use software.
- Inadequate Soft Skills: Employees lacking essential soft skills such as communication, teamwork, and problem-solving.
- Outdated Knowledge: Employees lacking up-to-date knowledge in their field.
- Lack of Training: Employees not receiving adequate training on new processes or technologies.
- Skill Mismatch: Employees assigned to tasks that do not match their skill sets.
Strategies for Eliminating Skill Inefficiencies:
- Training Programs: Implement comprehensive training programs to address skill gaps and enhance employee capabilities. This could include on-the-job training, workshops, online courses, or mentoring programs.
- Cross-Training: Train employees in multiple areas to improve flexibility and efficiency. This can help cover absences and improve overall team performance.
- Mentorship Programs: Pair experienced employees with newer employees to provide guidance and support.
- Job Rotation: Rotate employees through different roles to broaden their experience and skill sets.
- External Training: Utilize external training providers to offer specialized training not available internally.
- Skill Assessments: Regularly assess employee skills to identify areas for improvement and track progress.
Conclusion: A Holistic Approach to Efficiency
Eliminating inefficiencies requires a holistic approach that addresses all three sources – processes, resources, and skills. By systematically identifying bottlenecks, optimizing resource allocation, and investing in employee development, businesses can significantly improve efficiency, reduce costs, and enhance their overall competitiveness. Remember that continuous improvement is key. Regularly review and refine your processes, resources, and employee skill sets to ensure you are constantly optimizing your operations and staying ahead in the ever-evolving business world. Implementing these strategies requires commitment, careful planning, and a culture that values efficiency and continuous improvement. The rewards, however, are well worth the effort.
Latest Posts
Latest Posts
-
In The Short Run The Aggregate Supply Curve Slopes
May 09, 2025
-
When A Strong Acid Is Placed In Water It
May 09, 2025
-
A Conjugate Base Is The Species That
May 09, 2025
-
Which Level Of Organization Is The Highest
May 09, 2025
-
Why Is The Second Ionization Energy Higher
May 09, 2025
Related Post
Thank you for visiting our website which covers about The Three Sources Of Inefficiency Are . We hope the information provided has been useful to you. Feel free to contact us if you have any questions or need further assistance. See you next time and don't miss to bookmark.