What Are The Units For A Spring Constant
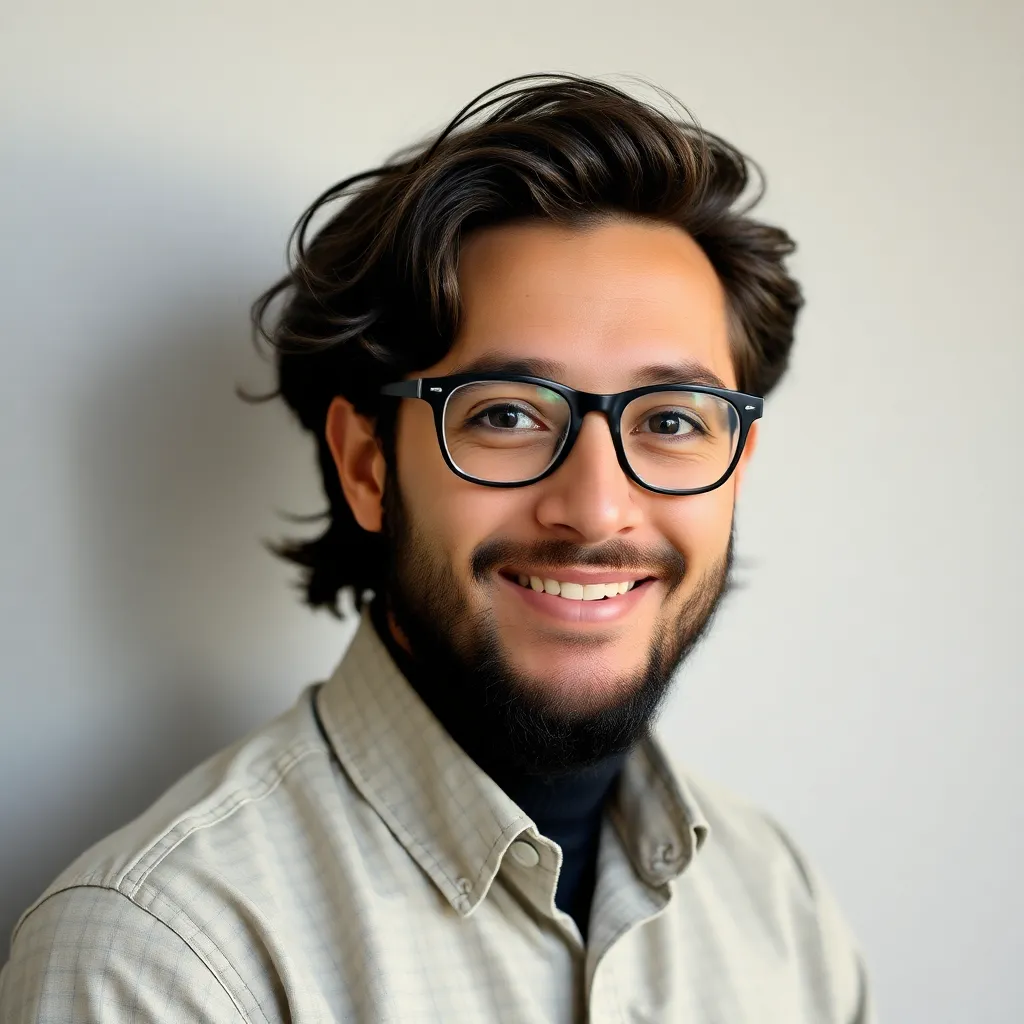
Muz Play
Apr 04, 2025 · 7 min read

Table of Contents
- What Are The Units For A Spring Constant
- Table of Contents
- What Are the Units for a Spring Constant? A Deep Dive into Hooke's Law and Spring Mechanics
- Understanding Hooke's Law: The Foundation of Spring Constant
- The Units of the Spring Constant: Unveiling the "N/m"
- Exploring Other Unit Systems
- Factors Affecting the Spring Constant: Beyond Material and Geometry
- 1. Material Properties: The Role of Young's Modulus
- 2. Geometry: Coils, Diameter, and Length
- 3. Temperature: The Impact of Thermal Effects
- Practical Applications and Examples: Spring Constant in Action
- 1. Automotive Engineering: Suspension Systems
- 2. Mechanical Engineering: Vibration Damping
- 3. Aerospace Engineering: Landing Gear
- 4. Medical Devices: Drug Delivery Systems
- 5. Consumer Electronics: Keyboards and Buttons
- Beyond Hooke's Law: Non-Linear Springs and Material Limitations
- Conclusion: Mastering the Spring Constant for Engineering Success
- Latest Posts
- Latest Posts
- Related Post
What Are the Units for a Spring Constant? A Deep Dive into Hooke's Law and Spring Mechanics
Understanding the units of a spring constant is crucial for anyone working with springs, from physicists and engineers to designers and hobbyists. This seemingly simple question opens the door to a fascinating exploration of Hooke's Law, the behavior of elastic materials, and the fundamental principles of mechanics. This comprehensive guide will delve deep into the topic, explaining not only the units themselves but also the underlying physics and practical applications.
Understanding Hooke's Law: The Foundation of Spring Constant
At the heart of spring constant calculations lies Hooke's Law, a fundamental principle in physics that describes the relationship between the force applied to an elastic object and the resulting deformation. The law states that the force (F) required to extend or compress a spring by some distance (x) is proportional to that distance. Mathematically, this is represented as:
F = kx
Where:
- F represents the force applied to the spring (measured in Newtons, N).
- x represents the displacement or deformation of the spring from its equilibrium position (measured in meters, m).
- k represents the spring constant (also known as the spring stiffness or rate). This is a measure of the spring's resistance to deformation.
This equation highlights the direct proportionality: a larger spring constant signifies a stiffer spring, requiring a greater force to achieve the same displacement as a spring with a smaller constant.
The Units of the Spring Constant: Unveiling the "N/m"
From Hooke's Law (F = kx), we can derive the units of the spring constant (k) by rearranging the equation to solve for k:
k = F/x
Since force (F) is measured in Newtons (N) and displacement (x) is measured in meters (m), the units of the spring constant are Newtons per meter (N/m). This means that a spring constant of 1 N/m indicates that a force of 1 Newton will cause a displacement of 1 meter. A higher value, like 100 N/m, implies a much stiffer spring that requires 100 Newtons of force for a 1-meter displacement.
Exploring Other Unit Systems
While N/m is the standard unit in the International System of Units (SI), other unit systems might be employed depending on the context. For instance:
- Dynes per centimeter (dyn/cm): Used in the centimeter-gram-second (CGS) system, this is a smaller unit of spring constant.
- Pounds per inch (lb/in): Commonly used in imperial units, this is frequently encountered in engineering applications.
- Kilonewtons per meter (kN/m): This is used for springs with significantly higher stiffness.
Conversion Between Units: It is crucial to ensure consistency in units when applying Hooke's Law. Converting between different units requires careful attention to conversion factors. For example, to convert from lb/in to N/m, you'd use conversion factors for both pounds to Newtons and inches to meters.
Factors Affecting the Spring Constant: Beyond Material and Geometry
The spring constant is not simply an inherent property of a spring; it's influenced by several factors:
1. Material Properties: The Role of Young's Modulus
The material from which the spring is made plays a significant role. Young's modulus (E), also known as the elastic modulus, is a measure of a material's stiffness or resistance to deformation under tensile or compressive stress. A material with a higher Young's modulus will generally result in a spring with a higher spring constant, all other factors being equal. Steels, for instance, possess significantly higher Young's moduli than rubbers, leading to much stiffer steel springs.
2. Geometry: Coils, Diameter, and Length
The physical dimensions of the spring drastically influence its stiffness. This includes:
- Number of coils: More coils generally lead to a lower spring constant (a less stiff spring).
- Coil diameter: A larger coil diameter typically results in a lower spring constant.
- Wire diameter: A thicker wire diameter usually leads to a higher spring constant (a stiffer spring).
- Spring length: The unstretched length of the spring also plays a role, although the relationship is not as straightforward as the others.
These geometric factors are often incorporated into more complex spring constant formulas that account for the specific design of the spring. These formulas are usually derived from the principles of elasticity and often involve advanced mathematical calculations.
3. Temperature: The Impact of Thermal Effects
Temperature changes can affect the material properties, hence the spring constant. Most materials exhibit a change in stiffness with temperature; some might become slightly stiffer with decreasing temperatures, while others might become less stiff. Precise calculations require consideration of the material's thermal expansion coefficient and its effect on Young's modulus.
Practical Applications and Examples: Spring Constant in Action
The concept of the spring constant has wide-ranging applications across numerous fields:
1. Automotive Engineering: Suspension Systems
Spring constants are fundamental in designing automotive suspension systems. Engineers carefully select springs with appropriate spring constants to provide optimal ride comfort and handling. Springs with higher spring constants offer better stability but a harsher ride, while those with lower constants provide a smoother ride but potentially less stability.
2. Mechanical Engineering: Vibration Damping
In mechanical systems where vibration control is paramount, understanding and choosing the correct spring constant is crucial. Springs are often used in conjunction with dampers to mitigate vibrations and oscillations, ensuring the smooth functioning of machinery. The optimal spring constant depends on the natural frequency of the system and the desired damping characteristics.
3. Aerospace Engineering: Landing Gear
Aircraft landing gear utilizes springs to absorb the impact of landing. Properly engineered spring constants are critical for ensuring both the structural integrity of the aircraft and the safety of passengers. The design must balance energy absorption during landing with the need for a stable platform.
4. Medical Devices: Drug Delivery Systems
In medical devices, springs play a role in controlled drug delivery systems. The spring constant dictates the rate at which the drug is released, allowing for precise dosage control.
5. Consumer Electronics: Keyboards and Buttons
The tactile feedback of keyboards and buttons often relies on carefully chosen spring constants. The stiffness of the springs determines the force required to actuate the keys or buttons and influences the user experience.
Beyond Hooke's Law: Non-Linear Springs and Material Limitations
Hooke's Law provides an excellent approximation for many springs, particularly within their elastic limit. However, it's important to remember that this is a linear approximation. Beyond a certain point, the relationship between force and displacement becomes non-linear. This means that the spring constant is no longer constant and depends on the applied force or displacement.
Materials subjected to excessive stress can undergo permanent deformation, meaning they won't return to their original shape after the force is removed. This phenomenon is known as plastic deformation, and it marks the failure of the linear elastic model described by Hooke's Law. Beyond the elastic limit, the spring's behavior becomes complex and requires more advanced models to describe it accurately.
Conclusion: Mastering the Spring Constant for Engineering Success
Understanding the units of the spring constant, its dependence on material properties and geometry, and its numerous applications is crucial for anyone working with springs. While the simple equation F = kx provides a solid foundation, a deeper understanding of the underlying physics, material behavior, and limitations of the linear model is vital for tackling complex engineering problems. The N/m unit, representing the force per unit displacement, serves as a cornerstone for accurate spring calculations and design, ensuring functionality and safety across diverse applications. Furthermore, awareness of other unit systems and the ability to convert between them ensures consistent and effective communication in various engineering contexts.
Latest Posts
Latest Posts
-
Is Condensation Physical Or Chemical Change
Apr 18, 2025
-
In Which Scenario Is Gravitational Potential Energy Present
Apr 18, 2025
-
Determining The Enthalpy Of A Chemical Reaction Lab
Apr 18, 2025
-
The Problems Of Aggregate Inflation And Unemployment Are
Apr 18, 2025
-
Classify Each Monosaccharide According To The Position
Apr 18, 2025
Related Post
Thank you for visiting our website which covers about What Are The Units For A Spring Constant . We hope the information provided has been useful to you. Feel free to contact us if you have any questions or need further assistance. See you next time and don't miss to bookmark.