What Is The Center Of Distribution
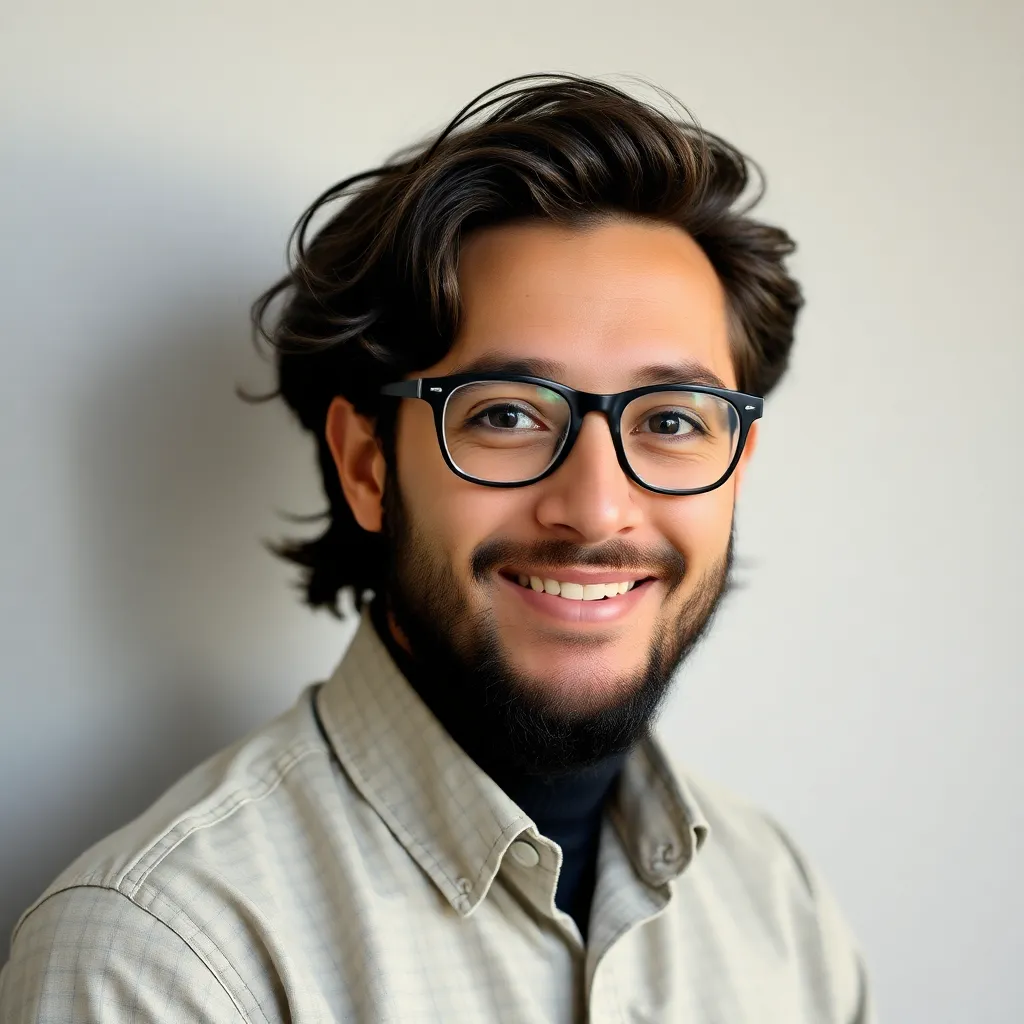
Muz Play
Apr 08, 2025 · 6 min read

Table of Contents
What is the Center of Distribution? A Comprehensive Guide
The center of distribution (COD), also sometimes referred to as a distribution center (DC) or fulfillment center, is the strategic heart of a company's logistics and supply chain operations. It's more than just a warehouse; it's a highly orchestrated system designed to efficiently receive, store, process, and distribute goods to various destinations. Understanding the intricacies of a COD is crucial for businesses of all sizes aiming to optimize their operations, enhance customer satisfaction, and gain a competitive edge. This comprehensive guide will delve deep into the concept of a COD, exploring its key functions, different types, and the critical factors influencing its successful operation.
Key Functions of a Center of Distribution
The core function of a COD is to act as a central hub for the flow of goods. This involves a complex interplay of various activities, seamlessly integrated to ensure smooth and efficient operations. Let's break down the key functions:
1. Receiving and Inbound Logistics:
This stage involves the careful management of incoming goods from suppliers. This includes:
- Receiving Inspection: Verifying the quantity and quality of incoming shipments against purchase orders. This step is crucial for identifying and addressing discrepancies early on.
- Put-Away: Efficiently storing received goods in designated locations within the COD. This often involves utilizing sophisticated inventory management systems (WMS) to optimize storage space and retrieval times.
- Dock Scheduling: Optimizing the arrival and unloading of trucks to minimize congestion and downtime. Advanced scheduling software can significantly improve efficiency in this area.
2. Storage and Inventory Management:
Efficient storage is paramount for maintaining optimal inventory levels. This includes:
- Inventory Control: Utilizing a robust inventory management system (WMS) to track inventory levels, locations, and movement within the COD. This ensures accurate information is readily available.
- Storage Optimization: Implementing strategies to maximize storage space and minimize wasted area. This could involve vertical storage, specialized racking systems, and careful product placement.
- Inventory Forecasting: Predicting future demand based on historical data and market trends to optimize inventory levels and avoid stockouts or excess inventory.
3. Order Processing and Fulfillment:
This is the core of the COD's operation, where orders are received, processed, and fulfilled.
- Order Management: Receiving and processing orders from various channels (online, retail, wholesale). This often involves integrating with different order management systems.
- Picking and Packing: Accurately selecting items from inventory based on customer orders and packaging them for shipment. This stage often employs techniques like wave picking, batch picking, or zone picking to optimize efficiency.
- Shipping and Outbound Logistics: Preparing shipments for dispatch, selecting carriers, generating shipping labels, and coordinating transportation. This also includes tracking shipments and managing returns.
4. Value-Added Services:
Many modern CODs offer a range of value-added services to enhance their offerings and customer satisfaction:
- Kitting and Assembly: Combining multiple items into kits or assembling products before shipment, often based on customer specifications.
- Labeling and Packaging Customization: Adding customized labels, packaging, or inserts to personalize the customer experience.
- Product Repair and Returns Management: Handling product returns, repairs, and replacements efficiently.
- Quality Control: Implementing quality checks at various stages of the process to ensure the accuracy and integrity of the products being shipped.
Types of Center of Distribution
CODs vary widely in size, design, and functionality depending on the specific needs of the business. Here are some common types:
1. Regional Distribution Centers:
These centers serve a specific geographic region, minimizing transportation costs and delivery times. They are often strategically located to optimize reach to a particular market.
2. National Distribution Centers:
These larger facilities serve a broader geographic area, often the entire nation. They typically handle a much larger volume of goods and require more sophisticated systems and processes.
3. Cross-Docking Centers:
These centers act as transfer points, where goods are unloaded from incoming shipments and immediately loaded onto outgoing shipments with minimal storage time. This minimizes inventory holding costs and speeds up delivery.
4. Omni-Channel Distribution Centers:
Designed to handle orders from multiple channels (online, retail, wholesale), these centers require flexible and integrated systems to manage inventory and fulfill orders efficiently across different platforms.
5. Specialized Distribution Centers:
These centers cater to specific product types requiring specialized handling and storage conditions, such as temperature-controlled facilities for perishable goods or secure facilities for high-value items.
Factors Influencing the Success of a Center of Distribution
The success of a COD hinges on several critical factors:
1. Location:
Choosing the right location is paramount. Factors to consider include proximity to transportation infrastructure (roads, railways, airports), labor costs, tax incentives, and access to target markets.
2. Technology and Automation:
Investing in advanced technology, such as Warehouse Management Systems (WMS), Transportation Management Systems (TMS), and automated guided vehicles (AGVs), can significantly improve efficiency and accuracy.
3. Layout and Design:
The physical layout of the COD must be optimized for efficient workflow, minimizing travel time and maximizing space utilization.
4. Inventory Management:
Effective inventory management is crucial for avoiding stockouts and excess inventory, ensuring accurate tracking, and minimizing holding costs.
5. Staff Training and Development:
Well-trained and motivated staff are essential for ensuring smooth and efficient operations. Continuous training and development programs are crucial for maintaining a skilled workforce.
6. Security:
Robust security measures are essential to protect inventory from theft and damage. This includes physical security measures, access controls, and surveillance systems.
7. Sustainability:
Increasingly, businesses are incorporating sustainability into their COD operations. This includes reducing energy consumption, minimizing waste, and using eco-friendly packaging.
The Future of Center of Distribution
The future of CODs is shaped by several emerging trends:
- Increased Automation: The adoption of robotics, automation, and AI is transforming COD operations, leading to greater efficiency and accuracy.
- Data Analytics and Predictive Modeling: Utilizing data analytics to optimize inventory levels, predict demand, and improve decision-making.
- E-commerce Growth: The continued growth of e-commerce is driving the need for more flexible and efficient CODs capable of handling high volumes of orders and diverse fulfillment requirements.
- Sustainability Initiatives: The increasing focus on sustainability is leading to the adoption of greener practices within CODs, including renewable energy sources, waste reduction, and eco-friendly packaging.
- Hyper-Personalization: The increasing demand for personalized experiences is leading CODs to adopt more sophisticated systems capable of handling customized orders and value-added services.
Conclusion: Optimizing Your Center of Distribution for Success
The center of distribution plays a vital role in the success of any business involved in the distribution of goods. By understanding its key functions, different types, and the factors that influence its success, businesses can optimize their operations, enhance customer satisfaction, and gain a competitive edge in the marketplace. Continuous adaptation to emerging trends and technologies will be critical for ensuring the future success of CODs in an increasingly dynamic and competitive landscape. Investing in the right technology, implementing robust processes, and fostering a culture of efficiency and continuous improvement are essential for maximizing the return on investment in your center of distribution. Remember, a well-managed COD is not merely a storage facility; it's the engine that drives your supply chain and ultimately, your business growth.
Latest Posts
Latest Posts
-
Is Theoretical Yield The Limiting Reactant
Apr 17, 2025
-
Clf Lewis Structure Polar Or Nonpolar
Apr 17, 2025
-
If Qc Is Greater Than Kc
Apr 17, 2025
-
A Positively Or Negatively Charged Particle
Apr 17, 2025
-
Electric Field Of A Charged Sphere
Apr 17, 2025
Related Post
Thank you for visiting our website which covers about What Is The Center Of Distribution . We hope the information provided has been useful to you. Feel free to contact us if you have any questions or need further assistance. See you next time and don't miss to bookmark.