Coefficient Of Thermal Expansion For Steel
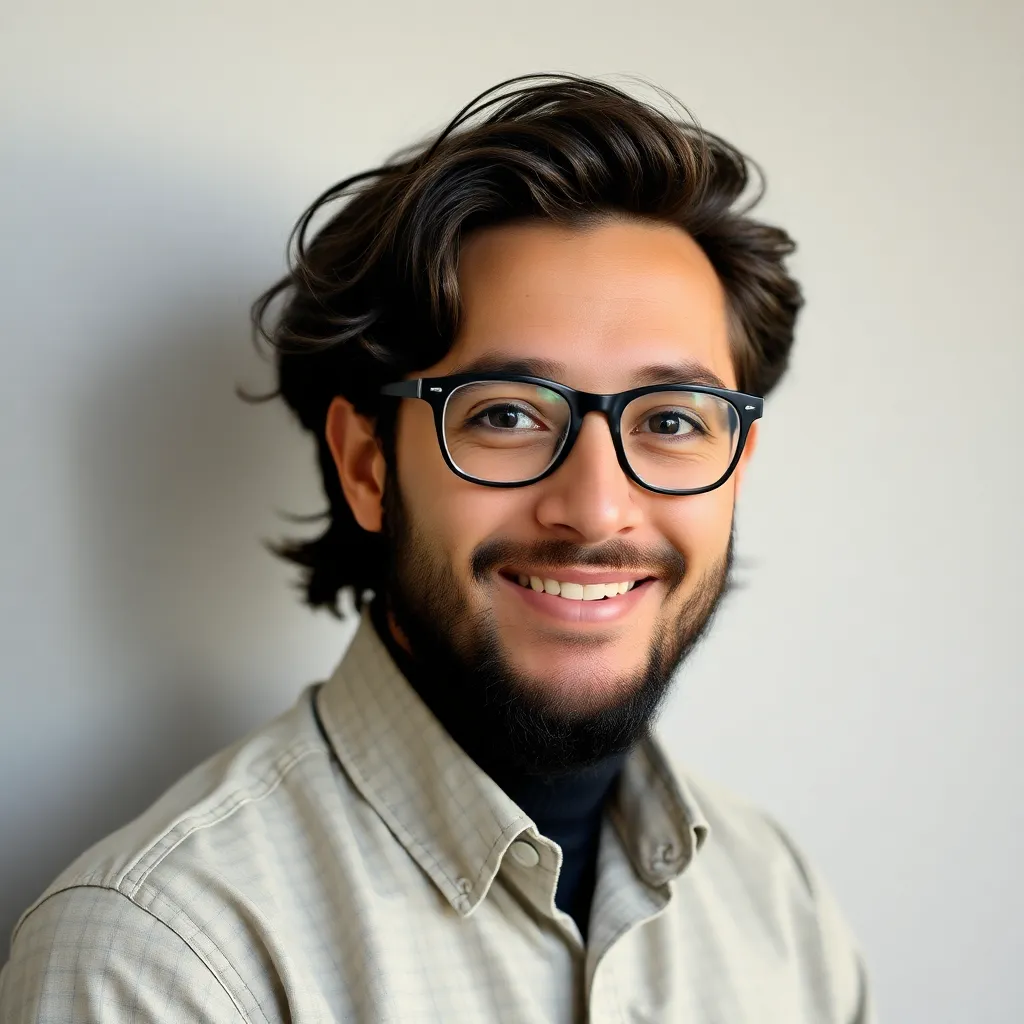
Muz Play
Mar 18, 2025 · 6 min read
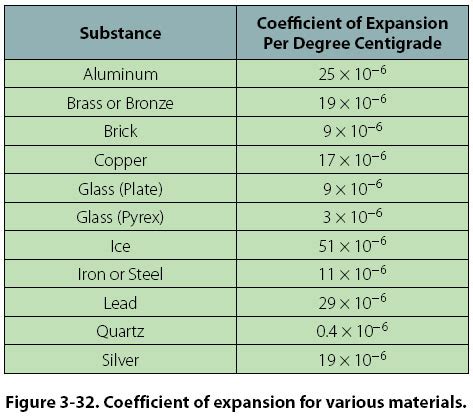
Table of Contents
Coefficient of Thermal Expansion for Steel: A Comprehensive Guide
Steel, a ubiquitous material in construction, manufacturing, and engineering, exhibits a crucial property known as the coefficient of thermal expansion (CTE). Understanding this property is paramount for designing and constructing structures and components that can withstand temperature fluctuations without experiencing significant dimensional changes or stress build-up. This comprehensive guide delves into the intricacies of the coefficient of thermal expansion for steel, exploring its definition, influencing factors, measurement techniques, and practical applications.
What is the Coefficient of Thermal Expansion (CTE)?
The coefficient of thermal expansion (CTE) quantifies the fractional change in size (length, area, or volume) of a material for a unit change in temperature. For steel, it represents how much its dimensions will change per degree Celsius (or Fahrenheit) of temperature increase or decrease. A higher CTE indicates a greater change in dimensions for a given temperature variation. This is a critical consideration in diverse applications, from bridges and skyscrapers to precision instruments and microelectronics.
Types of CTE
There are three main types of CTE:
-
Linear CTE (α): This describes the change in length per unit length per degree of temperature change. It's the most commonly used type for solid materials like steel. The formula is:
ΔL = αL₀ΔT
, where ΔL is the change in length, α is the linear CTE, L₀ is the original length, and ΔT is the temperature change. -
Area CTE: This measures the change in area per unit area per degree of temperature change. It's approximately twice the linear CTE (2α).
-
Volumetric CTE (β): This represents the change in volume per unit volume per degree of temperature change. It's approximately three times the linear CTE (3α).
Factors Influencing the CTE of Steel
The CTE of steel is not a constant value; it's influenced by several factors:
-
Steel Grade: Different steel grades possess varying compositions (alloying elements like carbon, manganese, chromium, nickel, etc.), which significantly affect their CTE. Higher carbon content generally leads to a slightly higher CTE. Stainless steels, with their higher alloy content, exhibit lower CTE values compared to carbon steels.
-
Temperature: The CTE itself is temperature-dependent. It's not strictly linear across a wide temperature range. At higher temperatures, the CTE tends to increase. This non-linearity needs to be accounted for in precise calculations, especially for applications involving significant temperature variations.
-
Phase Transformations: Steel undergoes phase transformations at specific temperatures (e.g., austenite to martensite). These transformations alter the crystal structure and, consequently, the CTE.
-
Microstructure: The microstructure of steel (grain size, grain orientation, etc.) influences its CTE. A finer grain size generally results in a slightly lower CTE.
-
Stress State: The presence of internal stresses within the steel can affect its apparent CTE. Residual stresses from manufacturing processes or external loads can alter the measured expansion or contraction.
-
Heat Treatment: Heat treatments like annealing, quenching, and tempering modify the microstructure and thus influence the CTE.
Measuring the CTE of Steel
Several methods are employed to measure the CTE of steel:
-
Dilatometry: This technique involves measuring the change in length of a steel sample as a function of temperature. A dilatometer precisely monitors the sample's expansion or contraction, providing accurate CTE data.
-
Interferometry: Interferometry utilizes the interference of light waves to measure extremely small changes in length. This is particularly useful for measuring CTE at high precision.
-
Thermomechanical Analysis (TMA): TMA is a technique that measures the dimensional changes of a material under the influence of temperature. It provides information on CTE and other thermomechanical properties.
-
X-ray Diffraction: X-ray diffraction can be used to determine the lattice parameters of the steel crystal structure. Changes in these parameters with temperature can be used to calculate the CTE.
Typical CTE Values for Steel
While the exact CTE varies depending on the factors mentioned above, typical values for common steel grades fall within a specific range. For carbon steels, the linear CTE at room temperature is approximately 11-13 x 10⁻⁶ /°C (or 6-7 x 10⁻⁶ /°F). Stainless steels generally exhibit lower CTE values, typically in the range of 9-17 x 10⁻⁶ /°C (or 5-10 x 10⁻⁶ /°F). High-strength low-alloy (HSLA) steels will have values that fall somewhere in between these ranges.
It's crucial to consult material datasheets and specifications provided by the steel manufacturer for the precise CTE value for a specific grade of steel used in a particular application.
Practical Applications and Considerations
Understanding the CTE of steel is essential in numerous engineering applications:
-
Structural Engineering: In designing bridges, buildings, and other structures, the CTE of steel needs to be considered to account for thermal expansion and contraction. Expansion joints are often incorporated to accommodate these dimensional changes and prevent stress build-up.
-
Mechanical Engineering: Machine components and precision instruments made of steel must be designed to function correctly despite temperature variations. The CTE influences the design of tolerances, clearances, and fits.
-
Automotive Industry: The CTE of steel plays a role in the design of automotive parts, ensuring proper functioning under diverse temperature conditions.
-
Aerospace Engineering: Aerospace structures experience significant temperature fluctuations during flight. The CTE of steel used in these structures needs to be carefully considered.
-
Welding: During welding, the heat input causes localized expansion and contraction. Understanding the CTE helps to predict and manage these thermal stresses and prevent defects like distortion and cracking.
Calculating Thermal Stresses
When steel is subjected to temperature changes, it experiences thermal strain. If this strain is constrained (e.g., a steel rod fixed at both ends), it leads to thermal stress. The stress can be calculated using the following formula:
σ = EαΔT
where:
- σ = thermal stress
- E = Young's modulus of steel
- α = linear CTE of steel
- ΔT = temperature change
Excessive thermal stresses can cause permanent deformation or even failure of steel components. Proper design considerations and measures, such as incorporating expansion joints or using materials with lower CTEs, are necessary to mitigate thermal stress.
Designing for Thermal Expansion: Best Practices
Several design practices help mitigate issues related to thermal expansion in steel structures:
-
Expansion Joints: These are incorporated into structures to allow for free expansion and contraction without inducing stresses.
-
Material Selection: Choosing steels with lower CTEs can reduce thermal expansion and associated stresses.
-
Pre-stressing: Pre-stressing can counteract thermal stresses by introducing initial compressive stresses.
-
Finite Element Analysis (FEA): FEA simulations can predict thermal stresses and deformations in complex structures.
-
Careful Design of Connections: The design of connections (welds, bolts, rivets) should account for thermal expansion and contraction.
Conclusion
The coefficient of thermal expansion is a critical property of steel that impacts its performance in diverse applications. Understanding the factors influencing the CTE, employing appropriate measurement techniques, and incorporating sound design practices are crucial for engineers to ensure the structural integrity and reliable functioning of steel components under various temperature conditions. Accurate knowledge of the specific CTE for a given steel grade is essential for precise calculations and effective design solutions. Failure to account for thermal expansion can lead to significant problems, from minor distortions to catastrophic failures. Through diligent consideration of CTE and the best design practices outlined here, engineers can mitigate the risks and build robust, durable, and long-lasting structures and components.
Latest Posts
Latest Posts
-
Find The Arclength Of The Curve
Mar 18, 2025
-
Which One Leaves The Solution Untouched
Mar 18, 2025
-
Which Statement Summarizes The Law Of Segregation
Mar 18, 2025
-
How Many Valence Electrons Does O3 Have
Mar 18, 2025
-
Why Do Solids Have A Definite Shape And Volume
Mar 18, 2025
Related Post
Thank you for visiting our website which covers about Coefficient Of Thermal Expansion For Steel . We hope the information provided has been useful to you. Feel free to contact us if you have any questions or need further assistance. See you next time and don't miss to bookmark.