During Manufacturing How Is The Resistivity Of A Resistor Changed
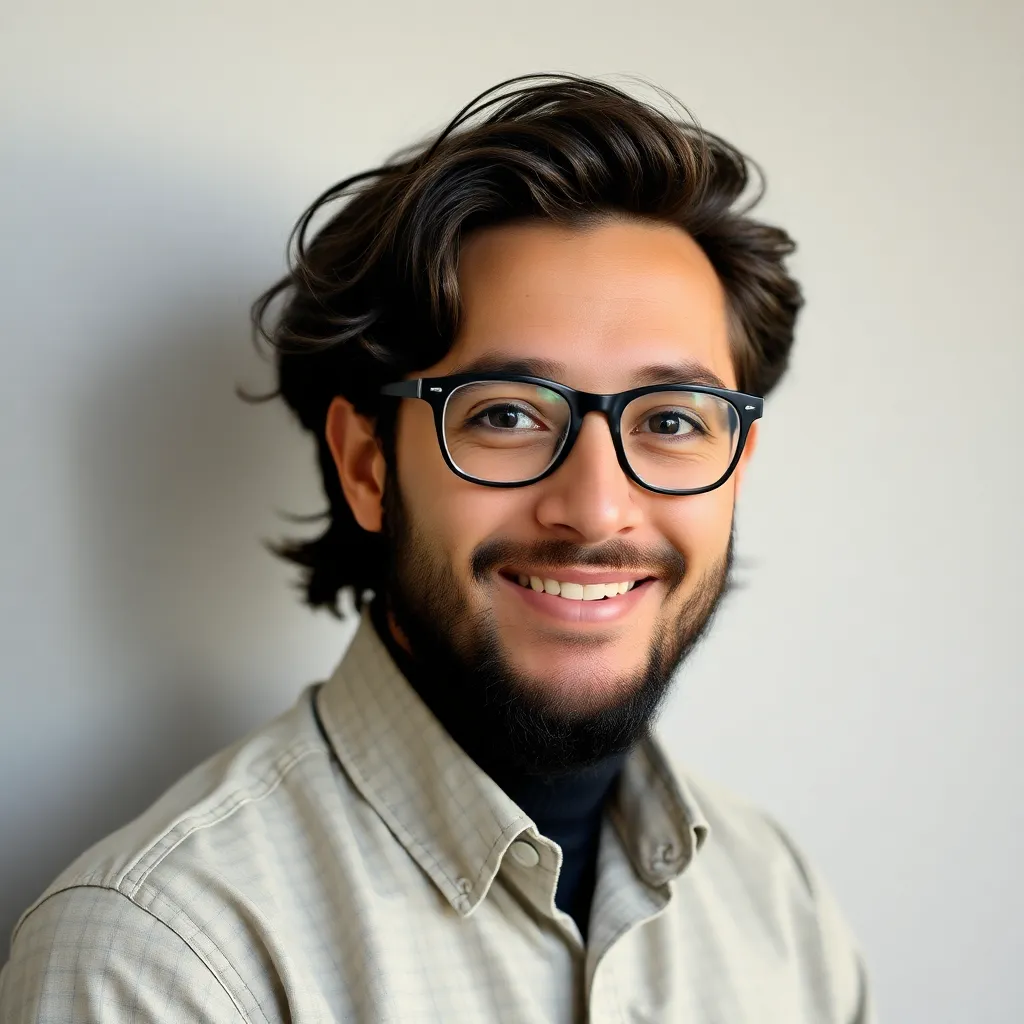
Muz Play
Apr 07, 2025 · 5 min read
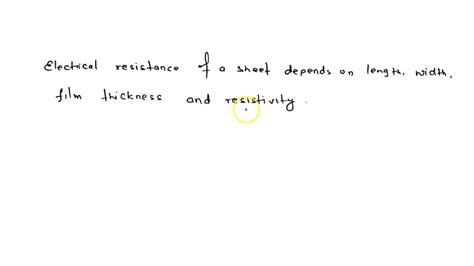
Table of Contents
Controlling Resistor Resistivity During Manufacturing: A Deep Dive
Resistors, seemingly simple passive components, play a crucial role in virtually every electronic circuit. Their primary function is to control current flow by offering resistance. This resistance, measured in ohms (Ω), is determined by the material's resistivity, geometry, and manufacturing processes. Understanding how resistivity is controlled during manufacturing is key to producing resistors with precise and stable values. This article delves into the intricacies of resistor manufacturing, focusing specifically on the methods used to manipulate resistivity and achieve the desired resistance.
The Fundamentals: Resistivity and Ohm's Law
Before diving into manufacturing techniques, let's revisit the fundamental relationship between resistance, resistivity, length, and cross-sectional area:
R = ρL/A
Where:
- R is the resistance (in ohms)
- ρ (rho) is the resistivity of the material (ohm-meters)
- L is the length of the resistor (in meters)
- A is the cross-sectional area of the resistor (in square meters)
This equation highlights that resistance can be altered by changing either the material's resistivity (ρ), the resistor's length (L), or its cross-sectional area (A). Manufacturers leverage all three to achieve the desired resistance value. However, controlling resistivity is often the primary method for achieving precise and consistent resistance values, especially at higher resistance values.
Material Selection: The Foundation of Resistivity Control
The choice of material fundamentally dictates the resistor's resistivity. Common materials include:
Carbon Composition Resistors:
These resistors utilize a mixture of carbon powder, a resin binder, and other additives. The ratio of carbon to binder is carefully controlled to determine the resistivity. A higher carbon concentration results in lower resistivity, and vice-versa. This method allows for a wide range of resistance values, but carbon composition resistors generally have lower precision and stability compared to other types.
Metal Film Resistors:
These resistors start with a ceramic substrate onto which a thin film of metal (e.g., nickel-chromium, or Nichrome) is deposited. The thickness of this metal film directly impacts resistivity. Thinner films have higher resistivity, while thicker films have lower resistivity. Furthermore, the composition of the metal alloy can be adjusted to fine-tune resistivity. The precise control offered by thin-film deposition techniques allows for higher precision and better stability compared to carbon composition resistors.
Thick Film Resistors:
Similar to metal film resistors, these use a ceramic substrate. However, instead of a thin film, a thick paste containing conductive particles (e.g., ruthenium oxide, bismuth ruthenate) and a glass binder is applied. The resistivity is controlled by the ratio of conductive particles to binder, as well as the firing temperature. Thick-film resistors offer a good balance between cost and performance, making them suitable for many applications.
Wirewound Resistors:
These resistors are made by winding a resistive wire (e.g., manganin, constantan) around a ceramic core. The resistivity of the wire is a primary factor determining the overall resistance. The length of the wire and the number of turns also influence the final resistance. Wirewound resistors are known for their high power handling capabilities and precision, but they are generally larger and more expensive than other types.
Manufacturing Processes: Fine-Tuning Resistivity
The manufacturing processes themselves contribute significantly to controlling the resistivity. Let's explore some key techniques:
Thin Film Deposition: Precise Resistivity Control
In metal film resistors, the thin film is deposited using techniques like:
- Sputtering: A physical vapor deposition (PVD) method where atoms are ejected from a target material and deposited onto the substrate. The sputtering parameters (e.g., gas pressure, voltage) can be carefully controlled to achieve the desired film thickness and hence, resistivity.
- Evaporation: Another PVD method where the material is heated until it evaporates and condenses on the substrate. Precise control of the evaporation rate and substrate temperature allows for accurate film thickness control.
- Chemical Vapor Deposition (CVD): A chemical reaction in the gas phase produces a solid film on the substrate. The gas flow rates and temperature influence the film's properties, including its resistivity.
Laser Trimming: Achieving Exact Resistance Values
Once the initial resistor is formed, laser trimming is often employed to fine-tune the resistance to its exact target value. A laser beam precisely removes small amounts of the resistive material, effectively increasing the resistance. This technique allows for incredibly precise control, ensuring the resistor meets its specified tolerance. The laser trimming process directly manipulates the effective length and cross-sectional area of the resistive element, thus indirectly altering the overall resistance as governed by the equation R = ρL/A.
Thick Film Screen Printing and Firing: Precise Paste Application
In thick film resistor production, a stencil is used to apply a precise amount of resistive paste to the substrate. The paste composition and the thickness of the printed layer determine the initial resistivity. Subsequent firing at high temperatures sinters the paste, further refining the resistive properties. Controlling the firing process is crucial to ensure consistent resistivity across batches.
Wire Winding: Length and Gauge are Key
For wirewound resistors, the length and gauge (diameter) of the resistive wire are paramount. The resistivity of the wire is inherent to its material, but the length and cross-sectional area (related to the gauge) can be adjusted to achieve the desired resistance. Precise winding techniques are essential to guarantee consistency and minimize variations in resistance.
Quality Control and Testing: Ensuring Consistent Resistivity
Throughout the manufacturing process, rigorous quality control measures are implemented to ensure the resistors meet their specifications. This includes:
- In-process monitoring: Real-time monitoring of parameters like film thickness, paste viscosity, and firing temperature to ensure consistency.
- Automated testing: Automated equipment measures the resistance of each resistor and rejects those outside the acceptable tolerance range.
- Environmental testing: Testing the resistors under various conditions (temperature, humidity, etc.) to ensure long-term stability.
Conclusion: A Symphony of Precision
Controlling the resistivity of a resistor during manufacturing is a complex process requiring careful attention to material selection, precise deposition and printing techniques, and rigorous quality control. The interplay between material resistivity, geometry, and manufacturing processes allows manufacturers to produce resistors with a wide range of resistance values, tolerances, and power ratings, catering to the diverse needs of modern electronics. From the careful blending of carbon particles in composition resistors to the laser-precise trimming of thin-film resistors, every step reflects a commitment to achieving reliable and consistent performance. The journey from raw materials to a precisely-calibrated resistor embodies a sophisticated understanding of materials science and manufacturing engineering, all aimed at delivering the essential components underpinning today's technology.
Latest Posts
Latest Posts
-
Write A Function In Standard Form
Apr 10, 2025
-
Row Vs Column Percentages Independent Variable
Apr 10, 2025
-
Which Molecule Is Expected To Have The Smallest Pka
Apr 10, 2025
-
How Many Electrons Are Shared In A Double Covalent Bond
Apr 10, 2025
-
When Do Ionic Compounds Conduct Electricity
Apr 10, 2025
Related Post
Thank you for visiting our website which covers about During Manufacturing How Is The Resistivity Of A Resistor Changed . We hope the information provided has been useful to you. Feel free to contact us if you have any questions or need further assistance. See you next time and don't miss to bookmark.