How To Compute Cost Per Equivalent Unit
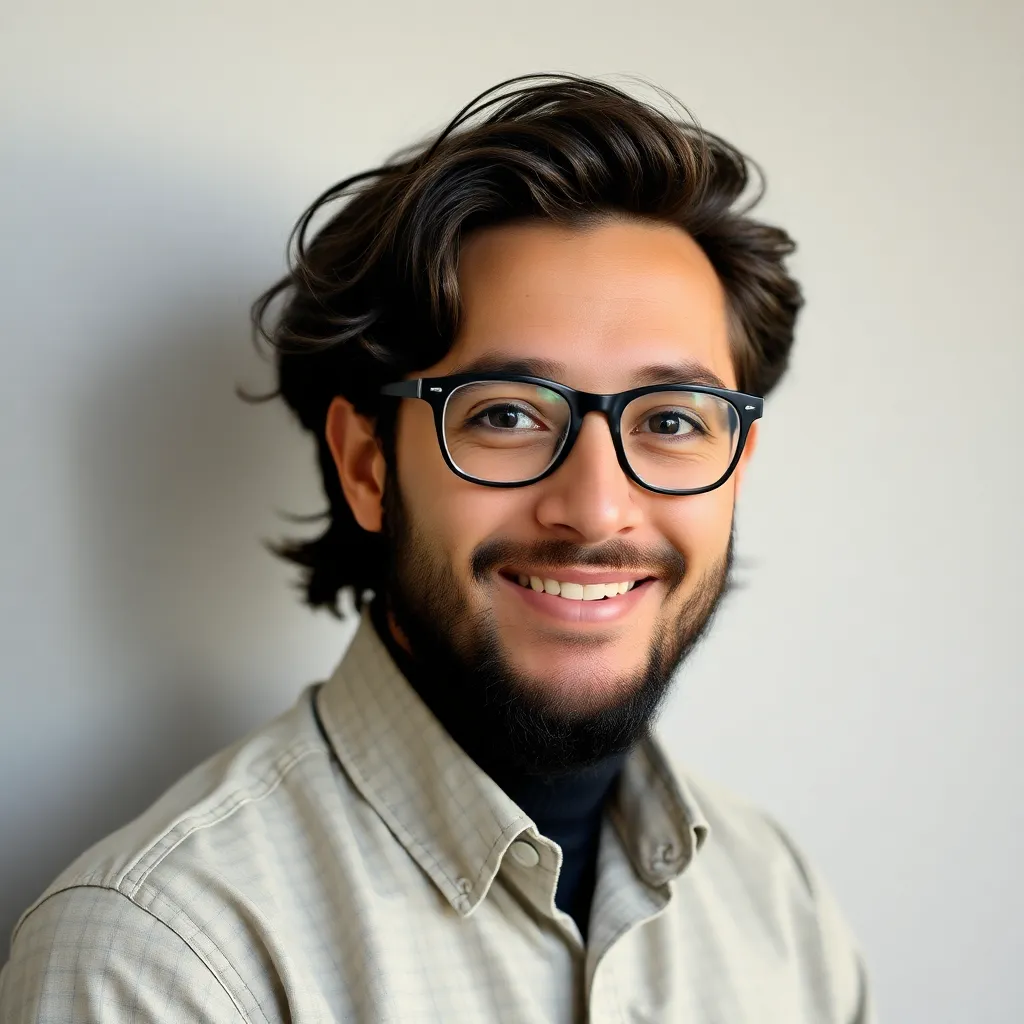
Muz Play
Mar 18, 2025 · 6 min read
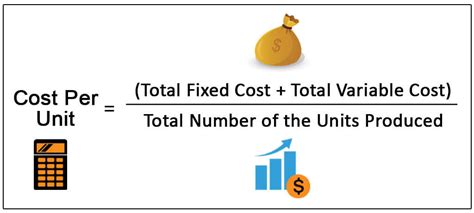
Table of Contents
How to Compute Cost Per Equivalent Unit: A Comprehensive Guide
Calculating the cost per equivalent unit (CPEU) is a crucial step in process costing, a method used to determine the cost of producing similar products or services in mass quantities. Understanding CPEU allows businesses to accurately track production costs, make informed pricing decisions, and identify areas for improvement in efficiency and resource allocation. This comprehensive guide will walk you through the process, covering various scenarios and offering practical examples.
What is Cost Per Equivalent Unit (CPEU)?
Cost per equivalent unit represents the cost of manufacturing one completed unit of a product. It's calculated by dividing the total manufacturing costs incurred during a period by the equivalent units produced during that same period. The key concept here is "equivalent units." These are the number of completed units expressed in terms of whole units, considering partially completed units as fractions of a whole. For example, a unit that's 50% complete is counted as 0.5 equivalent units.
Why is CPEU Important?
Accurate CPEU calculations are vital for several reasons:
- Inventory Valuation: CPEU is used to assign a cost to the work-in-progress (WIP) inventory and finished goods inventory. This is crucial for financial reporting purposes.
- Pricing Decisions: Understanding the cost per unit helps businesses set competitive and profitable prices for their products.
- Cost Control: By tracking CPEU over time, businesses can identify trends and areas where costs are escalating, allowing for timely intervention and cost reduction strategies.
- Performance Evaluation: CPEU can be used to assess the efficiency of the production process and identify bottlenecks.
- Decision Making: CPEU data helps in strategic decision-making, such as whether to invest in new equipment or adopt new production methods.
Steps to Calculate Cost Per Equivalent Unit
The calculation of CPEU involves several steps:
-
Identify Relevant Costs: Begin by identifying all costs directly related to the production process. These typically include:
- Direct Materials: Raw materials used in production.
- Direct Labor: Wages paid to production workers.
- Manufacturing Overhead: Indirect costs such as factory rent, utilities, and depreciation of equipment.
-
Calculate Equivalent Units of Production: This is arguably the most complex step. It requires analyzing the degree of completion of both beginning inventory and units started and completed during the period. We'll explore this in greater detail in the examples below.
-
Calculate Total Costs: Sum all the relevant costs identified in step 1.
-
Calculate Cost Per Equivalent Unit: Divide the total costs (step 3) by the equivalent units of production (step 2). This yields the CPEU.
Example: Calculating CPEU with Weighted-Average Method
The weighted-average method is commonly used to calculate CPEU. It considers both the beginning inventory costs and the costs incurred during the current period. Let's work through an example:
Scenario:
A company manufactures chairs. The following information is available for the month of July:
- Beginning WIP Inventory: 100 chairs (40% complete for materials, 60% complete for conversion costs)
- Units Started and Completed During July: 1000 chairs
- Ending WIP Inventory: 200 chairs (70% complete for materials, 30% complete for conversion costs)
- Direct Materials Costs: $2000 (beginning WIP) + $10,000 (during July) = $12,000
- Conversion Costs (Direct Labor + Manufacturing Overhead): $1500 (beginning WIP) + $7000 (during July) = $8500
Calculations:
Step 1: Equivalent Units of Production:
Materials | Conversion Costs | |
---|---|---|
Beginning Inventory: | 100 * 60% = 40 | 100 * 40% = 60 |
Units Started and Completed: | 1000 | 1000 |
Ending Inventory: | 200 * 70% = 140 | 200 * 30% = 60 |
Total Equivalent Units: | 1180 | 1120 |
Step 2: Total Costs:
- Total Direct Materials Costs: $12,000
- Total Conversion Costs: $8500
Step 3: Cost Per Equivalent Unit:
- CPEU for Materials: $12,000 / 1180 units = $10.17 per unit
- CPEU for Conversion Costs: $8500 / 1120 units = $7.59 per unit
Step 4: Cost Assignment:
Now we can use the CPEU to assign costs to the finished goods and ending WIP inventory. This is a complex calculation best done with a detailed spreadsheet.
Example: Calculating CPEU with FIFO Method
The First-In, First-Out (FIFO) method assigns costs to units based on their order of completion. It separately tracks the costs of beginning inventory and costs incurred during the current period. Let's adapt the previous example using FIFO:
Scenario (same as above):
- Beginning WIP Inventory: 100 chairs (40% complete for materials, 60% complete for conversion costs)
- Units Started and Completed During July: 1000 chairs
- Ending WIP Inventory: 200 chairs (70% complete for materials, 30% complete for conversion costs)
- Direct Materials Costs: $2000 (beginning WIP) + $10,000 (during July) = $12,000
- Conversion Costs (Direct Labor + Manufacturing Overhead): $1500 (beginning WIP) + $7000 (during July) = $8500
Calculations:
Step 1: Equivalent Units of Production (FIFO):
This is where the FIFO method differs significantly. We treat the beginning inventory separately.
- Beginning Inventory: The equivalent units from beginning inventory are accounted for separately.
- Materials: 100 chairs * (100% - 40%) = 60 equivalent units.
- Conversion Costs: 100 chairs * (100% - 60%) = 40 equivalent units.
- Units Started and Completed: 1000 chairs. (This is treated as fully completed.)
- Ending Inventory:
- Materials: 200 chairs * 70% = 140 equivalent units.
- Conversion Costs: 200 chairs * 30% = 60 equivalent units.
Materials | Conversion Costs | |
---|---|---|
Beginning Inventory (to complete): | 60 | 40 |
Units Started and Completed: | 1000 | 1000 |
Ending Inventory: | 140 | 60 |
Total Equivalent Units: | 1200 | 1100 |
Step 2: Cost Calculation (FIFO):
We need to allocate the costs separately. For beginning inventory, we only allocate the costs needed to complete these units.
- Materials Costs:
- Beginning Inventory: $2000 * (1-0.40) = $1200 (cost to complete)
- Current Period Costs: $10000
- Total Materials Cost: $11200
- Conversion Costs:
- Beginning Inventory: $1500 * (1-0.60) = $600 (cost to complete)
- Current Period Costs: $7000
- Total Conversion Costs: $7600
Step 3: Cost Per Equivalent Unit (FIFO):
- CPEU for Materials (FIFO): $11200 / 1200 units = $9.33 per unit
- CPEU for Conversion Costs (FIFO): $7600 / 1100 units = $6.91 per unit
This shows a different CPEU compared to the weighted-average method.
Choosing Between Weighted-Average and FIFO
The choice between the weighted-average and FIFO methods depends on several factors:
- Cost Accuracy: FIFO generally provides a more accurate reflection of costs, particularly in periods of fluctuating costs.
- Simplicity: The weighted-average method is simpler to calculate.
- Management Preferences: Some companies prefer the weighted-average method due to its simplicity.
It's crucial to choose a method and stick to it consistently for accurate comparisons over time.
Advanced Considerations in CPEU Calculation
- Multiple Departments: In complex manufacturing processes involving multiple departments, CPEU must be calculated for each department separately.
- Spoilage and Abnormal Losses: These must be accounted for and excluded from the calculation of equivalent units.
- Joint Products and By-products: These require specialized cost allocation methods beyond the scope of this basic guide.
- Software and Automation: Using accounting software simplifies the complex calculations inherent in process costing.
Conclusion
Computing the cost per equivalent unit is a fundamental aspect of process costing, providing invaluable insights into production costs and efficiency. While the calculations can be complex, a methodical approach, careful attention to detail, and a clear understanding of the chosen method (weighted-average or FIFO) will ensure accuracy. This information empowers businesses to make informed decisions regarding pricing, resource allocation, and overall profitability. Remember that consistency in your method is key for meaningful comparisons and analysis over time. Consult with an accounting professional for guidance on complex scenarios or if you require assistance in implementing process costing within your business.
Latest Posts
Latest Posts
-
What Is The Total Magnification Of 4x
Mar 18, 2025
-
The Cutaneous Membrane Is Blank To The Muscles
Mar 18, 2025
-
If A Hybrid Offspring Does Not Survive
Mar 18, 2025
-
5 Postulates Of Daltons Atomic Theory
Mar 18, 2025
-
How To Find Linear Relationship Between Independent And Dependent Variables
Mar 18, 2025
Related Post
Thank you for visiting our website which covers about How To Compute Cost Per Equivalent Unit . We hope the information provided has been useful to you. Feel free to contact us if you have any questions or need further assistance. See you next time and don't miss to bookmark.