Job Order Costing Vs Process Costing
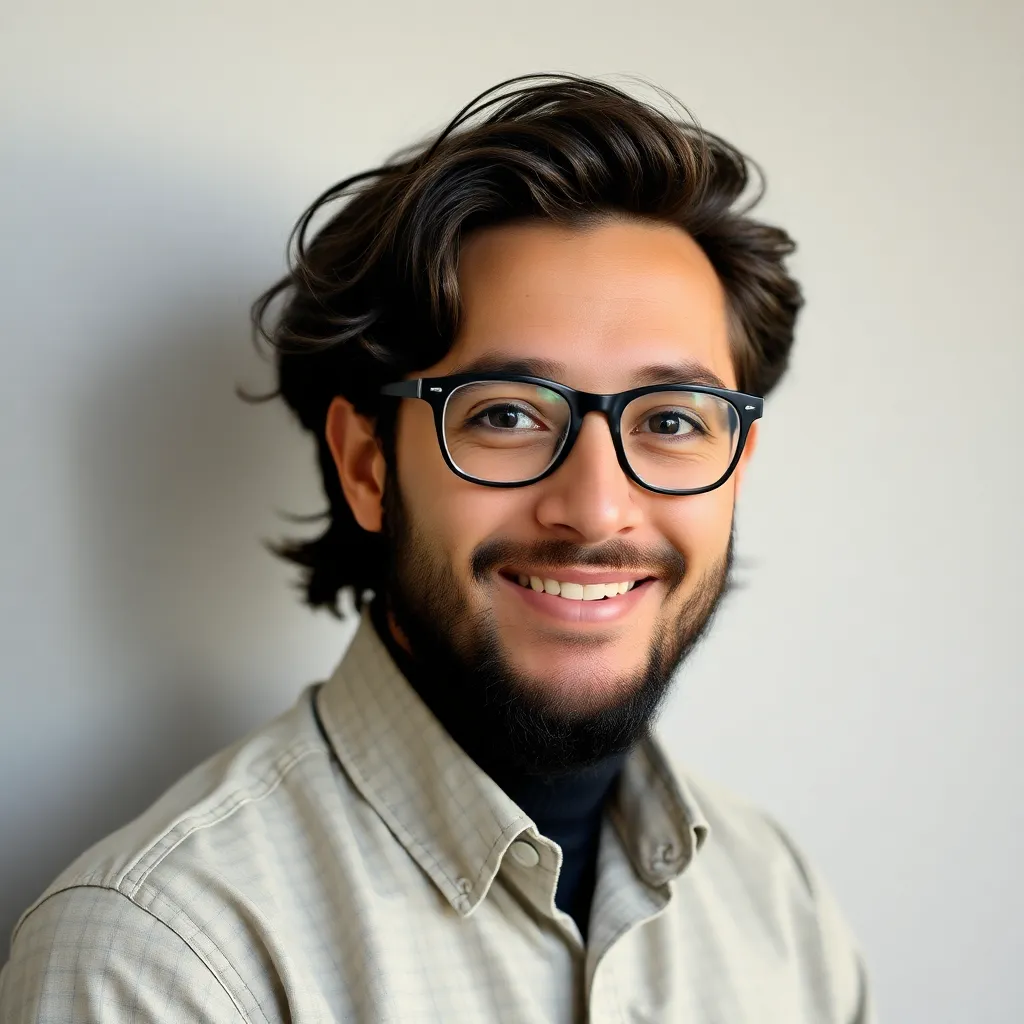
Muz Play
Mar 31, 2025 · 6 min read
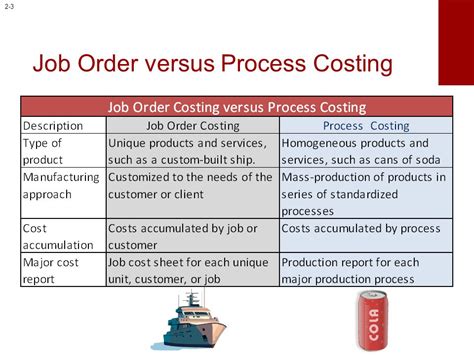
Table of Contents
Job Order Costing vs. Process Costing: A Comprehensive Guide
Choosing the right costing method is crucial for accurate financial reporting and effective business management. Two prominent methods are job order costing and process costing. Understanding their differences is vital for businesses to track costs effectively and make informed decisions. This comprehensive guide delves deep into the nuances of job order costing versus process costing, exploring their applications, advantages, disadvantages, and ultimately, helping you determine which method best suits your business needs.
What is Job Order Costing?
Job order costing is a costing method that assigns costs to individual projects or jobs. This approach is particularly suitable for businesses that produce unique or customized products or services, where each job has distinct characteristics and requires specific resources. Think of custom-made furniture, construction projects, specialized software development, or even bespoke tailoring. Each job is treated as a separate cost unit, allowing for precise cost tracking from inception to completion.
Key Characteristics of Job Order Costing:
- Individual Job Tracking: Costs are meticulously tracked for each individual job. This includes direct materials, direct labor, and overhead costs.
- Unique Products or Services: Ideal for businesses producing non-uniform, customized products or services.
- Detailed Cost Information: Provides detailed cost information for each job, facilitating pricing decisions and performance evaluation.
- Higher Administrative Costs: Requires more detailed record-keeping and administrative overhead compared to process costing.
How Job Order Costing Works:
- Job Cost Sheet: A job cost sheet is created for each job, acting as a central repository for all costs associated with that specific project.
- Direct Material Tracking: The costs of all materials directly used in the job are recorded on the job cost sheet.
- Direct Labor Tracking: Labor hours directly spent on the job, along with the associated labor rates, are meticulously recorded.
- Overhead Allocation: Manufacturing overhead costs (rent, utilities, depreciation) are allocated to each job based on a predetermined overhead rate. This rate is often calculated using a predetermined overhead rate based on a chosen allocation base (e.g., direct labor hours, machine hours).
- Cost Calculation: The total cost of the job is calculated by summing up the direct materials, direct labor, and allocated overhead costs.
- Pricing and Profitability Analysis: The total job cost is then used to determine the selling price, allowing for profit margin calculations and overall profitability assessment.
Examples of Industries Using Job Order Costing:
- Construction: Building a house or commercial building. Each project has unique specifications and costs.
- Custom Manufacturing: Creating specialized machinery or equipment tailored to customer needs.
- Printing: Producing personalized stationery or marketing materials for various clients.
- Advertising Agencies: Managing individual advertising campaigns for different clients.
- Legal Services: Tracking costs associated with individual legal cases.
What is Process Costing?
Process costing, in contrast to job order costing, is used to assign costs to products or services produced in a continuous or mass production process. This method is ideal for businesses manufacturing homogenous units in large quantities, where individual product differentiation is minimal. Think of food processing, chemical manufacturing, petroleum refining, or the production of standardized consumer goods.
Key Characteristics of Process Costing:
- Mass Production: Suitable for businesses producing large volumes of identical or nearly identical products.
- Averaging Costs: Costs are averaged across all units produced within a specific production period.
- Simplified Cost Tracking: Requires less detailed record-keeping than job order costing.
- Less Job-Specific Information: Provides less detailed cost information for individual units.
How Process Costing Works:
- Cost Accumulation: Costs are accumulated for each production department or process throughout a specific accounting period (e.g., month, quarter).
- Equivalent Units: The concept of equivalent units is crucial. These represent the number of completed units that could have been produced given the total input of resources, accounting for partially completed units.
- Cost per Equivalent Unit: The total cost for the period is divided by the total equivalent units to determine the cost per equivalent unit.
- Cost Assignment: The cost per equivalent unit is then multiplied by the number of completed units to assign costs to finished goods.
- Work-in-Process (WIP) Inventory: Costs associated with partially completed units are carried over as work-in-process inventory to the next accounting period.
Examples of Industries Using Process Costing:
- Food Processing: Manufacturing canned goods, packaged snacks, or beverages.
- Chemical Manufacturing: Producing plastics, fertilizers, or pharmaceuticals.
- Textile Manufacturing: Producing fabrics or clothing in large quantities.
- Oil Refining: Processing crude oil into various petroleum products.
- Paper Manufacturing: Producing different types of paper in a continuous process.
Job Order Costing vs. Process Costing: A Detailed Comparison
Feature | Job Order Costing | Process Costing |
---|---|---|
Type of Product | Unique, customized products or services | Homogenous, mass-produced products |
Cost Tracking | Individual job tracking | Cost averaging across units |
Cost Accuracy | High, detailed cost information for each job | Lower, less detailed cost information for each unit |
Record Keeping | More complex, detailed record-keeping | Simpler, less detailed record-keeping |
Administrative Costs | Higher | Lower |
Inventory Valuation | Costs assigned to specific jobs in inventory | Costs assigned to units in inventory based on average |
Suitability | Small-scale projects, custom orders, professional services | Large-scale production, continuous processes |
Example Industries | Construction, custom manufacturing, advertising | Food processing, chemical manufacturing, oil refining |
Choosing the Right Costing Method: Key Considerations
The optimal costing method depends heavily on the nature of your business and its production processes. Consider these factors:
- Product Homogeneity: If you produce highly similar units in large quantities, process costing is likely more suitable. If you produce unique or customized items, job order costing is preferred.
- Production Volume: Process costing excels in high-volume production environments. Job order costing is more appropriate for smaller volumes of unique projects.
- Complexity of Production: For complex projects with many individual components and varying labor inputs, job order costing offers better cost visibility.
- Degree of Customization: High customization necessitates job order costing, while standardized products benefit from process costing.
- Cost of Tracking: Consider the administrative costs associated with each method. Process costing generally has lower administrative costs, while job order costing requires more detailed tracking.
- Management Information Needs: Consider the level of detail required for decision-making. Job order costing provides detailed cost information for individual projects, while process costing provides an average cost per unit.
Hybrid Costing Systems
It's important to note that not all businesses strictly adhere to either job order costing or process costing. Some businesses may employ a hybrid costing system, combining elements of both methods to achieve a balance between accuracy and efficiency. This can be particularly useful for businesses that produce both standardized and customized products.
Conclusion: Optimizing Cost Accounting for Your Business
Ultimately, selecting the appropriate costing method is a crucial decision that impacts financial reporting accuracy, pricing strategies, and overall profitability. By carefully considering the nature of your products, your production processes, and your specific information needs, you can choose the costing method that best aligns with your business goals and ensures effective cost management. Remember, understanding the core principles of both job order costing and process costing equips you with the knowledge to make an informed decision, ultimately optimizing your cost accounting practices and driving your business towards success. Regular review and adjustments to your costing system are essential to ensure its continued relevance and effectiveness as your business grows and evolves.
Latest Posts
Latest Posts
-
Clonal Selection Of T Cells Happens In The Thymus
Apr 01, 2025
-
Formula Para Sacar Diametro De Un Circulo
Apr 01, 2025
-
How To Make A Frequency Histogram In Excel
Apr 01, 2025
-
What Is The Monomer Of A Dna Molecule
Apr 01, 2025
-
When Does The Segregation Of Alleles Occur
Apr 01, 2025
Related Post
Thank you for visiting our website which covers about Job Order Costing Vs Process Costing . We hope the information provided has been useful to you. Feel free to contact us if you have any questions or need further assistance. See you next time and don't miss to bookmark.