The Three Components Of Product Costs Are
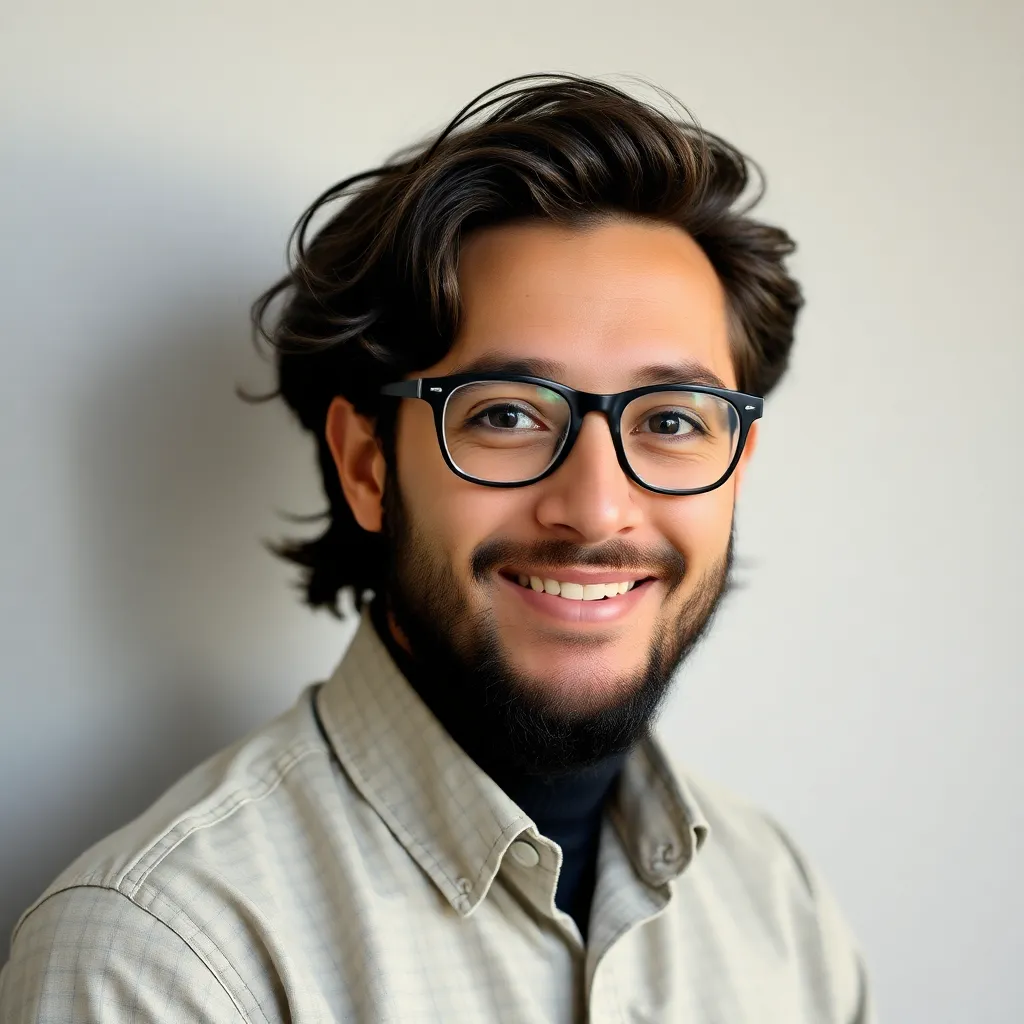
Muz Play
Apr 21, 2025 · 6 min read

Table of Contents
The Three Components of Product Costs: A Deep Dive for Businesses
Understanding product costs is crucial for any business, regardless of size or industry. Accurate cost accounting is not just about meeting accounting standards; it's the foundation for profitable pricing strategies, informed inventory management, and sound business decisions. This article will delve deep into the three core components of product costs: direct materials, direct labor, and manufacturing overhead, explaining each in detail and offering practical examples to illuminate their significance.
1. Direct Materials: The Raw Ingredients of Your Product
Direct materials represent the tangible raw materials that are directly incorporated into the finished product. These are the fundamental building blocks, easily traceable and quantifiable in terms of their contribution to the final output. Think of the flour, sugar, and eggs in a cake, the wood in a chair, or the steel in a car.
Identifying Direct Materials
The key characteristic distinguishing direct materials is their direct traceability to the finished product. This means you can easily and accurately link a specific amount of material to a specific unit of production. Consider these points:
- Physical Incorporation: The material must be physically part of the finished good.
- Measurable Quantity: The quantity used should be easily measurable and traceable.
- Direct Cost Attribution: The cost of the material should be directly attributable to the production of a specific product.
Examples of Direct Materials
- Manufacturing: Steel for cars, fabrics for clothing, wood for furniture, silicon for computer chips.
- Food & Beverage: Flour, sugar, milk, coffee beans, fruits, vegetables.
- Software: While less tangible, certain software components or licenses might be considered direct materials if they are directly incorporated into a larger software product.
Costing Direct Materials
Accurately costing direct materials requires careful tracking and documentation. Common methods include:
- First-In, First-Out (FIFO): This method assumes the oldest materials are used first.
- Last-In, First-Out (LIFO): This method assumes the newest materials are used first.
- Weighted-Average Cost: This method calculates an average cost based on the total cost of materials divided by the total quantity.
Choosing the appropriate method depends on various factors, including the nature of the inventory and the prevailing economic conditions. Accurate inventory management systems are essential for effective direct material cost tracking.
2. Direct Labor: The Human Touch in Production
Direct labor refers to the wages and benefits paid to employees who directly work on the production of goods. These are the individuals whose time and effort are directly traceable to the creation of the finished product. This contrasts with indirect labor, which we'll discuss under manufacturing overhead.
Identifying Direct Labor Costs
Similar to direct materials, direct labor costs are directly traceable to the production process. Key characteristics include:
- Direct Involvement: Employees must be directly involved in the manufacturing or production process.
- Time Tracking: Accurate time tracking is crucial for calculating the labor cost per unit.
- Wage & Benefit Inclusion: This encompasses not just wages but also employee benefits such as health insurance, retirement contributions, and paid time off.
Examples of Direct Labor
- Manufacturing: Assembly line workers, machinists, welders, carpenters, tailors.
- Food & Beverage: Bakers, chefs, butchers, brewers.
- Construction: Carpenters, electricians, plumbers, masons.
Calculating Direct Labor Costs
Accurate calculation involves considering:
- Hourly Wage Rates: The base hourly rate of pay for each employee.
- Overtime Premiums: Additional pay for work exceeding regular hours.
- Employee Benefits: The cost of employee benefits, often expressed as a percentage of wages.
- Labor Burden: This represents the total cost of employing an individual, including wages, benefits, and payroll taxes.
Effective labor cost management requires efficient scheduling, optimized workflows, and proper training to minimize downtime and maximize productivity.
3. Manufacturing Overhead: The Supporting Costs of Production
Manufacturing overhead encompasses all costs incurred in the production process that are not directly traceable to specific products. These are indirect costs that support the production process but aren't easily attributable to individual units.
Components of Manufacturing Overhead
Manufacturing overhead is a broad category encompassing a variety of indirect costs, including:
- Indirect Labor: Salaries and wages of employees who don't directly work on the product but support the production process (e.g., supervisors, maintenance personnel, quality control inspectors).
- Factory Rent and Utilities: Costs associated with the factory space, including rent, electricity, gas, and water.
- Depreciation on Factory Equipment: The allocation of the cost of factory equipment over its useful life.
- Factory Supplies: Consumable supplies used in the production process but not directly incorporated into the product (e.g., cleaning supplies, lubricants).
- Insurance and Property Taxes: Costs related to insurance and property taxes on the factory building and equipment.
- Factory Maintenance: Costs associated with maintaining and repairing factory equipment.
Allocating Manufacturing Overhead
Because manufacturing overhead costs are indirect, they must be allocated to individual products. Common methods include:
- Direct Labor Hours: Allocating overhead based on the number of direct labor hours used in production.
- Machine Hours: Allocating overhead based on the number of machine hours used in production.
- Direct Materials Cost: Allocating overhead based on the direct materials cost of the product.
- Predetermined Overhead Rate: This method involves calculating an estimated overhead rate at the beginning of the accounting period, based on projected overhead costs and a chosen allocation base.
Choosing the appropriate allocation method depends on the specific production environment and the nature of the overhead costs. The goal is to find a method that provides a reasonably accurate allocation of overhead costs to individual products.
The Importance of Accurate Product Costing
Accurate product costing is essential for several key reasons:
- Profitability Analysis: Understanding product costs is vital for determining profitability and setting appropriate selling prices. Without accurate cost data, businesses risk underpricing their products, losing potential profits, or overpricing, leading to lost sales.
- Inventory Valuation: Accurate product costing is crucial for valuing inventory, impacting the financial statements and influencing decisions related to inventory management.
- Pricing Strategies: Understanding costs allows for the development of informed pricing strategies, ensuring competitiveness and maximizing profitability.
- Cost Control: By tracking and analyzing product costs, businesses can identify areas for cost reduction and improve operational efficiency.
- Decision Making: Accurate cost data informs key business decisions, such as product mix, outsourcing, and investment in new equipment.
Beyond the Three Core Components: Considerations for a Comprehensive Cost Picture
While direct materials, direct labor, and manufacturing overhead form the bedrock of product costing, several other factors can influence the overall cost of production. These might include:
- Research and Development (R&D) Costs: These are costs associated with designing and developing new products. While not directly part of production, they contribute to the overall cost of bringing a product to market.
- Marketing and Sales Costs: These costs, while not directly related to production, are essential for selling the product. Understanding these costs is crucial for overall profitability analysis.
- Administrative Costs: General administrative overhead, including salaries of administrative staff, rent for office space, and other administrative expenses.
Conclusion: Mastering Product Costs for Business Success
Mastering the three components of product costs – direct materials, direct labor, and manufacturing overhead – is a critical skill for any business. By accurately tracking and analyzing these costs, businesses can make informed decisions about pricing, inventory management, and overall business strategy. Remember that accurate costing isn't just about complying with accounting standards; it’s about gaining a deep understanding of your business's financial health, empowering you to make strategic choices that drive profitability and long-term success. Regular review and refinement of your costing methods ensure they remain relevant and effective in a dynamic business environment. Continuous improvement in this area is a cornerstone of sustainable business growth.
Latest Posts
Latest Posts
-
Calculating Standard Reaction Free Energy From Standard Reduction Potentials
Apr 21, 2025
-
Step By Step Sliding Filament Theory
Apr 21, 2025
-
What Are The Three Steps In The Water Cycle
Apr 21, 2025
-
How Many Turns Of The Krebs Cycle Per Glucose
Apr 21, 2025
-
A Combination Of Variables Numbers And Operations
Apr 21, 2025
Related Post
Thank you for visiting our website which covers about The Three Components Of Product Costs Are . We hope the information provided has been useful to you. Feel free to contact us if you have any questions or need further assistance. See you next time and don't miss to bookmark.