The Three Major Cost Of Manufacturing A Product Are
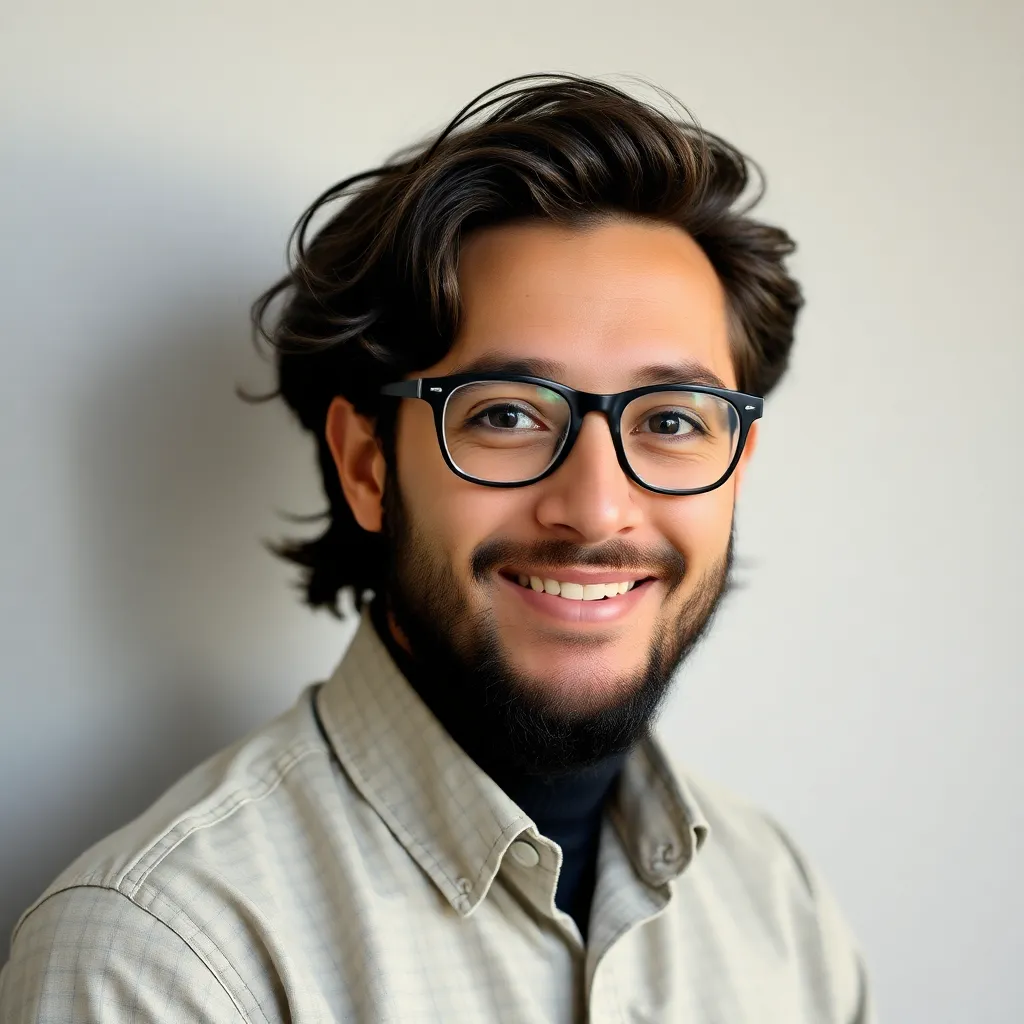
Muz Play
Apr 20, 2025 · 6 min read

Table of Contents
The Three Major Costs of Manufacturing a Product: A Deep Dive
Manufacturing a product, whether it's a simple widget or a complex piece of machinery, involves a multifaceted process with significant financial implications. Understanding the major cost components is crucial for businesses aiming to optimize profitability and remain competitive. While numerous expenses contribute to the overall manufacturing cost, three stand out as the most significant: direct materials, direct labor, and manufacturing overhead. Let's delve into each one, exploring their intricacies and providing strategies for effective cost management.
1. Direct Materials: The Foundation of Your Product
Direct materials represent the raw materials, components, and parts that are directly used in the production of a finished good. These are the tangible elements that physically become part of the final product. Think of the wood used in furniture making, the steel in automobile manufacturing, or the silicon in microchips. Accurate costing of direct materials is fundamental to accurate product pricing and profitability analysis.
Identifying Direct Materials
Identifying direct materials requires a meticulous approach. You need to clearly trace the usage of each material directly back to the finished product. This traceability is key for accurate cost accounting. Examples of direct materials include:
- Raw materials: These are the basic, unprocessed materials that undergo significant transformation during the manufacturing process. Examples include cotton for textiles, iron ore for steel, and crude oil for plastics.
- Purchased parts: These are pre-manufactured components that are incorporated into the final product without significant further processing. Examples include electronic components for consumer electronics, engine parts for automobiles, and screws and bolts for furniture.
- Packaging materials: While sometimes overlooked, packaging materials are crucial for product protection and presentation, and therefore constitute direct materials. Examples include boxes, cartons, labels, and films.
Managing Direct Material Costs
Controlling direct material costs requires a multi-pronged strategy:
- Supplier Relationship Management (SRM): Building strong relationships with reliable suppliers can lead to preferential pricing, bulk discounts, and timely delivery. Negotiating favorable contracts is paramount.
- Inventory Management: Implementing effective inventory control systems, such as Just-In-Time (JIT) inventory or Material Requirements Planning (MRP), minimizes storage costs and reduces the risk of obsolescence.
- Quality Control: Strict quality control procedures throughout the supply chain reduce waste from defective materials and minimize rework or scrap.
- Material Substitution: Exploring alternative materials with similar functionality but lower costs can significantly impact the bottom line. Thorough testing to ensure quality and performance is crucial.
- Waste Reduction Initiatives: Implementing lean manufacturing principles, such as 5S methodologies, can significantly reduce material waste during the production process.
2. Direct Labor: The Human Element in Production
Direct labor encompasses the wages, salaries, and benefits paid to employees directly involved in the manufacturing process. These are the individuals who physically transform raw materials into finished goods. This includes assembly line workers, machinists, welders, and other skilled tradespeople directly contributing to production. Accurate tracking of direct labor hours is critical for accurate costing and performance measurement.
Identifying Direct Labor Costs
Unlike direct materials, which are easily quantifiable, accurately tracking direct labor costs can be more challenging. This requires detailed record-keeping, including:
- Regular time wages: The base pay for employees working standard hours.
- Overtime pay: Compensation for hours worked beyond the standard workweek.
- Employee benefits: Costs associated with employee benefits, such as health insurance, retirement plans, and paid time off.
- Payroll taxes: Taxes levied on wages and salaries, such as Social Security and Medicare taxes.
Managing Direct Labor Costs
Effective management of direct labor costs requires a strategic approach:
- Workforce Planning: Accurate forecasting of labor requirements helps optimize staffing levels and avoid over- or understaffing.
- Employee Training and Development: Investing in employee training improves productivity, reduces errors, and minimizes waste. Skilled workers are more efficient and produce higher-quality output.
- Technology Implementation: Automating parts of the manufacturing process through robotics, automation, and other technologies can reduce labor costs while increasing efficiency.
- Process Optimization: Streamlining production processes, improving workflow, and eliminating bottlenecks can minimize the labor required to produce a unit of output.
- Incentive Programs: Implementing performance-based incentive programs can motivate workers to increase productivity and efficiency.
3. Manufacturing Overhead: The Indirect Costs of Production
Manufacturing overhead encompasses all indirect costs associated with the production process. These costs are not directly traceable to individual products but are essential for the overall manufacturing operation. They are often fixed costs, meaning they remain relatively constant regardless of production volume.
Components of Manufacturing Overhead
Manufacturing overhead includes a wide range of expenses:
- Indirect Labor: The wages and benefits paid to employees who support the production process but are not directly involved in transforming raw materials, such as supervisors, quality control inspectors, and maintenance personnel.
- Factory Rent and Utilities: Costs associated with the factory space, including rent, electricity, water, heating, and cooling.
- Depreciation and Amortization: The allocation of the cost of fixed assets, such as machinery and equipment, over their useful life.
- Factory Supplies: The cost of consumables used in the production process but not directly incorporated into the final product, such as cleaning supplies, lubricants, and tools.
- Insurance: Premiums paid for factory insurance, including property insurance and liability insurance.
- Maintenance and Repairs: The costs of maintaining and repairing factory equipment and facilities.
Managing Manufacturing Overhead Costs
Effectively managing manufacturing overhead requires a focused approach:
- Process Improvement: Identifying and eliminating waste in the production process can reduce overhead costs associated with indirect labor, utilities, and supplies.
- Negotiation: Negotiating favorable contracts with suppliers for utilities, maintenance, and insurance can lead to significant cost savings.
- Technology Optimization: Implementing energy-efficient technologies can reduce utility costs. Investing in robust equipment can minimize maintenance and repair costs.
- Preventive Maintenance: Regular preventative maintenance can help extend the life of equipment and reduce repair costs.
- Space Optimization: Efficient space utilization can reduce rent and utility costs.
Integrating the Three Costs: Cost Accounting Methods
Accurately determining the total cost of manufacturing requires integrating direct materials, direct labor, and manufacturing overhead. Several methods exist, each with its own advantages and disadvantages:
- Job Order Costing: This method tracks costs for individual jobs or projects. It's best suited for customized or unique products where each product requires a separate cost calculation.
- Process Costing: This method averages costs over a large number of identical products. It's ideal for mass production environments where products are nearly identical.
- Activity-Based Costing (ABC): ABC allocates overhead costs based on activities that drive the costs, providing a more accurate picture of cost drivers. It's particularly useful in complex manufacturing environments with diverse products.
Conclusion: A Holistic Approach to Cost Management
Understanding the three major costs of manufacturing – direct materials, direct labor, and manufacturing overhead – is paramount for successful manufacturing operations. By effectively managing each cost component through careful planning, strategic sourcing, process optimization, and the implementation of appropriate cost accounting methods, manufacturers can improve profitability, enhance competitiveness, and achieve sustainable growth. Continuous monitoring, analysis, and adaptation are crucial for navigating the ever-evolving landscape of manufacturing costs. Remember that proactive management and a commitment to efficiency are key to long-term success in this dynamic environment. The more precise your understanding, the better equipped you are to make informed decisions that drive your business forward.
Latest Posts
Latest Posts
-
Trabeculae And Spicules Are Found In
Apr 20, 2025
-
What Is Dissipated Energy In Physics
Apr 20, 2025
-
The Anova Test Assume The Samples Are Selected
Apr 20, 2025
-
Which Type Of Cell Is The Smallest
Apr 20, 2025
-
Which Of The Following Is A System That Helps Maintain
Apr 20, 2025
Related Post
Thank you for visiting our website which covers about The Three Major Cost Of Manufacturing A Product Are . We hope the information provided has been useful to you. Feel free to contact us if you have any questions or need further assistance. See you next time and don't miss to bookmark.