An Electrical Motor Provides 0.50 W Of Mechanical Power Quizlet
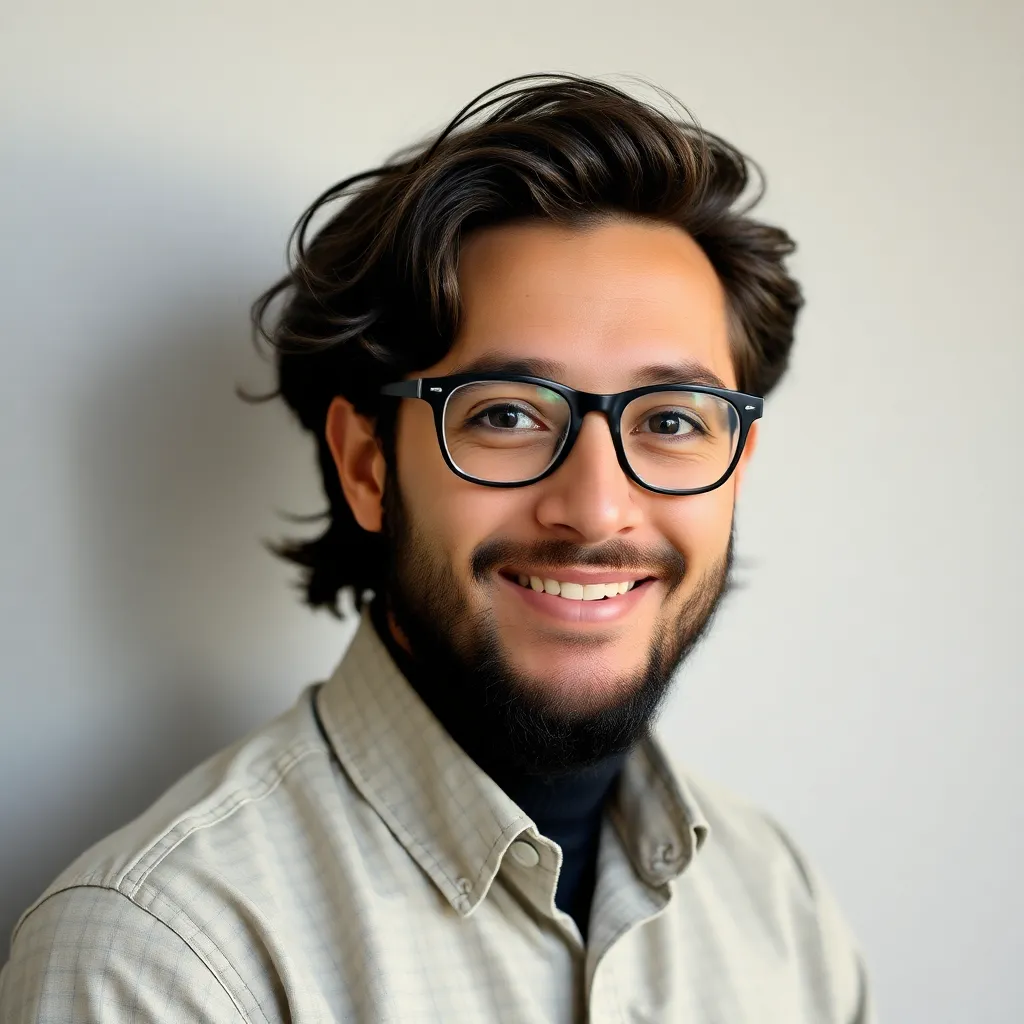
Muz Play
Apr 01, 2025 · 6 min read
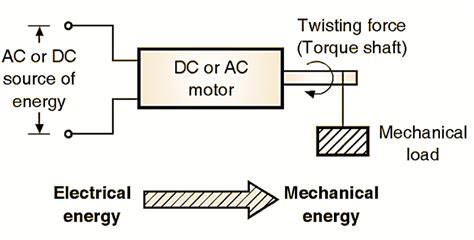
Table of Contents
Decoding the 0.50W Mechanical Power Output of an Electrical Motor: A Comprehensive Guide
An electrical motor converting electrical energy into mechanical work with a power output of 0.50W presents a fascinating case study in electromechanical energy conversion. This seemingly small power output has significant implications across various applications, from miniature robotics to low-power sensor systems. Understanding the factors contributing to this power output requires delving into the core principles of motor operation and efficiency. This article provides a comprehensive exploration of this topic, explaining the underlying physics, potential applications, and factors influencing the 0.50W output.
Understanding Electrical Motor Fundamentals
Before delving into the specifics of the 0.50W motor, it's crucial to establish a foundational understanding of how electrical motors work. At their heart, electrical motors utilize the interaction between magnetic fields and electric currents to generate rotational motion. This interaction is governed by the fundamental principles of electromagnetism, specifically Faraday's law of induction and Lorentz force.
Key Components and their Roles:
- Stator: The stationary part of the motor, containing the windings that generate the magnetic field. The stator's design significantly influences the motor's characteristics, including torque, speed, and efficiency.
- Rotor: The rotating part of the motor, interacting with the stator's magnetic field to produce mechanical rotation. The rotor's design also impacts the motor's performance.
- Commutator (for DC motors): A mechanical switch that reverses the current direction in the rotor windings, ensuring continuous rotation. AC motors utilize different mechanisms to achieve this alternating current.
- Windings: Coils of wire carrying electric current, generating magnetic fields. The number of windings, their arrangement, and the current flowing through them directly impact the motor's power output.
Power, Torque, and Speed: The Interplay in Motor Performance
The power (P) delivered by an electrical motor is intrinsically linked to its torque (τ) and rotational speed (ω). The relationship is defined by the equation:
P = τω
Where:
- P is the power in Watts (W)
- τ is the torque in Newton-meters (Nm)
- ω is the angular velocity in radians per second (rad/s)
A 0.50W motor operates at a specific torque and speed combination satisfying this equation. A higher torque will necessitate a lower speed for the same power output, and vice-versa. This trade-off is crucial in selecting a motor for a specific application. For example, a motor requiring high torque for starting heavy loads might operate at a relatively low speed, while a motor in a high-speed application like a fan might operate at lower torque.
Efficiency Considerations: Losses in the System
The actual mechanical power output of an electrical motor is always less than the electrical power input. This discrepancy is due to several energy losses within the motor itself:
- Copper Losses (I²R Losses): Resistance in the motor windings leads to heat generation, reducing the overall efficiency. These losses are proportional to the square of the current.
- Iron Losses (Hysteresis and Eddy Current Losses): These losses arise from the magnetization and demagnetization of the motor's core material. Hysteresis losses are related to the material's magnetic properties, while eddy current losses are due to induced currents in the core.
- Mechanical Losses (Friction and Windage): Friction in the bearings and air resistance contribute to mechanical losses, reducing the available mechanical power.
- Stray Load Losses: These are miscellaneous losses that are difficult to quantify, including losses due to leakage flux and other minor imperfections in the motor's construction.
These losses collectively reduce the overall efficiency (η) of the motor, defined as:
η = (Mechanical Power Output) / (Electrical Power Input)
A low power motor, like the 0.50W example, might exhibit lower efficiency due to the proportionally higher impact of these losses compared to higher-power motors.
Applications of 0.50W Motors: A Diverse Landscape
Despite their seemingly low power output, 0.50W motors find applications in a surprisingly wide range of situations, where their small size, low power consumption, and precise control are valuable:
- Miniature Robotics: These motors are ideal for powering small robotic actuators, allowing for fine-grained control and precise movements. Applications might include micro-robots for medical procedures, miniature drones, or educational robotics kits.
- Sensor Systems: Low-power sensor applications frequently utilize small motors for positioning sensors, adjusting focus, or performing other mechanical tasks. Examples include optical sensors, environmental monitoring systems, and various scientific instruments.
- Wearable Technology: The low power consumption of 0.50W motors makes them suitable for powering components in wearable devices, minimizing battery drain. Applications might include actuators for smartwatches, haptic feedback devices, or micro-pumps for drug delivery systems.
- Toys and Hobbies: Small motors with low power output are frequently used in model trains, remote-controlled vehicles, and other hobbyist applications.
- Automation and Control Systems: In industrial automation, smaller motors can handle delicate tasks requiring precise control and positioning.
Factors Affecting the 0.50W Output: Design and Operating Conditions
Several factors influence the mechanical power output of a 0.50W motor:
- Motor Type: Different motor types (DC brushed, DC brushless, AC induction, stepper, etc.) exhibit varying torque-speed characteristics and efficiencies. The selection of motor type significantly impacts the attainable power output.
- Voltage and Current: The applied voltage and the resulting current determine the power input to the motor. The efficiency of the motor dictates how much of this power is converted into useful mechanical power.
- Magnetic Field Strength: A stronger magnetic field leads to higher torque, potentially increasing the power output. However, this comes with increased losses in the motor's core.
- Motor Size and Construction: The physical dimensions and materials used in the motor's construction affect its efficiency and power output. Smaller motors generally have higher losses due to a higher surface area to volume ratio.
- Operating Temperature: Increased temperatures can reduce the motor's efficiency due to increased resistance in the windings and changes in the magnetic properties of the core material.
Analyzing the 0.50W Output: A Practical Example
Let's consider a hypothetical example: A 0.50W DC motor operates at a rotational speed of 1000 RPM (revolutions per minute). To determine the torque, we first convert the rotational speed to radians per second:
ω = (1000 RPM) * (2π rad/rev) * (1 min/60 s) ≈ 104.7 rad/s
Using the power equation (P = τω), we can calculate the torque:
τ = P/ω = 0.50 W / 104.7 rad/s ≈ 0.0048 Nm
This demonstrates that a 0.50W motor might only generate a small amount of torque, consistent with its low power rating. The specific torque and speed will vary considerably depending on the motor's design and operating conditions.
Conclusion: The Significance of Small Power Motors
The 0.50W electrical motor, though seemingly insignificant in terms of raw power, plays a critical role in a broad spectrum of modern technologies. Understanding its operational principles, efficiency limitations, and diverse applications highlights the importance of optimizing energy conversion in miniaturized systems. Further research and development in motor design and materials science can push the boundaries of efficiency, potentially leading to even smaller, more powerful, and energy-efficient motors for future applications. The 0.50W motor serves as a potent reminder of the remarkable capabilities embedded within even the smallest of electromechanical systems.
Latest Posts
Latest Posts
-
Write In Standard Form The Equation Of Each Line
Apr 02, 2025
-
What Does Fad Stand For In Biology
Apr 02, 2025
-
The Outermost Layer Of The Heart Is Called The
Apr 02, 2025
-
Which Of The Following Are Channels Of Nonverbal Communication
Apr 02, 2025
-
Express The Interval As An Inequality
Apr 02, 2025
Related Post
Thank you for visiting our website which covers about An Electrical Motor Provides 0.50 W Of Mechanical Power Quizlet . We hope the information provided has been useful to you. Feel free to contact us if you have any questions or need further assistance. See you next time and don't miss to bookmark.