List Of Equipments For Validation In Pharma And Biotech Industry
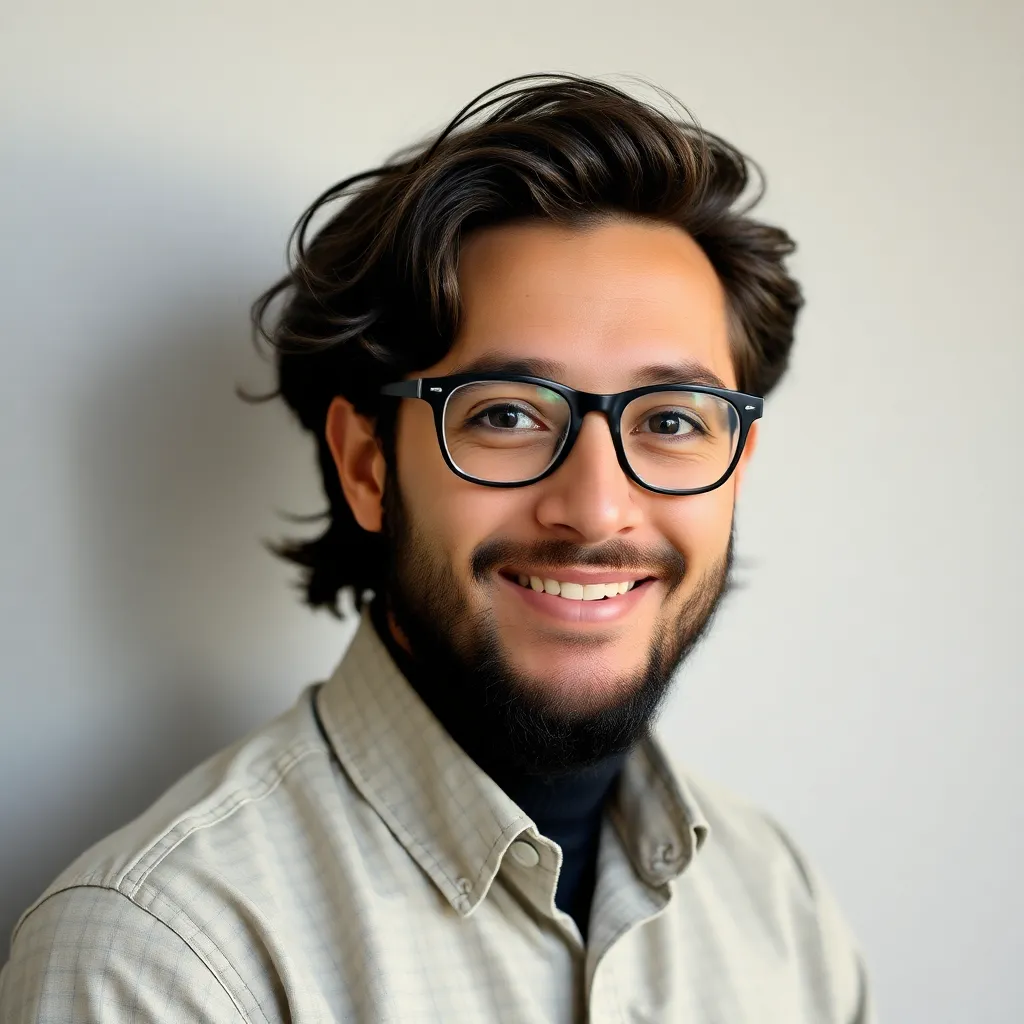
Muz Play
Mar 17, 2025 · 6 min read
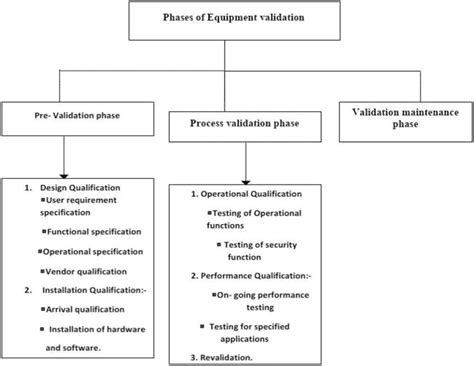
Table of Contents
- List Of Equipments For Validation In Pharma And Biotech Industry
- Table of Contents
- A Comprehensive List of Equipment for Validation in the Pharma and Biotech Industries
- I. Equipment for Manufacturing Processes
- A. Mixing and Blending Equipment
- B. Processing Equipment
- C. Filling and Packaging Equipment
- II. Equipment for Quality Control and Testing
- A. Analytical Instrumentation
- B. Environmental Monitoring Equipment
- III. Supporting Equipment Requiring Validation
- A. Cleanroom Equipment
- B. Data Handling and Storage Systems
- C. Utilities
- IV. Validation Considerations Across Equipment Types
- Latest Posts
- Latest Posts
- Related Post
A Comprehensive List of Equipment for Validation in the Pharma and Biotech Industries
The pharmaceutical and biotechnology industries operate under stringent regulatory requirements, mandating rigorous validation processes for all equipment impacting product quality, safety, and efficacy. This comprehensive guide provides a detailed list of equipment commonly requiring validation, categorized for clarity and enhanced understanding. We'll explore the specific validation parameters and considerations for each category.
I. Equipment for Manufacturing Processes
This section focuses on equipment directly involved in the production of pharmaceutical and biotech products. Validation ensures these systems consistently deliver expected performance, producing high-quality, safe, and efficacious products.
A. Mixing and Blending Equipment
- High Shear Mixers: Validation focuses on ensuring consistent mixing, shear rates, and temperature control. Critical parameters include torque, speed accuracy, and temperature uniformity throughout the mixing process. Documentation of cleaning validation is also crucial.
- Fluid Bed Dryers/Granulators: Validation should address uniform drying/granulation, consistent particle size distribution, and effective residence time distribution. Parameters include airflow rate, temperature profiles, and pressure variations. Cleaning validation protocols are essential.
- Ribbon Blenders: Validation protocols should verify consistent blending, achieving target homogeneity, and minimizing segregation. Critical parameters include rotational speed, mixing time, and the consistency of the final blend.
- Twin Shell Blenders: Similar to ribbon blenders, validation focuses on achieving homogenous blending. Key parameters include rotational speed, mixing cycles, and blend uniformity across the entire batch.
B. Processing Equipment
- Reactors (including Bioreactors): Validation is crucial for ensuring consistent reaction conditions, including temperature, pressure, agitation, and pH control. For bioreactors, parameters like dissolved oxygen levels, cell density, and nutrient feeding strategies are critical. Sterility validation is paramount.
- Centrifuges: Validation focuses on consistent separation efficiency, cake dryness, and the absence of cross-contamination. Parameters include speed, acceleration/deceleration profiles, and cycle times. Cleaning validation is also important.
- Filters (including membrane filters): Validation includes testing filtration efficiency, flow rates, and integrity testing. For sterile filtration, validation is essential for demonstrating the sterility assurance level. Documentation of filter integrity testing is crucial.
- Crystallizers: Validation focuses on achieving consistent crystal size and shape, yield, and purity. Parameters include temperature control, agitation, and seeding procedures.
- Dryers (including freeze dryers/lyophilizers): Validation addresses uniform drying, ensuring product quality and preventing degradation. For freeze dryers, parameters include chamber pressure, temperature ramps, and shelf temperature uniformity. Cycle development and validation are critical.
C. Filling and Packaging Equipment
- Filling Machines (liquid, powder, and semi-solid): Validation ensures accurate and consistent filling, minimizing variations in fill weight or volume. Parameters include fill accuracy, precision, and speed. Cleaning validation is essential.
- Sealing/Capping Machines: Validation focuses on the reliability of sealing or capping, preventing leaks or contamination. Parameters include torque, seal integrity, and leak testing procedures.
- Labeling Machines: Validation ensures accurate and consistent application of labels, including proper alignment and adhesion.
- Cartoners/Case Packers: Validation confirms proper carton or case formation, sealing, and filling, preventing damage or product loss.
II. Equipment for Quality Control and Testing
This section outlines the equipment essential for quality control testing to ensure the final product meets required specifications. Validation ensures the accuracy and reliability of these testing processes.
A. Analytical Instrumentation
- High-Performance Liquid Chromatography (HPLC): Validation focuses on demonstrating system suitability, accuracy, precision, linearity, and robustness. Methods must be validated to ensure accurate quantification and identification of analytes.
- Gas Chromatography (GC): Similar to HPLC validation, GC validation focuses on demonstrating system suitability and method accuracy. Specific parameters will vary depending on the application.
- Mass Spectrometry (MS): MS validation encompasses system suitability, method specificity, sensitivity, and linearity. Calibration and maintenance are critical aspects.
- Spectrophotometers (UV-Vis, IR): Validation ensures accuracy and precision in absorbance measurements. Wavelength accuracy, linearity, and stray light checks are vital.
- Titrators: Validation focuses on accuracy, precision, and repeatability in titration measurements. Calibration procedures are crucial.
- pH Meters: Validation addresses accuracy, precision, and response time. Regular calibration is essential for reliable measurements.
- Dissolution Testers: Validation ensures consistent and reliable dissolution testing according to regulatory guidelines. Parameters include rotational speed, temperature control, and sampling reproducibility.
- Particle Size Analyzers: Validation focuses on accuracy and repeatability in particle size distribution measurements.
- Microscopy (Optical, Electron): Validation, while less standardized than other analytical instruments, focuses on ensuring image quality and calibration for accurate particle analysis or identification.
B. Environmental Monitoring Equipment
- Particle Counters: Validation ensures accurate particle count and size distribution measurements within cleanrooms and controlled environments. Calibration and regular maintenance are critical.
- Microbial Air Samplers: Validation confirms sampling accuracy and reliability for microbial contamination monitoring. Calibration and filter integrity are important parameters.
- Water Purity Analyzers: Validation ensures accurate measurement of water quality parameters, including conductivity, pH, and total organic carbon (TOC).
- Temperature and Humidity Sensors: Validation addresses accuracy, precision, and response time for temperature and humidity monitoring throughout the facility.
III. Supporting Equipment Requiring Validation
This section covers equipment supporting manufacturing and quality control operations, but equally vital to consistent and reliable outcomes.
A. Cleanroom Equipment
- Autoclaves: Validation focuses on achieving sterility, including temperature and pressure profiles within the chamber. Biological indicators are essential for confirming sterility assurance.
- Depyrogenation Tunnels: Validation ensures effective removal of pyrogens, confirmed through appropriate endotoxin testing. Temperature profiles are vital.
- Cleanroom Pass-Through Chambers: Validation focuses on ensuring effective sterilization and airlocks to maintain cleanliness and prevent contamination.
- HVAC Systems: While not directly a piece of equipment, HVAC system validation is critical to ensure appropriate temperature, pressure, and airflow within cleanrooms.
B. Data Handling and Storage Systems
- Laboratory Information Management Systems (LIMS): Validation ensures data integrity, accuracy, and security.
- Chromatography Data Systems (CDS): Validation verifies data integrity and accurate reporting of chromatographic results.
- Manufacturing Execution Systems (MES): Validation is critical to ensure data integrity, traceability, and control throughout the manufacturing process.
C. Utilities
- Water Systems (Purified Water, Water for Injection): Validation is paramount for ensuring water meets all required quality parameters throughout the entire water system. Regular monitoring and testing are crucial.
- Compressed Gas Systems: Validation focuses on ensuring consistent gas purity and pressure.
- Steam Systems: Validation addresses temperature, pressure, and purity of steam used in sterilization and other processes.
IV. Validation Considerations Across Equipment Types
Regardless of the specific equipment, certain universal validation principles apply:
- Risk Assessment: A thorough risk assessment identifies critical parameters and potential failure modes, guiding the scope and depth of validation.
- Design Qualification (DQ): This stage verifies that the equipment design meets user requirements and regulatory standards.
- Installation Qualification (IQ): This verifies that the equipment was installed correctly and meets specifications.
- Operational Qualification (OQ): This demonstrates that the equipment performs as intended under specified conditions.
- Performance Qualification (PQ): This confirms that the equipment consistently delivers expected performance over time under normal operating conditions.
- Cleaning Validation: Demonstrates effective cleaning to prevent cross-contamination.
- Change Control: A formal process for managing changes to validated equipment and processes.
- Maintenance and Calibration: Regular maintenance and calibration are essential to maintain equipment performance and validation status.
- Documentation: Comprehensive documentation is essential for demonstrating compliance with regulatory requirements.
This detailed list and explanation of equipment validation in the pharmaceutical and biotech industries provides a comprehensive overview of the processes and equipment involved. Remember that specific validation requirements may vary depending on the equipment type, product being manufactured, and applicable regulatory guidelines. Always consult the relevant regulatory guidance and seek expert advice when developing validation protocols. Consistent, thorough validation is critical for ensuring product quality, safety, and regulatory compliance.
Latest Posts
Latest Posts
-
Solving Equations By Multiplying Or Dividing
Mar 18, 2025
-
Order Of Elution In Gas Chromatography
Mar 18, 2025
-
The Units Of Molar Mass Are
Mar 18, 2025
-
What Is The Conjugate Base Of Hcl
Mar 18, 2025
-
Normal Biota Of The Upper Respiratory Tract Include
Mar 18, 2025
Related Post
Thank you for visiting our website which covers about List Of Equipments For Validation In Pharma And Biotech Industry . We hope the information provided has been useful to you. Feel free to contact us if you have any questions or need further assistance. See you next time and don't miss to bookmark.