What Is Gas To Solid Called
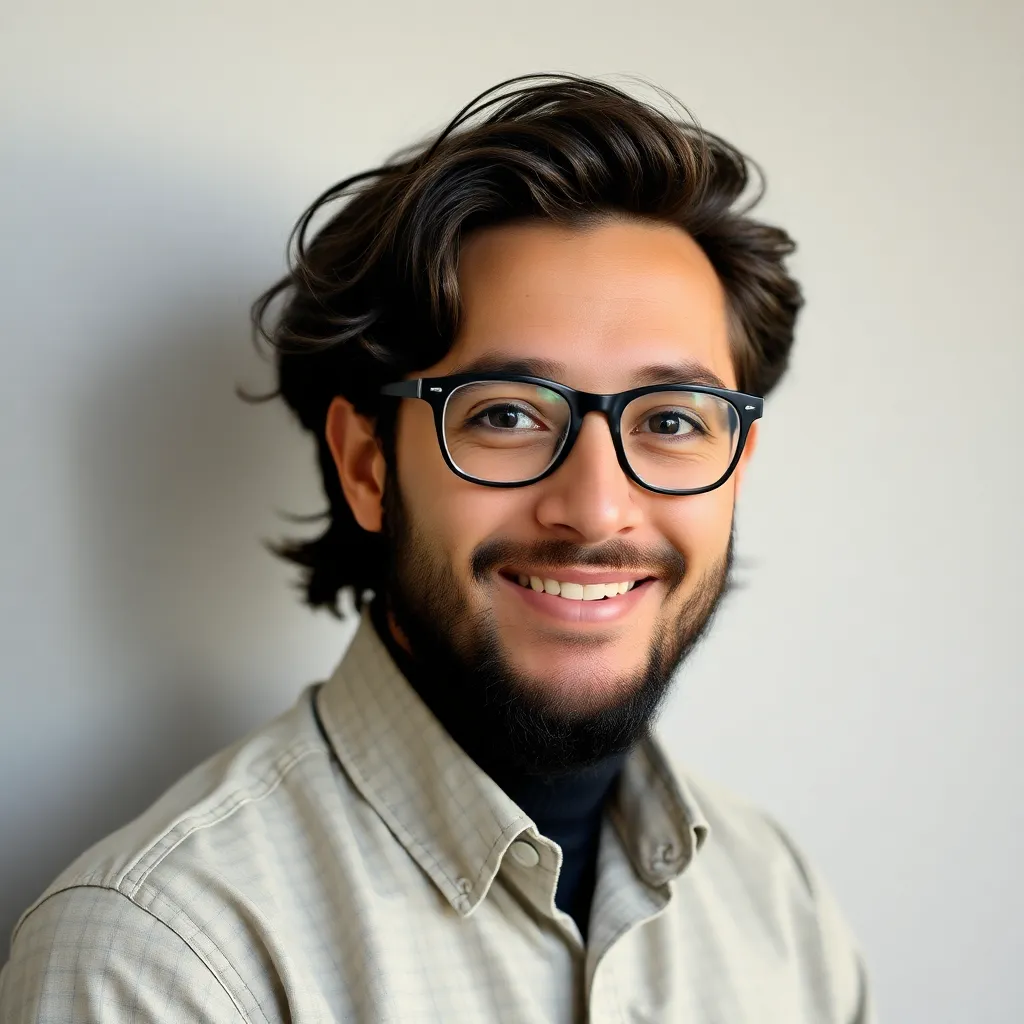
Muz Play
Mar 20, 2025 · 6 min read
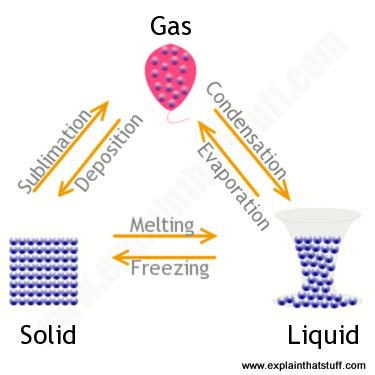
Table of Contents
What is Gas to Solid Called? Understanding Deposition and its Applications
The transformation of a gas directly into a solid state, bypassing the liquid phase, is a fascinating physical process with numerous applications across diverse scientific and technological fields. This phenomenon is known as deposition, and understanding its mechanisms and applications is crucial for advancements in various industries. This comprehensive article delves deep into the process of gas-to-solid conversion, exploring its underlying principles, various types, and widespread applications.
Understanding the Gas to Solid Transition: Deposition
Deposition, also referred to as desublimation or solid deposition, is a phase transition where a gas transforms directly into a solid without passing through an intermediate liquid phase. This occurs when the gas molecules lose sufficient kinetic energy to overcome the activation energy barrier for direct solid formation. This contrasts with condensation, where a gas transitions to a liquid first, and then potentially freezes into a solid.
The process is driven by the thermodynamic conditions, primarily temperature and pressure. When the temperature of a gas drops significantly below its triple point (the temperature and pressure at which solid, liquid, and gas phases coexist in equilibrium), the gas molecules lose kinetic energy, facilitating the formation of a solid crystalline structure.
Key Factors Influencing Deposition:
Several factors significantly impact the efficiency and quality of deposition:
-
Temperature: Lower temperatures generally favor deposition. A sufficiently low temperature is crucial for gas molecules to lose enough kinetic energy to overcome the activation barrier for direct solid formation.
-
Pressure: The pressure of the gas also plays a role. Higher pressures can lead to increased collision rates among gas molecules, enhancing the probability of nucleation and crystal growth. However, extremely high pressures might hinder the process.
-
Surface Properties: The surface onto which deposition occurs greatly influences the process. The surface's material, roughness, and temperature can affect nucleation and crystal growth rates. Smooth surfaces often lead to more uniform films.
-
Gas Purity: Impurities in the gas phase can significantly affect the quality and properties of the deposited solid. Impurities may inhibit crystal growth or lead to defects in the solid structure.
-
Rate of Cooling: The rate at which the gas is cooled impacts the crystal structure and morphology of the resulting solid. Rapid cooling might lead to amorphous or disordered structures, while slow cooling allows for better crystal ordering.
Types of Deposition Processes:
Several different methods are employed to achieve deposition, each with its own advantages and disadvantages depending on the application:
1. Physical Vapor Deposition (PVD):
PVD encompasses various techniques used to deposit thin films by transforming a solid material into a gaseous phase and subsequently condensing it onto a substrate. Common PVD techniques include:
-
Evaporation: The source material is heated in a vacuum until it vaporizes, then the vapor deposits onto the substrate. This is a relatively simple technique but may not be suitable for high-melting-point materials.
-
Sputtering: A target material is bombarded with ions, causing atoms to be ejected and deposited onto the substrate. This technique is versatile and can be used for a wide range of materials.
-
Molecular Beam Epitaxy (MBE): This is a highly controlled technique used for creating high-quality epitaxial thin films with precise layer-by-layer growth. It involves the precise control of molecular beams to deposit materials onto a crystalline substrate.
2. Chemical Vapor Deposition (CVD):
In CVD, gaseous precursors react on a heated substrate's surface, forming a solid deposit and releasing volatile byproducts. This technique is widely used for creating coatings and bulk materials. Different variations of CVD exist, including:
-
Metal-organic CVD (MOCVD): Uses metal-organic compounds as precursors.
-
Plasma-enhanced CVD (PECVD): Uses a plasma to enhance the reaction rate and lower the deposition temperature.
-
Atomic Layer Deposition (ALD): A self-limiting technique that deposits one atomic layer at a time, resulting in highly conformal coatings.
3. Freeze-Drying (Lyophilization):
Although not directly a gas-to-solid transition from a gaseous precursor, freeze-drying involves sublimation – the transition from solid to gas – and its reverse, deposition. It’s a crucial method in preserving biological materials. A frozen substance, often a solution, is placed under vacuum, and the ice sublimates directly to vapor, leaving behind a porous solid. This process avoids the damaging effects of high temperatures and helps maintain the integrity of sensitive biomolecules.
Applications of Deposition Processes:
Deposition techniques find extensive applications in various fields, including:
1. Semiconductor Industry:
Deposition is indispensable in semiconductor manufacturing. Thin films of various materials, such as silicon dioxide, silicon nitride, and metals, are deposited onto silicon wafers to create transistors, integrated circuits, and other electronic components. Techniques like CVD, PVD, and ALD are crucial in this industry.
2. Optics and Coatings:
Deposition plays a significant role in the fabrication of optical components and coatings. Anti-reflective coatings, high-reflectivity mirrors, and other specialized optical coatings are produced through techniques like CVD and PVD. These coatings improve the performance of optical instruments, lenses, and other optical devices.
3. Materials Science:
Deposition techniques are used to create novel materials with unique properties. Nanocomposites, thin films with specific electrical, magnetic, or optical properties, can be fabricated through controlled deposition processes. This area fuels innovation in areas like energy storage, catalysis, and sensors.
4. Biomedical Engineering:
Deposition is used in creating biocompatible coatings for medical implants, drug delivery systems, and tissue engineering scaffolds. Biocompatible materials are deposited to improve the integration of implants into the body and reduce the risk of rejection.
5. Food Industry:
While not as prevalent as in other industries, deposition principles can be applied in specialized food preservation techniques and coating processes. The concept relates to creating protective layers on food items to extend shelf life.
6. Environmental Remediation:
Specific deposition techniques can be used in environmental cleanup processes. This may involve depositing specific materials to absorb or neutralize pollutants.
7. Energy Applications:
Deposition plays a critical role in manufacturing solar cells, fuel cells, and batteries. Thin-film solar cells often utilize deposition techniques for creating layers of semiconductor materials. Fuel cell components also utilize deposition for creating catalytic layers and membranes.
Challenges and Future Directions:
Despite its widespread applications, deposition processes face some challenges:
-
Control of film uniformity and thickness: Achieving uniform and precise control over film thickness and quality remains a challenge, especially for large-scale applications.
-
Substrate compatibility: Choosing appropriate substrates that are compatible with the deposition process and the desired film properties is important.
-
Cost-effectiveness: Some deposition techniques, particularly those involving high vacuum or specialized equipment, can be expensive and energy-intensive.
-
Scale-up for mass production: Scaling up deposition processes to meet the demands of large-scale manufacturing can be complex and require significant technological advancements.
Future research will focus on:
-
Developing novel deposition techniques: Research is continually underway to develop new and more efficient deposition techniques that address the current limitations.
-
Improving process control and automation: Advanced automation and process control strategies will further enhance the precision and reproducibility of deposition processes.
-
Exploring new materials: Research is ongoing to explore new materials and their application in deposition processes, leading to the development of novel materials with enhanced properties.
-
Environmental impact reduction: Efforts to reduce the environmental impact of deposition processes, by decreasing energy consumption and minimizing waste generation, are essential.
In conclusion, deposition—the direct transition of a gas to a solid—is a fundamental physical process with profound implications across diverse fields. Understanding its underlying principles, diverse techniques, and wide-ranging applications is critical for innovation and advancements in various technologies. Ongoing research and development in this area continue to unlock new possibilities and push the boundaries of what's achievable through controlled gas-to-solid transformations.
Latest Posts
Latest Posts
-
N Type Vs P Type Semiconductor
Mar 21, 2025
-
This Type Of Reaction Requires Energy In Order To Proceed
Mar 21, 2025
-
Special Channels That Enable Water To Cross The Plasma Membrane
Mar 21, 2025
-
1 2 And 1 4 Addition
Mar 21, 2025
-
What Is A Signed Integer In Chemistry
Mar 21, 2025
Related Post
Thank you for visiting our website which covers about What Is Gas To Solid Called . We hope the information provided has been useful to you. Feel free to contact us if you have any questions or need further assistance. See you next time and don't miss to bookmark.