What Is The Middle Layer Of A Capacitor Made Of
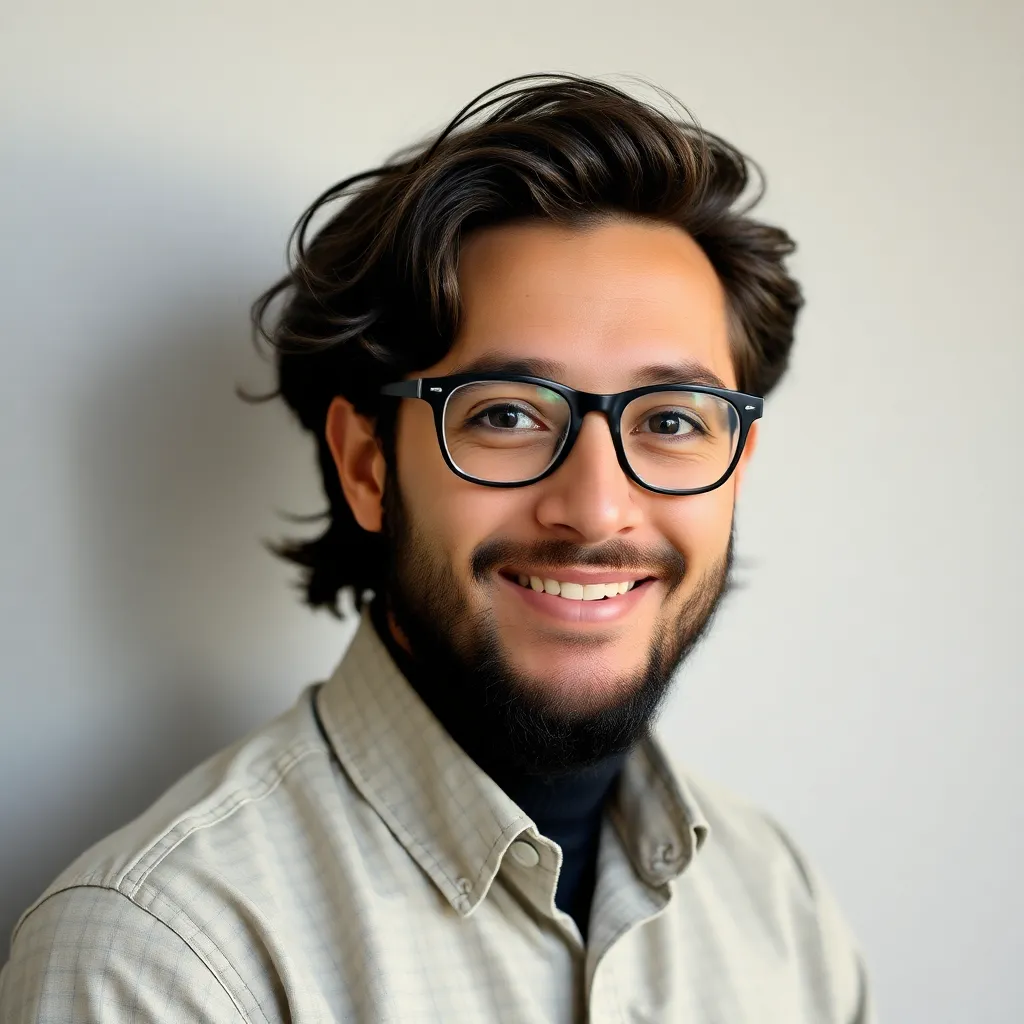
Muz Play
Mar 16, 2025 · 6 min read
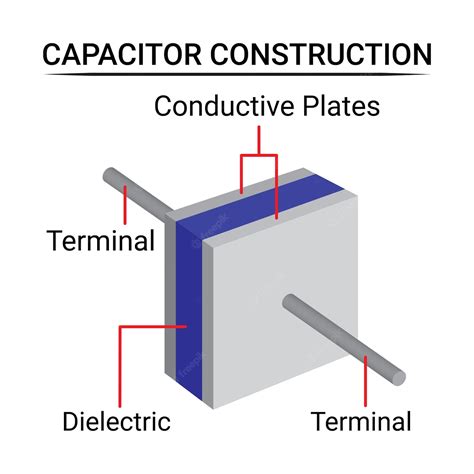
Table of Contents
What is the Middle Layer of a Capacitor Made Of? A Deep Dive into Dielectric Materials
Capacitors, those ubiquitous electronic components, are essential for countless devices. Their ability to store electrical energy makes them vital in everything from smartphones and computers to power grids and automobiles. But what makes a capacitor work? The answer lies within its core: the dielectric material forming the middle layer. This article delves deep into the composition and properties of various dielectric materials, exploring their impact on capacitor performance and application.
Understanding the Capacitor's Structure
Before we dive into the dielectric, let's briefly review the basic structure of a capacitor. A capacitor fundamentally consists of two conductive plates separated by an insulating layer—the dielectric. When a voltage is applied across the plates, an electric field develops within the dielectric, allowing the capacitor to store electrical charge. The ability to store charge is quantified by the capacitance, measured in Farads (F).
The key parameter determining a capacitor's capacitance is the dielectric constant (κ or ε<sub>r</sub>) of the insulating material. This constant represents the material's ability to store electrical energy within an electric field compared to a vacuum. Higher dielectric constants lead to higher capacitance for a given capacitor geometry.
The Heart of the Matter: Dielectric Materials
The choice of dielectric material significantly impacts a capacitor's characteristics, including its capacitance, voltage rating, temperature stability, frequency response, and lifespan. Numerous materials are employed, each offering a unique blend of properties suitable for specific applications.
1. Ceramic Dielectrics
Ceramic capacitors utilize ceramic materials as their dielectric. These are incredibly versatile, offering a wide range of capacitance values and voltage ratings. The specific properties depend on the ceramic composition. Common ceramic dielectric materials include:
-
Class 1 Ceramics: These possess high stability and low losses over a wide range of frequencies and temperatures. They're often used in applications requiring high precision and stability, such as resonant circuits and timing circuits. Typical compositions involve titanium dioxide (TiO₂) or mixtures of different ceramic compounds.
-
Class 2 Ceramics: These offer much higher capacitance values than Class 1 ceramics, but with reduced stability and increased losses. Their capacitance varies significantly with temperature and voltage. Barium titanate (BaTiO₃) is a commonly used material in Class 2 ceramics, often modified with other elements to tailor properties. These are frequently found in decoupling and bypass applications where high capacitance is crucial.
2. Film Dielectrics
Film capacitors employ thin films of polymeric or inorganic materials as their dielectric. These offer excellent stability and reliability, making them suitable for a wide range of applications. Common film dielectric materials include:
-
Polypropylene (PP): Known for its low dielectric loss and excellent high-frequency characteristics. Polypropylene film capacitors are used extensively in high-frequency circuits, RF applications, and audio circuits where high-frequency stability is crucial.
-
Polyester (PET): Offers a good balance of capacitance, voltage rating, and cost. Polyester film capacitors are widely used in general-purpose applications.
-
Polycarbonate (PC): Features high temperature stability and low dielectric absorption, making them suitable for demanding applications with stringent temperature requirements.
-
Metallized Film: In many film capacitors, the metal electrodes are not discrete plates but rather thin metal layers deposited directly onto the dielectric film. This construction reduces size and cost.
3. Electrolytic Dielectrics
Electrolytic capacitors are characterized by their extremely high capacitance values for a given size. This is achieved through the use of an electrolytic layer formed on the surface of one of the capacitor's electrodes. The formation of this layer is a critical part of the manufacturing process.
-
Aluminum Electrolytic Capacitors: These are the most common type of electrolytic capacitor, using a thin aluminum oxide layer as the dielectric. The manufacturing process involves electrochemical oxidation of the aluminum anode. They are known for their high capacitance but relatively lower voltage ratings and less stability compared to film capacitors.
-
Tantalum Electrolytic Capacitors: Tantalum electrolytic capacitors employ a tantalum pentoxide (Ta₂O₅) layer as the dielectric. They often exhibit better stability and higher temperature capabilities than aluminum electrolytic capacitors but are generally more expensive. The manufacturing process for tantalum capacitors is also electrochemical oxidation.
4. Mica Dielectrics
Mica capacitors utilize thin sheets of mica as their dielectric. Mica is a naturally occurring mineral with excellent dielectric properties, including high temperature stability and low dielectric loss. Mica capacitors are known for their exceptional stability and precision, but they are relatively expensive and have lower capacitance values compared to other types. They are frequently used in high-frequency and high-precision applications where stability is paramount.
5. Air Dielectrics
Air dielectric capacitors use air as the insulating material between the plates. These are simple in construction, featuring two conductive plates separated by a precisely controlled air gap. They possess high stability, low loss, and a wide frequency range, making them ideal for high-frequency applications and tuning circuits, though their capacitance values are usually low.
Factors Influencing Dielectric Choice
The selection of a dielectric material for a capacitor depends on several factors:
-
Capacitance: The required capacitance value significantly influences the dielectric choice. Electrolytic capacitors are preferred for high capacitance needs, while film or ceramic capacitors may be better suited for lower capacitance requirements.
-
Voltage Rating: The operating voltage of the circuit determines the required dielectric strength. Dielectrics with higher breakdown voltage are necessary for high-voltage applications.
-
Temperature Stability: The temperature range of operation dictates the stability of the dielectric. Class 1 ceramics and mica offer exceptional temperature stability, while Class 2 ceramics show more significant variation.
-
Frequency Response: For high-frequency applications, dielectrics with low dielectric loss are crucial to minimize signal attenuation. Polypropylene and mica are excellent choices in this regard.
-
Cost: The cost of the dielectric material is a practical consideration, influencing the overall cost of the capacitor.
-
Size and Physical Constraints: The required size and physical footprint of the capacitor can restrict the selection of dielectrics, influencing the choice between high capacitance density materials such as electrolytic capacitors versus lower density but potentially more compact film options.
Dielectric Properties and Their Impact on Capacitor Performance
The properties of the dielectric material directly impact the performance of the capacitor:
-
Dielectric Constant (κ): A higher dielectric constant allows for greater charge storage for the same physical size and voltage.
-
Dielectric Strength: This represents the maximum electric field the dielectric can withstand before breakdown occurs. Higher dielectric strength means the capacitor can handle higher voltages.
-
Dissipation Factor (DF or tan δ): This measures the energy loss in the dielectric due to internal friction. A lower dissipation factor indicates lower energy loss and better efficiency.
-
Dielectric Absorption: This refers to the capacitor's ability to retain charge after discharging. Lower dielectric absorption is desirable for applications requiring precise charge control.
-
Temperature Coefficient of Capacitance (TCC): This indicates how much the capacitance changes with temperature fluctuations. A low TCC is essential for applications requiring stable capacitance over a temperature range.
Conclusion
The middle layer of a capacitor—the dielectric—is a critical component determining its performance and application. The wide range of available dielectric materials, each with unique properties, allows for the design of capacitors tailored to specific needs. Understanding the characteristics and trade-offs of different dielectric materials is crucial for engineers selecting the appropriate capacitor for a given circuit design. The choice involves careful consideration of capacitance, voltage rating, temperature stability, frequency response, cost, and size constraints, all intricately linked to the specific properties of the dielectric material used. Further research into specific dielectric compositions and advanced capacitor technologies continues to push the boundaries of performance and efficiency.
Latest Posts
Latest Posts
-
Are Strong Bases Good Leaving Groups
Mar 17, 2025
-
Which Polymer Is Composed Of Amino Acids
Mar 17, 2025
-
According To Dalton Atoms Of Different Elements Will Be
Mar 17, 2025
-
Examples Of Essential And Nonessential Nutrients
Mar 17, 2025
-
Electric Potential From A Point Charge
Mar 17, 2025
Related Post
Thank you for visiting our website which covers about What Is The Middle Layer Of A Capacitor Made Of . We hope the information provided has been useful to you. Feel free to contact us if you have any questions or need further assistance. See you next time and don't miss to bookmark.