Coefficient Of Thermal Expansion Of Steel
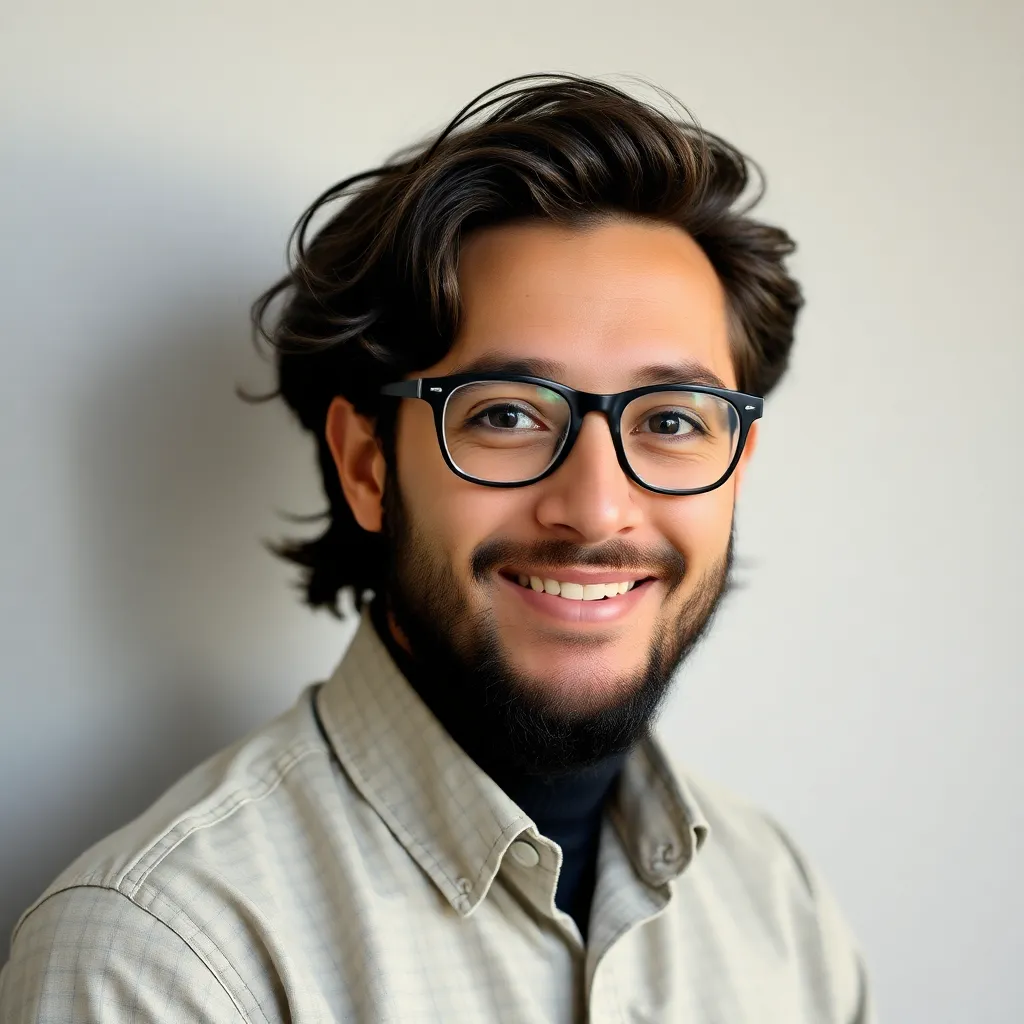
Muz Play
Mar 28, 2025 · 6 min read
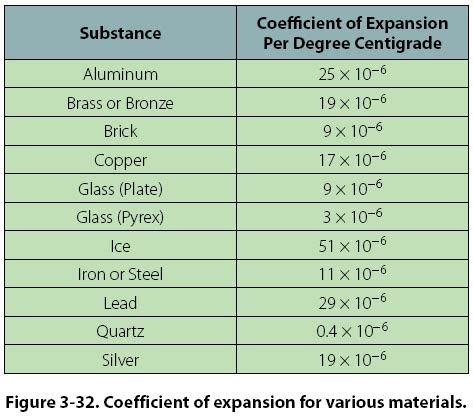
Table of Contents
Coefficient of Thermal Expansion of Steel: A Comprehensive Guide
The coefficient of thermal expansion (CTE) is a crucial material property, especially when dealing with engineering applications involving temperature variations. Steel, a ubiquitous material in construction, manufacturing, and numerous other industries, exhibits a distinct CTE that engineers must carefully consider to avoid issues like structural failure, component deformation, and performance degradation. This comprehensive guide delves into the intricacies of the coefficient of thermal expansion of steel, exploring its definition, influencing factors, measurement techniques, practical applications, and implications for various engineering disciplines.
Understanding the Coefficient of Thermal Expansion
The coefficient of thermal expansion quantifies the fractional change in size (length, area, or volume) of a material per degree change in temperature. For steel, this means how much its dimensions change for every degree Celsius (or Fahrenheit) increase or decrease in temperature. It's expressed as a value with units of per degree Celsius (°C⁻¹) or per degree Fahrenheit (°F⁻¹).
Linear Thermal Expansion: This is the most commonly used CTE for steel and refers to the change in length per unit length per degree change in temperature. It's represented by the symbol α (alpha). The formula for linear thermal expansion is:
ΔL = αL₀ΔT
Where:
- ΔL is the change in length
- α is the coefficient of linear thermal expansion
- L₀ is the original length
- ΔT is the change in temperature
Volumetric Thermal Expansion: This refers to the change in volume per unit volume per degree change in temperature. It's typically three times the linear thermal expansion coefficient (approximately, as it depends on material isotropy).
Factors Influencing the CTE of Steel
Several factors influence the precise CTE of a given steel:
1. Steel Grade and Composition:
The exact chemical composition of the steel significantly impacts its CTE. Different alloys, including carbon steel, stainless steel (austenitic, ferritic, martensitic), and high-strength low-alloy (HSLA) steels, possess varying CTE values. The presence of alloying elements like chromium, nickel, molybdenum, and manganese alters the crystal structure and bonding within the steel, thus affecting its thermal expansion behavior. For example, stainless steels generally have lower CTEs than carbon steels.
2. Temperature Range:
The CTE of steel isn't constant across all temperature ranges. It varies, sometimes significantly, depending on the temperature. At very low temperatures, the CTE might be lower, while at elevated temperatures, it could increase before possibly decreasing again at extremely high temperatures. Therefore, specifying the temperature range is crucial when referencing a steel's CTE.
3. Microstructure:
The microstructure of the steel, including grain size, phase distribution, and presence of precipitates, influences its CTE. A finer grain size generally leads to a slightly lower CTE. Heat treatments, such as annealing, quenching, and tempering, can significantly alter the microstructure and consequently the CTE.
4. Phase Transformations:
Steel undergoes phase transformations at specific temperature ranges (e.g., austenite to ferrite). These transformations are accompanied by changes in volume and can drastically affect the CTE. Understanding these phase transitions is critical for accurate CTE prediction, particularly in applications involving high temperatures.
5. Residual Stresses:
Internal residual stresses within the steel, introduced during manufacturing processes like welding or rolling, can influence the measured CTE. These stresses can either enhance or suppress thermal expansion, leading to variations in the observed CTE.
Measurement Techniques for CTE of Steel
Several techniques are employed to determine the CTE of steel:
1. Dilatometry:
This is a common technique where a sample of steel is heated or cooled at a controlled rate, and its length change is precisely measured using a dilatometer. This allows for the determination of the CTE over a wide temperature range.
2. Interferometry:
This optical method uses interference patterns to measure extremely small changes in length, providing high precision in CTE determination. It's particularly useful for measuring CTE at high temperatures.
3. X-ray Diffraction:
This technique determines the lattice parameters of the steel crystal structure at different temperatures. By analyzing the changes in lattice parameters, the CTE can be calculated. This method is valuable for studying CTE at the atomic level.
4. Thermal Mechanical Analysis (TMA):
TMA involves measuring the dimensional changes of a material under controlled temperature conditions. It can provide information on CTE, as well as other thermal properties such as glass transition temperature and softening point.
Applications and Implications of Steel's CTE
The CTE of steel plays a significant role in various engineering applications:
1. Structural Engineering:
In building design, bridges, and skyscrapers, the CTE of steel needs to be considered to account for thermal expansion and contraction due to temperature fluctuations. Expansion joints are incorporated into structures to accommodate these changes and prevent damage. Ignoring thermal expansion can lead to significant stresses within the structure, potentially causing cracking or failure.
2. Mechanical Engineering:
In the design of machinery and mechanical components, thermal expansion needs careful consideration. Mismatches in CTE between different materials in a component can cause warping, binding, or premature failure. For example, in engine design, the differential expansion of various metal components must be accounted for to ensure proper function and prevent damage.
3. Aerospace Engineering:
Aerospace structures experience significant temperature variations during flight. The CTE of the steel used in aircraft and spacecraft components must be carefully selected to minimize thermal stresses and ensure structural integrity. Lightweight, high-strength steels with carefully controlled CTEs are crucial for aerospace applications.
4. Civil Engineering:
In railway track design, the expansion and contraction of steel rails due to temperature changes are accounted for through the use of expansion gaps between rail sections. These gaps prevent buckling and ensure smooth train operation.
5. Automotive Engineering:
Automotive components often experience significant temperature changes during operation. Understanding the CTE of the steel used in engine blocks, chassis components, and other parts is crucial to preventing warping, deformation, and failure.
Practical Considerations and Design Implications
Several practical considerations arise when dealing with the CTE of steel in design and engineering:
- Material Selection: Choosing the appropriate steel grade with the desired CTE is crucial for the specific application and temperature range.
- Thermal Stress Analysis: Finite element analysis (FEA) is frequently used to predict thermal stresses and deformations in steel components under varying temperature conditions.
- Design for Thermal Expansion: Incorporating expansion joints, clearances, and other design features to accommodate thermal expansion is essential to prevent component failure.
- Pre-stressing: Pre-stressing techniques can be applied to compensate for thermal expansion and reduce stresses in certain applications.
- Temperature Compensation: In some precision instruments and applications, temperature compensation mechanisms are used to minimize the effects of thermal expansion.
Conclusion
The coefficient of thermal expansion of steel is a critical material property with significant implications for engineering design across various industries. Understanding its dependence on steel grade, temperature range, and microstructure is essential for avoiding structural failure, component deformation, and performance degradation. Accurate measurement techniques, coupled with careful consideration of thermal stress analysis and design for thermal expansion, are crucial for ensuring the successful and reliable performance of steel components in diverse engineering applications. The continued development of new steel alloys with tailored CTE values will further enhance the performance and durability of steel structures and components in increasingly demanding environments. This understanding allows engineers to create robust and reliable systems that can withstand the effects of temperature variations.
Latest Posts
Latest Posts
-
The Energy Needed To Start A Chemical Reaction Is Called
Mar 31, 2025
-
Person In Environment In Social Work
Mar 31, 2025
-
What Is The Funnel Used For
Mar 31, 2025
-
Chains Of Carbon Atoms Bonded To Hydrogen Atoms
Mar 31, 2025
-
How To Write Compounds In Chemistry
Mar 31, 2025
Related Post
Thank you for visiting our website which covers about Coefficient Of Thermal Expansion Of Steel . We hope the information provided has been useful to you. Feel free to contact us if you have any questions or need further assistance. See you next time and don't miss to bookmark.